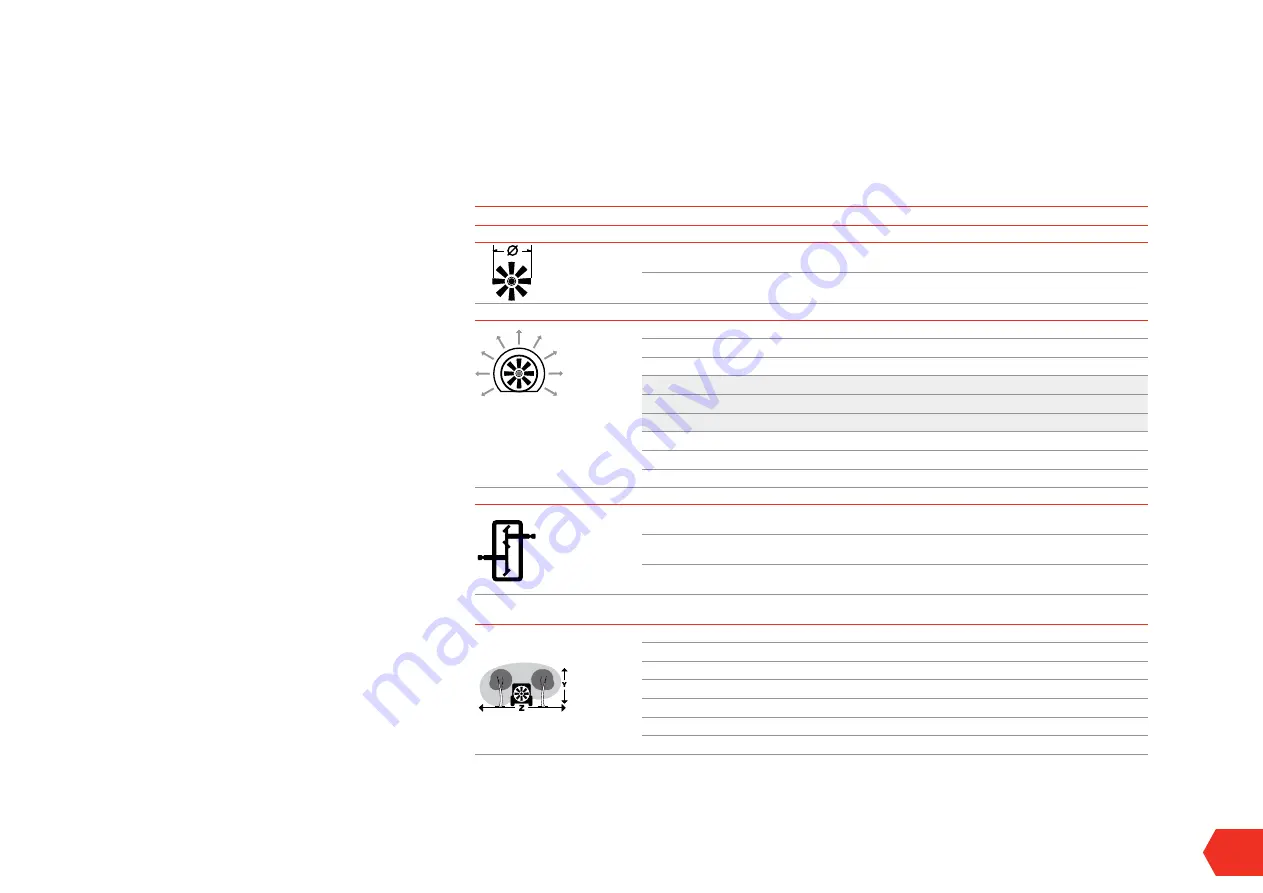
17
SECTION 4
PRODUCT FEATURES / FAMILIARISATION
FIENI FANS
The attached table lists the performance details for each
Cropliner Fieni fan model.
The DSV fan was designed for low noise and lower power
absorption, while still guaranteeing a large air volume.
The 9 blades of the DSV fan are made of a composite
material and have been specifically designed to
guarantee high performance.
Rear intake fans run anticlockwise.
The fan blades can be set at three different pitch angles
to adapt the Fieni sprayer unit to the power of the tractor
available. All Cropliner sprayers are tested and supplied
with the fan set to the
middle blade pitch setting
.
The fans are equipped with a centrifugal clutch made of
metal with brake lining.
Each fan is PTO shaft driven via a 2 speed (plus neutral),
low maintenance, heavy duty gearbox.
Designed for maximum PTO speed = 540 rpm.
Each fan has a series of small independent moveable
flat blades fitted on the air outlet, to help direct the air to
where it is required.
Each side of the fan is a stainless steel “spray ring” with
13, 14 or 15 nozzles per side. Each nozzle is of the brass
“roll-over” type.
920 LINEAR
TOWER (LT) FAN
920 DSV FAN
1060 DSV FAN
ORDER CODE
KH-5037
KH-5035
KH-5040
9-BLADE FAN
Fan blade diameter mm
913
913
1,060
Standard RPM (PTO 540)
(High)
1,780
1,780
1,780
OUTPUT AND POWER
Pitch
26°
26°
64°
M3/HR
73,682
73,682
84,696
HP
26.4
26.4
35.38
Pitch
34°
34°
72°
m3/hr
81,285
81,285
99,929
HP
36.9
36.9
50.08
Pitch
42°
42°
80°
M3/HR
83,798
83,798
108,618
HP
47.5
47.5
70.23
FAN GEARBOX MODEL
CM-12VNS
CM-12VNS
CM-15
2-speed plus neutral
2 + N
2 + N
2 + N
Low box ratio
1:2:93
1:2.93
1:2.93
High box
1:3.29
1:3.29
1:3.3
PERFORMANCE*
(*in ideal conditions)
Y = metres
6
8
10
Z = metres
15
14
16
Suitable tank size
1500 - 4000
1500 - 4000
3000 - 5000
Recommended tractor HP
≥
65
≥
70
≥
105
Nozzles per side
13 + 13 (26)
14 + 14 (28)
15 + 15 (30)
Noise rating (dB) @ 7.5m
92
92
96
Fan weight
178
130
188
The maximum canopy height and width figures are entirely subject to the canopy density, size, shape and weather conditions.
Summary of Contents for Cropliner 1500XL
Page 125: ...125...