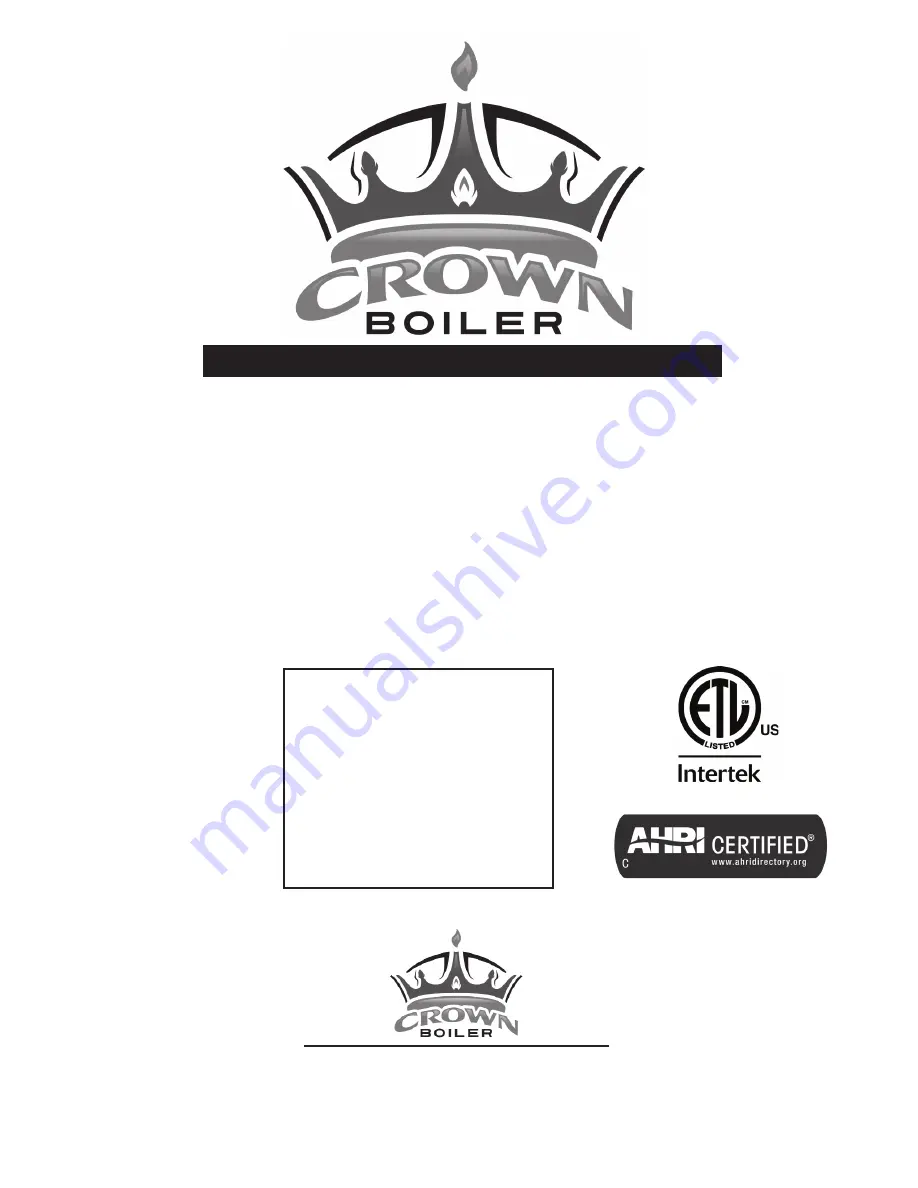
1
Series 16H
Gas-Fired Natural Draft Hot Water Boilers
INSTALLATION INSTRUCTIONS
These instructions must be affixed on or adjacent to the boiler
Models:
•
16H-340
•
16H-410
•
16H-460
•
16H-505
WARNING
: Improper installation,
adjustment, alteration, service or
maintenance can cause property
damage, injury, or loss of life.
For assistance or additional
information, consult a qualified
installer, service agency or
the gas supplier. Read these
instructions carefully before
installing.
D
E S I G N E D T O
L
E A D
Manufacturer of Hydronic Heating Products
P.O. Box 14818 3633 I. Street
Philadelphia, PA 19134
www.crownboiler.com
3050579
Summary of Contents for 16H-340
Page 13: ...13 Figure 8 Jacket Assembly ...
Page 14: ...14 Figure 9 EP CSD 1 Control Installation ...
Page 16: ...16 Figure 11 Main Gas Piping Intermittent Ignition EI ...
Page 17: ...17 Figure 12 Schematic Pilot Piping Honeywell EI USA ...
Page 18: ...18 Figure 15 Schematic Gas Piping EP CSD 1 Control System 16H 410 16H 505 ...
Page 37: ...37 Figure 41 Operating Instructions EI ...
Page 47: ...47 Honeywell EI Trouble Shooting Guide ...
Page 48: ...48 THIS PAGE LEFT BLANK INTENTIONALLY ...
Page 58: ...58 ...
Page 60: ...60 ...