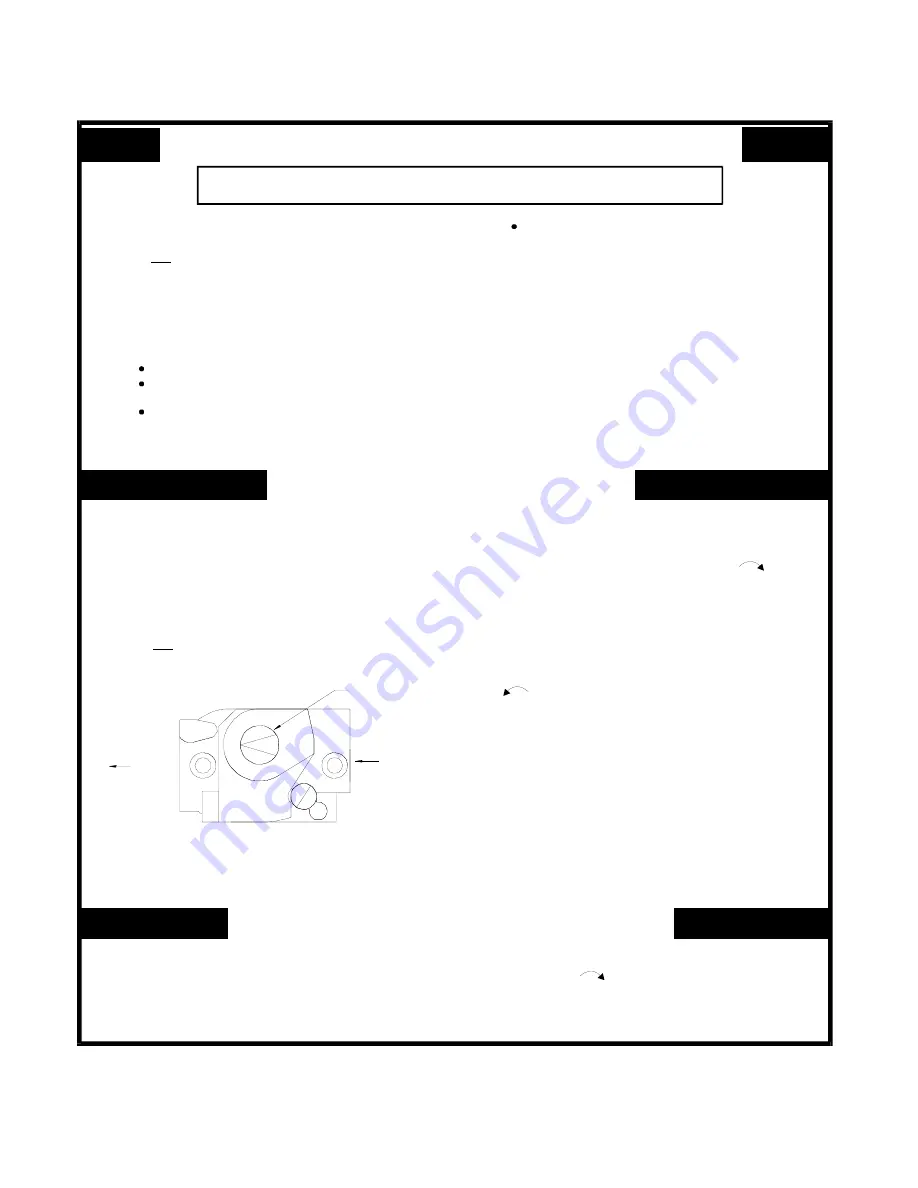
37
A. This appliance is equipped with an ignition
device which automatically lights the pilot.
Do
try to light the pilot by hand.
B. BEFORE LIGHTING smell all around the
appliance area for gas. Be sure to smell next
to the floor because some gas is heavier than
air and will settle on the floor.
WHAT TO DO IF YOU SMELL GAS
Do not try to light any appliance.
Do not touch any electric switch; do not
use any phone in your building.
Immediately call your gas supplier from
a neighbor’s phone. Follow the gas
supplier’s instructions.
not
If you cannot reach your gas supplier, call
the fire department.
C. Use only your hand to push in or turn the gas
control knob. Never use tools. If the knob will
not push in or turn by hand, don’t try to repair it,
call a qualified service technician. Force or
attempted repair may result in a fire or explosion.
D. Do not use this appliance if any part has been
under water. Immediately call a qualified service
technician to inspect the appliance and to
replace any part of the control system and any
gas control which has been under water.
OPERATING INSTRUCTIONS
1. STOP! Read the safety information above on
this label.
2. Set the thermostat to lowest setting.
3. Turn off all electric power to the appliance.
4. This appliance is equipped with an ignition
device which automatically lights the pilot.
Do
try to light the pilot by hand.
not
5. Remove front access panel.
6. Rotate the gas control knob clockwise to OFF.
7. Wait five (5) minutes to clear out any gas. Then
smell for gas, including near the floor. If you then
smell gas, STOP! Follow “B” in the safety inform-
ation above on this label. If you don’t smell gas
go to the next step.
8. Rotate the gas control knob counter clockwise
to “ON”.
9. Replace front access panel.
10. Turn on all electric power to the appliance.
11. Set thermostat to desired setting.
12. If the appliance will not operate, follow the
instructions “To Turn Off Gas To Appliance” and
call your service technician or gas supplier.
1. Set the thermostat to lowest setting.
2. Turn off all electric power to the appliance if
service is to be performed.
3. Push in gas control knob slightly and turn
clockwise to “OFF”. Do not Force.
WARNING: If you do not follow these instructions exactly, a fire or explosion
may result causing property damage, personal injury or loss of life.
TO TURN OFF GAS TO APPLIANCE
FOR YOUR SAFETY READ BEFORE LIGHTING
GAS OUTLET
GAS CONTROL KNOB
(SHOWN IN “ON” POSITION)
GAS INLET
GAS VALVE - TOP VIEW
Summary of Contents for BWF061
Page 8: ...7 ...
Page 9: ...8 ...
Page 14: ...13 ...
Page 31: ...30 ...
Page 34: ...33 ...
Page 36: ...35 ...
Page 40: ...39 FIGURE 38 PILOT BURNER FLAME ...
Page 49: ...48 ...
Page 51: ...50 1 Burner Components 50mm Burner Components ...
Page 53: ...52 ...