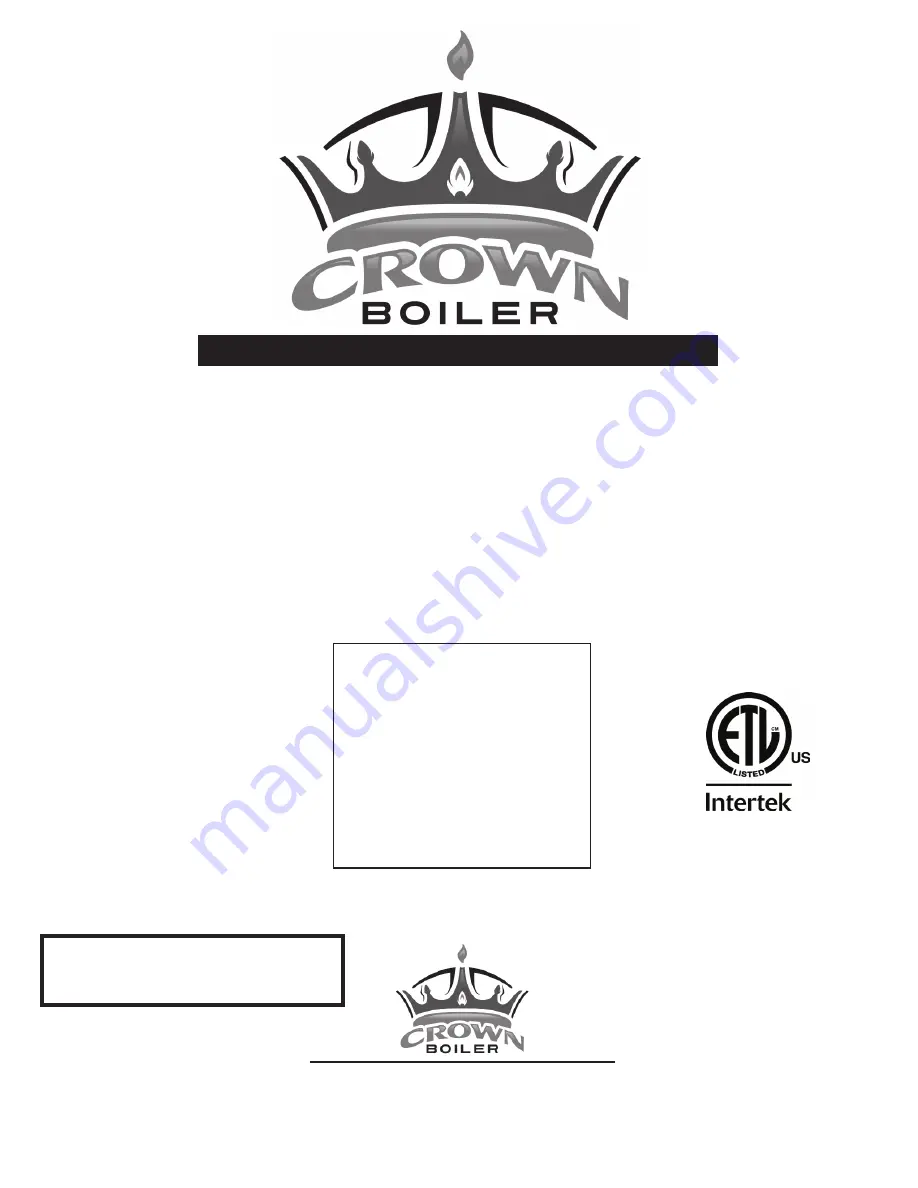
WARNING
: Improper installation,
adjustment, alteration, service or
maintenance can cause property
damage, injury, or loss of life. For
assistance or additional information,
consult a qualified installer, service
agency or the gas supplier. Read
these instructions carefully before
installing.
Models:
•
CWD060
•
CWD083
•
CWD110
•
CWD138
•
CWD165
•
CWD193
•
CWD220
•
CWD245
CWD Series
Gas-Fired Direct Vent Hot Water Boilers
INSTALLATION INSTRUCTIONS
These instructions must be affixed on or adjacent to the boiler
D
E S I G N E D T O
L
E A D
Manufacturer of Hydronic Heating Products
P.O. Box 14818 3633 I. Street
Philadelphia, PA 19134
www.crownboiler.com
Equipped with Honeywell
S9361A Control System
9902339
Summary of Contents for CWD060
Page 2: ...2 2...
Page 13: ...11 11 FIGURE 5 5 ALLAIR FROM OUTSIDE USING HORIZONTAL DUCTS INTO BOILER ROOM...
Page 41: ...39 39 FIGURE 8 1 BASIC PIPING FIGURE 8 2 INDIRECT WATER HEATER BOILER SIDE PIPING...
Page 42: ...40 40 FIGURE 8 3 BYPASS PIPING FIGURE 8 4 ISOLATION OF BOILER FROM SYSTEM WITH HEAT EXCHANGER...
Page 43: ...41 41 FIGURE 8 5 CHILLER PIPING...
Page 46: ...44 44 FIGURE 9 2 INTERNAL CONNECTIONS DIAGRAM...
Page 47: ...45 45 FIGURE 9 3 LADDER DIAGRAM...
Page 51: ...49 49 FIGURE 10 3 GAS VALVE FIGURE 10 4 MEASURING MANIFOLD PRESSURE...
Page 64: ...62 62 FIGURE 12 2b MEASURING PRESSURE ACROSS PRESSURE SWITCH...
Page 68: ...66 66 Notes...
Page 71: ...69 69...
Page 73: ...71 71...
Page 75: ...73 73...
Page 77: ...75 75...
Page 79: ...Notes...