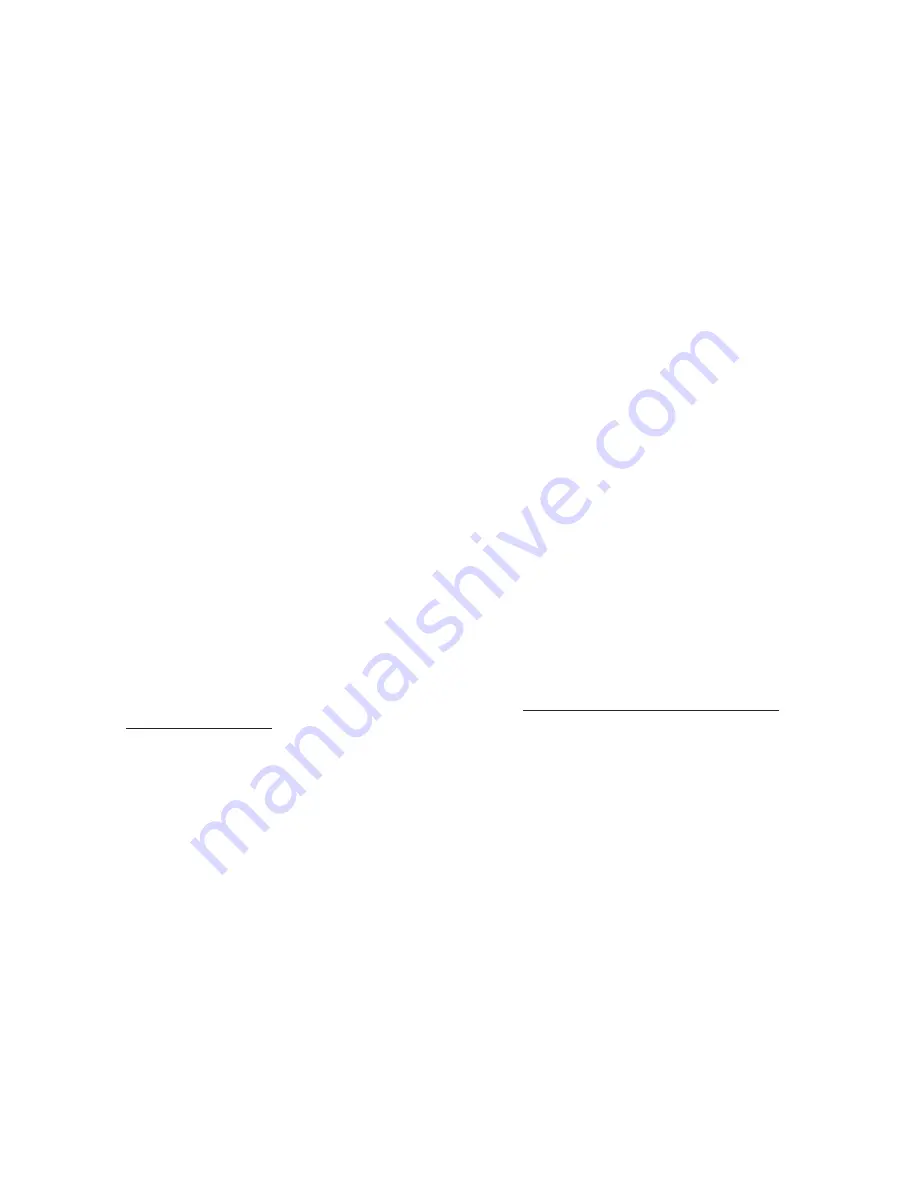
52
side panel installed in the previous step and secure with three #10 sheet metal screws.
5) Install the left side panel in the same manner as the right side.
6) Attach the front corners of the diverter panel to the side jacket panels using #10 sheet metal screws.
7) Install the horizontal (angle) jacket clips in the front edge of the side jacket panels. Slide this clip through the
rectangular slot that is about halfway up the front edge of the side jacket panels and secure with the 8-32 self
tapping screws provided.
8) Slip the Vertical Jacket Clip through the rectangular slot that is near the bottom of the front edge of the side jacket
panels. Secure with the 8-32 sheet metal screws provided.
9) Install the top jacket panel. Use #10 sheet metal screws to attach it to the rear jacket panel and the top-front corners
of the side panels.
10) Install the upper-front jacket panel. Insert the flange on the top of this panel under the top panel. Run two #10 sheet
metal screws into the horizontal jacket clips through the holes in the bottom of this panel.
11) Attach the door knobs to the Lower-Front Panel using 8-32 x 1/2 machine screws.
12) The labels have been applied at the factory. Verify the location of the labels according to the list below:
a) Clearance Label - Located on the top jacket panel.
b) Lighting Instructions - Located on the lower left corner of the right side panel next to the gas manifold
c) Lowest Permissible Water Level Plate - Located next to the bottom water gauge tapping.
d) Blow Down Card - Located just above the "Lowest Permissible" Water Level Plate
e) Wiring Diagram - Located on the inside of the removable door
f)
"CROWN" Nameplate - Located on the top center of the outside of the removable door
g) Rating Plate - Located on the upper left of the right side panel
D. Gas Valve Installation
1) The gas valve assembly has been pre-piped with one half of a piping union and is to be connected to the other half
of the union located on the gas manifold.
2) Connect the pilot tubing from the pilot burner to the gas valve pilot tapping.
3) Connect the thermocouple lead to the gas valve (standing pilot boilers only).
E. Control and Trim Installation
(Refer to Figure A3 for Tapping Locations)
1) Install the tankless heater or blank cover plate on the opening on the right side of the heat exchanger using the
gasket and 3/8 bolts provided.
2) Install the high limit well in the tapping in the tankless heater or cover plate.
3) Mount the limit control (L8148E or L8124E) onto the control well. Be sure that the temperature sensing bulb is
bottomed out in the well. Tighten the screw on the bottom of the control so that it is securely clamped onto the well.
4) Install a 1/2 x 1/4 bushing and the tridicator gauge into tapping “C”. Tighten with wrench applied to the square
shank on the back of the gauge. Do not apply pressure on the gauge case since this may ruin the calibration of the
gauge.
5) Install relief valve (spindle must be in vertical position) into tapping “H” on the boiler left side (See Figure 1 in the
installation manual) using the ¾” NPT nipples and elbow supplied. Pipe the discharge of the safety relief valve to a
location where water or steam will not create a hazard or cause property damage if the valve opens. The end of the
discharge pipe must terminate in an unthreaded pipe. The safety valve discharge piping must be in an area where it
is not likely to become plugged by debris or subjected to freezing.
6) Install the 1-1/2 return piping and circulator in tapping “D”. See Section VIII System Piping in the installation
manual for instructions on completing the piping of this boiler.
51
Summary of Contents for CWI Series
Page 15: ...15 14 FIGURE12 INDIRECTWATERHEATER BOILERSIDEPIPING FIGURE11 STANDARDBOILERPIPING...
Page 17: ...17 FIGURE15 BOILERPIPINGWITHCHILLER FIGURE14 ISOLATIONOFBOILERFROMSYSTEMWITHAHEATEXCHANGER 16...
Page 45: ...45 44...
Page 47: ...47 46...
Page 49: ...49 48...
Page 51: ...51 50 FIGUREA1 BASE HEATEXCHANGER FLUE COLLECTORASSEMBLY...
Page 53: ...53 52 FIGUREA2 JACKETINSTALLATION...
Page 55: ...55 54 FIGUREA3 TAPPING LOCATIONS SEE TEXT FOR TAPPING USES...