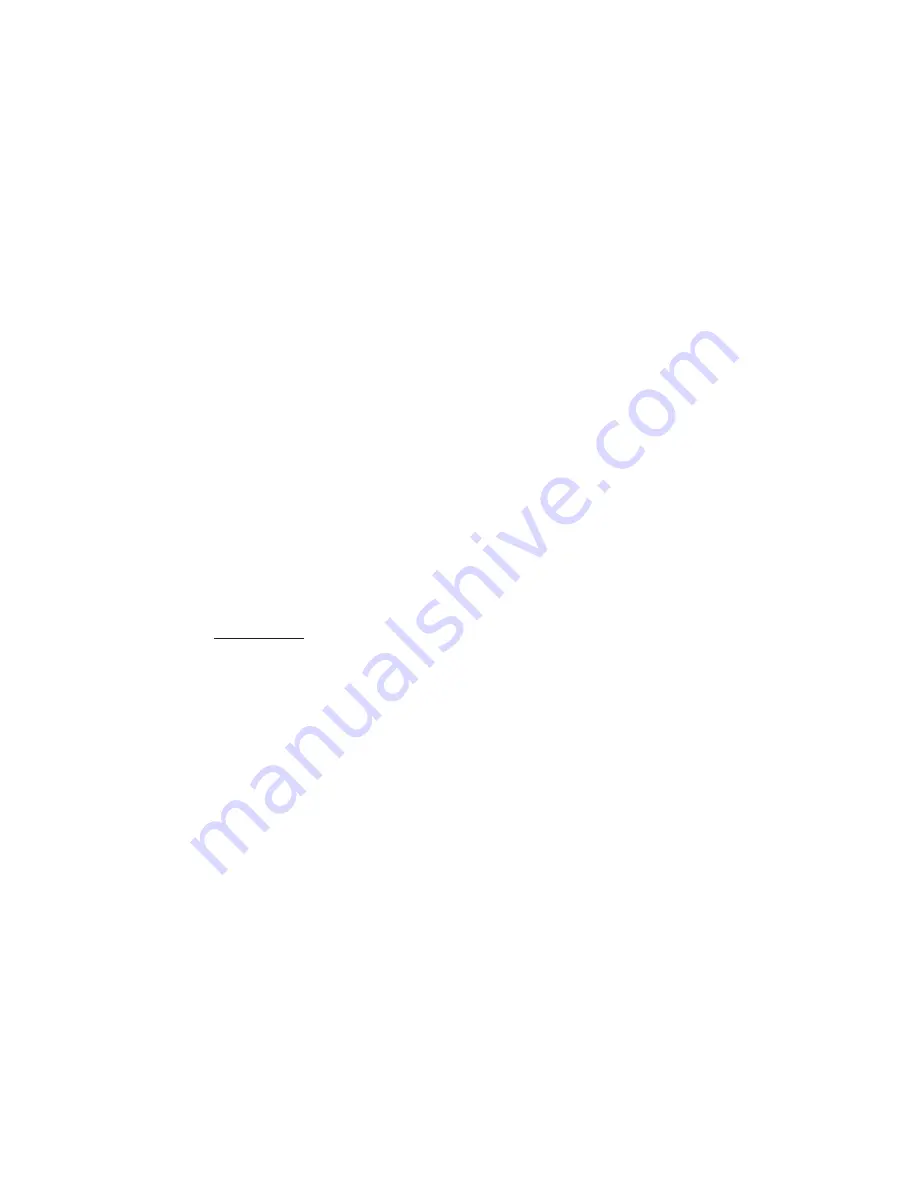
99
•
The “free area” of an opening takes into account the blocking effect of mesh, grills, and louvers. Where screens are
used, they must be no finer than ¼” (4 x 4) mesh.
VI Venting
Vent installation must be in accordance with local building codes, or the local authority having jurisdiction, or the
National
Fuel Gas Code
, NFPA 54/ANSI Z 223.1.
A typical vent installation is illustrated by Figure 8. The components of vent installation are the vent damper, vent connector
and chimney.
1) Acceptable Chimneys - The following chimneys may be used to vent CWI series boilers:
•
Listed Type B or L gas vent - Install in accordance with the manufacturer’s instructions, the terms of its listing, and
applicable codes.
•
Masonry Chimney - The masonry chimney must be constructed in accordance with the
Standard for Chimneys,
Fireplaces, Vents, and Solid Fuel Burning Appliances
(NFPA 211) and lined with a clay liner or other listed lining
system. Do not vent a CWI series boiler into an unlined chimney.
2) Acceptable Vent Connectors - The following may be used for vent connectors:
•
Listed type B or L Gas Vent
•
Single Wall Galvanized Pipe - Use 0.018” (26 gauge or heavier). The size and location of the chimney may not
permit the use of a single wall connector in some cases. See the
National Fuel Gas Code
. Do not use single wall
pipe for vent connectors in attics.
•
Other Vent Connectors Permitted by the
National Fuel Gas Code
.
3) Chimney and Vent Connector Sizing - Size the chimney and vent connector in accordance with the
National Fuel Gas
Code.
4) Exterior Chimneys - An exterior chimney has one or more sides exposed to the outdoors below the roof line. There are
two conditions under which an exterior chimney may be used:
•
In some very restrictive
cases, CWI series boilers may be vented into an exterior ceramic lined masonry chimney.
See the
National Fuel Gas Code
for information on when exterior chimneys may be used.
•
An exterior masonry chimney may be used if it is lined with B vent or a listed chimney lining system.
5) This boiler may be vented using a listed power venter. The power venter must be in sized and installed in accordance
with the power venter manufacturer’s instructions, the terms of the power venter listing, and applicable codes. The boiler
must be electrically interlocked with the power venter to prevent boiler operation if the power venter fails to operate. Before
deciding to use a power venter, make certain that the flue gas exiting the power venter will not damage adjacent construction
or other structures. Also make certain that the power venter terminal will not be subjected to winds which could effect power
venter operation.
6) Do not connect the vent of this appliance into any portion of a mechanical vent system operating under positive pressure.
7) Do not connect the boiler into a chimney flue serving an open fireplace or other solid fuel appliance.
8) Prior to boiler installation, inspect chimney for obstructions or other defects and correct as required. Clean chimney as
necessary.
9) Vent pipe should slope upward from draft diverter not less than one inch in four feet. No portion of vent pipe should run
downward or have sags. Vent pipe must be securely supported.
10) The vertical section of vent pipe coming off the boiler should be as tall as possible, while still maintaining the proper
clearance from the horizontal vent connector to combustibles and the proper pitch called for in (9) above.
11) Vent pipe should be installed above the bottom of the chimney to prevent blockage.
12) Vent pipe must be inserted flush with inside face of the chimney liner and the space between vent pipe and chimney
sealed tight.
13) Do not install the vent damper in any portion of the vent system which is used by appliances other than the boiler being
installed.
Summary of Contents for CWI103
Page 2: ......
Page 17: ...15 15 FIGURE 12 INDIRECT WATER HEATER BOILER SIDE PIPING FIGURE 11 STANDARD BOILER PIPING ...
Page 34: ...32 32 Notes ...
Page 41: ...39 39 Notes ...
Page 43: ...41 41 ...
Page 45: ...43 43 ...
Page 47: ...45 45 ...
Page 49: ...47 47 FIGURE A1 BASE HEAT EXCHANGER FLUE COLLECTOR ASSEMBLY ...
Page 51: ...49 49 FIGURE A2 JACKET INSTALLATION ...
Page 53: ...51 51 FIGURE A3 TAPPING LOCATIONS SEE TEXT FOR TAPPING USES ...
Page 54: ...52 52 Notes ...
Page 55: ...53 53 Notes ...