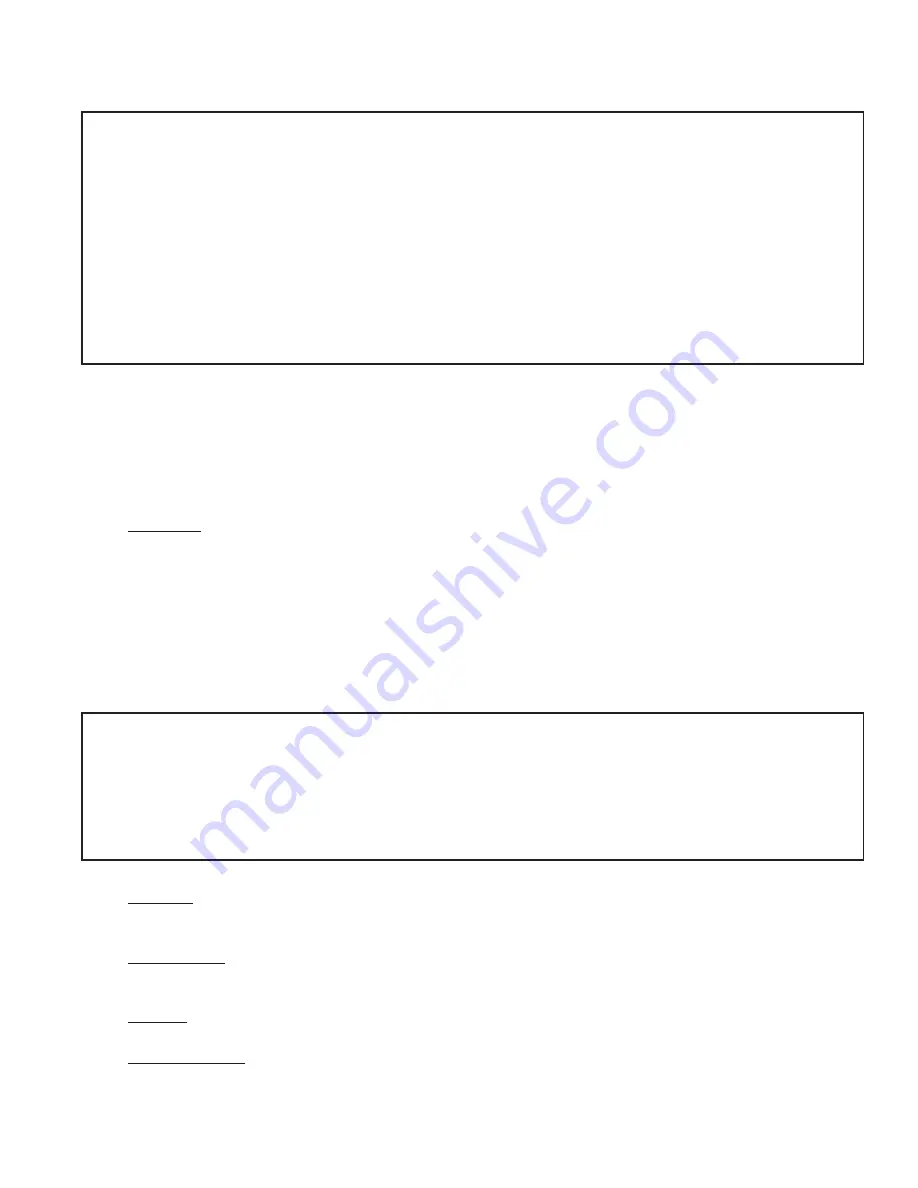
13
13
VIII System Piping
Standard Piping
Figure 11 shows typical boiler system connections on a single zone system. Additional information on hydronic system
design may be found in
Installation of Residential Hydronic Systems
(Pub. #200) published by the Hydronics Institute in
Berkeley Heights, NJ. The components in this system and their purposes are as follows:
1) Relief valve (Required) - Mount the relief valve on the right side of the boiler as shown in Figure 1 using the 3/4 nipples
and elbow provided. The relief valve shipped with the boiler is set to open at 30 psi. This valve may be replaced with one
having a pressure up to the “MAWP, WATER” shown on the rating plate. If the valve is replaced, the replacement must
have a relief capacity in excess of the DOE heating capacity for the boiler.
Pipe the discharge of the relief valve to a location where water or steam will not create a hazard or cause property damage
if the valve opens. The end of the discharge pipe must terminate in an unthreaded pipe. If the relief valve discharge is
not piped to a drain it must terminate at least 6 inches above the floor. Do not run relief valve discharge piping through an
area that is prone to freezing. The termination of the relief valve discharge piping must be in an area where it is not likely
to become plugged by debris.
2) Circulator (Required) - Although the circulator is shipped on the boiler return, it can be installed on the boiler supply. If
the circulator is moved to the supply, it should be positioned just downstream of the expansion tank as shown in Figure
11.
3) Expansion Tank (Required) - If this boiler is replacing an existing boiler with no other changes in the system, the
old expansion tank can generally be reused. If the expansion tank must be replaced, consult the expansion tank
manufacturer’s literature for proper sizing.
4) Fill Valve (Required) - Either a manual or automatic fill valve may be used. The ideal location for the fill is at the
expansion tank.
5) Automatic Air Vent (Required) - At least one automatic air vent is required. Manual vents will usually be required in
other parts of the system to remove air during initial fill.
CAUTION
• INSTALL BOILER SO THAT THE GAS IGNITION SYSTEM COMPONENTS ARE PROTECTED
FROM WATER (DRIPPING, SPRAYING, RAIN, ETC.) DURING APPLIANCE OPERATION AND
SERVICE (CIRCULATOR REPLACEMENT, ETC.).
• OPERATION OF THIS BOILER WITH CONTINUOUS RETURN TEMPERATURES BELOW 120°F
CAN CAUSE SEVERE HEAT EXCHANGER CORROSION DAMAGE.
• OPERATION OF THIS BOILER IN A SYSTEM HAVING SIGNIFICANT AMOUNTS OF DISSOLVED
OXYGEN CAN CAUSE SEVERE HEAT EXCHANGER CORROSION DAMAGE.
• DO NOT USE TOXIC ADDITIVES, SUCH AS AUTOMOTIVE ANTIFREEZE, IN A HYDRONIC
SYSTEM.
DANGER
• PIPE RELIEF VALVE DISCHARGE TO A SAFE LOCATION.
• DO NOT INSTALL A VALVE IN THE RELIEF VALVE DISCHARGE LINE.
• DO NOT MOVE RELIEF VALVE FROM FACTORY LOCATION.
• DO NOT PLUG RELIEF VALVE DISCHARGE.
Summary of Contents for CWI103
Page 2: ......
Page 17: ...15 15 FIGURE 12 INDIRECT WATER HEATER BOILER SIDE PIPING FIGURE 11 STANDARD BOILER PIPING ...
Page 34: ...32 32 Notes ...
Page 41: ...39 39 Notes ...
Page 43: ...41 41 ...
Page 45: ...43 43 ...
Page 47: ...45 45 ...
Page 49: ...47 47 FIGURE A1 BASE HEAT EXCHANGER FLUE COLLECTOR ASSEMBLY ...
Page 51: ...49 49 FIGURE A2 JACKET INSTALLATION ...
Page 53: ...51 51 FIGURE A3 TAPPING LOCATIONS SEE TEXT FOR TAPPING USES ...
Page 54: ...52 52 Notes ...
Page 55: ...53 53 Notes ...