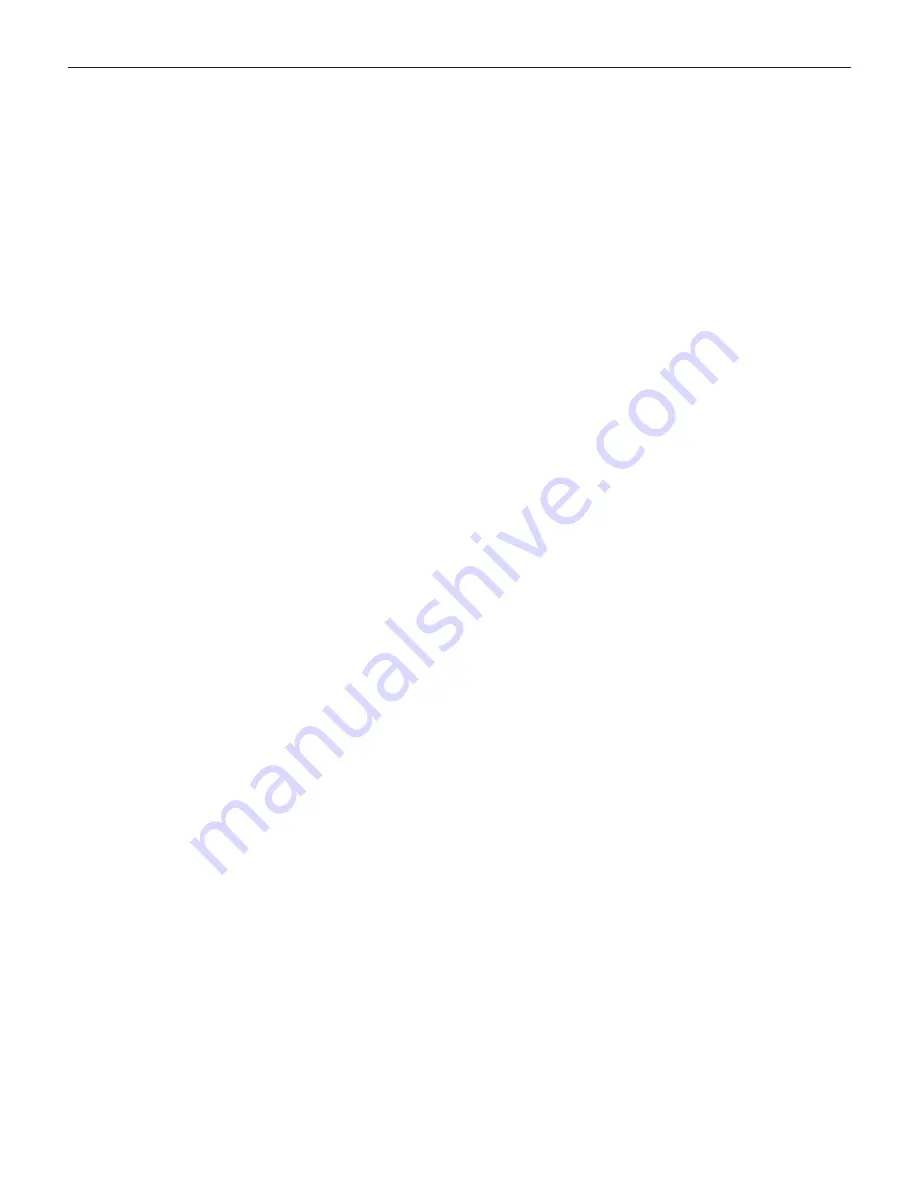
7
❖
English
L-2028 Installation
removes debris from the air prior to the air being drawn
across the evaporator coil and fins. Dust and lint can clog and
reduce airflow across the evaporator coil resulting in poor
performance. See the “
Maintenance” section for filter cleaning
instructions.
Ducting
Good airflow is critical for the performance of the entire
system. It is highly dependent on the quality of the ducting
installation. The ducting should be run as straight, smooth and
taut as possible minimizing the number of 90 degree bends
(two tight 90 degree bends can reduce airflow by 25 percent).
The following is a summary of proper ducting connections:
1. Pull back the fiberglass insulation exposing the inner
mylar duct hose.
2. Slide the mylar duct hose around the mount ring until it
bottoms out.
3. Screw 3 or 4 stainless steel sheet metal screws through
the duct hose into the transition ring. Make sure to catch
the wire in the duct hose with the heads of the screws. Do
not use band clamps, as the hose will slide off.
4. Wrap duct tape around the ducting and ring joint to
prevent any air leaks.
5. Pull the insulation back up over the mylar to the ring and
tape this joint.
6. Remove excess ducting and use the same connection
method at the supply air grill.
Manual Control Panel Installation
The manual control panel should be located within cap tube
length of the air conditioning unit. The dimensions for the
2-knob panel is 3¼" (83mm) x 5½" (140mm). The cut out size
for the 2-knob panel is 2½" (64mm) wide by 4¾" (121mm) tall.
The 3-knob panel is configured either vertically or horizontally.
Dimensions for the 3-knob is 2
15
/
16
" (75mm) x 7
15
/
16
" (202mm).
The cut out size for the 3-knob panel is 2" (51mm) by
6¾"(171mm). (Refer to Figures 6 and 7 at the back of this
manual.) Once the cut out is made, carefully uncoil the copper
cap tube with return air sensor (copper bulb) and route the
control wires and cap tube through the hole and back to the
unit
using caution not to kink the cap tube.
Mount the
return air sensor into the clips provided on the evaporator coil.
If the return air sensor cannot be mounted on the evaporator
coil, mount it behind the return air grill. The sensor must be
mounted in the return air stream. Make electrical connections
according to the wiring diagrams provided. (See wiring
diagrams, Figures 8, 9, 10 and 11 at the back of this manual.)
Electrical Connections, Grounding & Bonding
for AC Powered Zephyr
All Zephyr units have a five position terminal strip mounted
inside the electric box. The terminal strip is labeled for proper
connections of the electrical supply, ground wires and pump
circuits. Wiring diagrams are provided in the electrical box and
in this manual. The correct size circuit breaker should be used
to protect the system as specified on the air conditioning unit’s
data plate label. A minimum of 12 AWG boat cable should be
used to supply power to the air conditioning unit and to the
seawater pump (see next paragraph). All connections to the
terminal strip shall be made with ring terminals supplied with
the Zephyr kit.
Turn off AC (alternating current) power
supply circuit breaker before opening electrical box and
accessing the terminal strip.
Each air conditioning unit installed requires its own dedicated
circuit breaker. If there is only one air conditioning unit
installed, the seawater pump does not require a circuit
breaker; the wiring from the seawater pump is connected to
the terminal strip on the unit. (See wiring diagrams, Figures 8,
9 and 10 at the back of this manual.) A minimum of 12 AWG
boat cable should be used to extend the wires on the pump, if
necessary, using the butt slices included with the kit. If two or
more air conditioning units use the same seawater pump, the
pump wires will be connected to a pump relay panel (PRP)
which in turn has its own dedicated circuit breaker (see the
wiring diagram furnished with the PRP). Any electrical
connections in the bilge below the waterline should use heat
shrink type butt splices.
The air conditioning unit must be connected to the boat’s
bonding system to prevent corrosion due to stray electrical
current. All pumps, metallic valves and fittings in the seawater
circuit that are isolated from the air conditioning unit by PVC
or rubber hoses must be individually bonded to the boat’s
bonding system also. This will help eliminate any possibility of
corrosion due to stray current.
Note: Failure to properly ground and bond the
system will void the warranty!
Electrical Connections, Grounding & Bonding
for DC Powered Cuddy dc
All Cuddy dc units are connected by polarized plugs to the
Dedicated Power Module DPM, pump, and control (available
separately or in kit). These plugs are configured unique to
each component. Wiring diagrams and schematics are
provided in this manual (see Figure 11 at the back of this
manual). A 60 amp circuit breaker or fuse should be installed
at the positive side of the battery to protect the wires. Any
electrical connections in the bilge below the waterline should
be heat shrink type.
Turn off DC power supply circuit breaker before making
connections.
The air conditioning unit and its components must be con-
nected to the boat’s bonding system to prevent corrosion due
to stray electrical current. There is a bonding ground stud on
the Dedicated Power Module. This stud must be connected to
the vessel’s bonding stud, which is typically on the engine
Summary of Contents for Cuddy dc
Page 2: ......
Page 22: ...22 English L 2028 Fig 8 Wiring Diagram of ZF3 5 ...
Page 24: ...24 English L 2028 Fig 11 Wiring Diagram for Cuddy dc CD3 5HV 12VDC ...
Page 34: ......
Page 35: ......