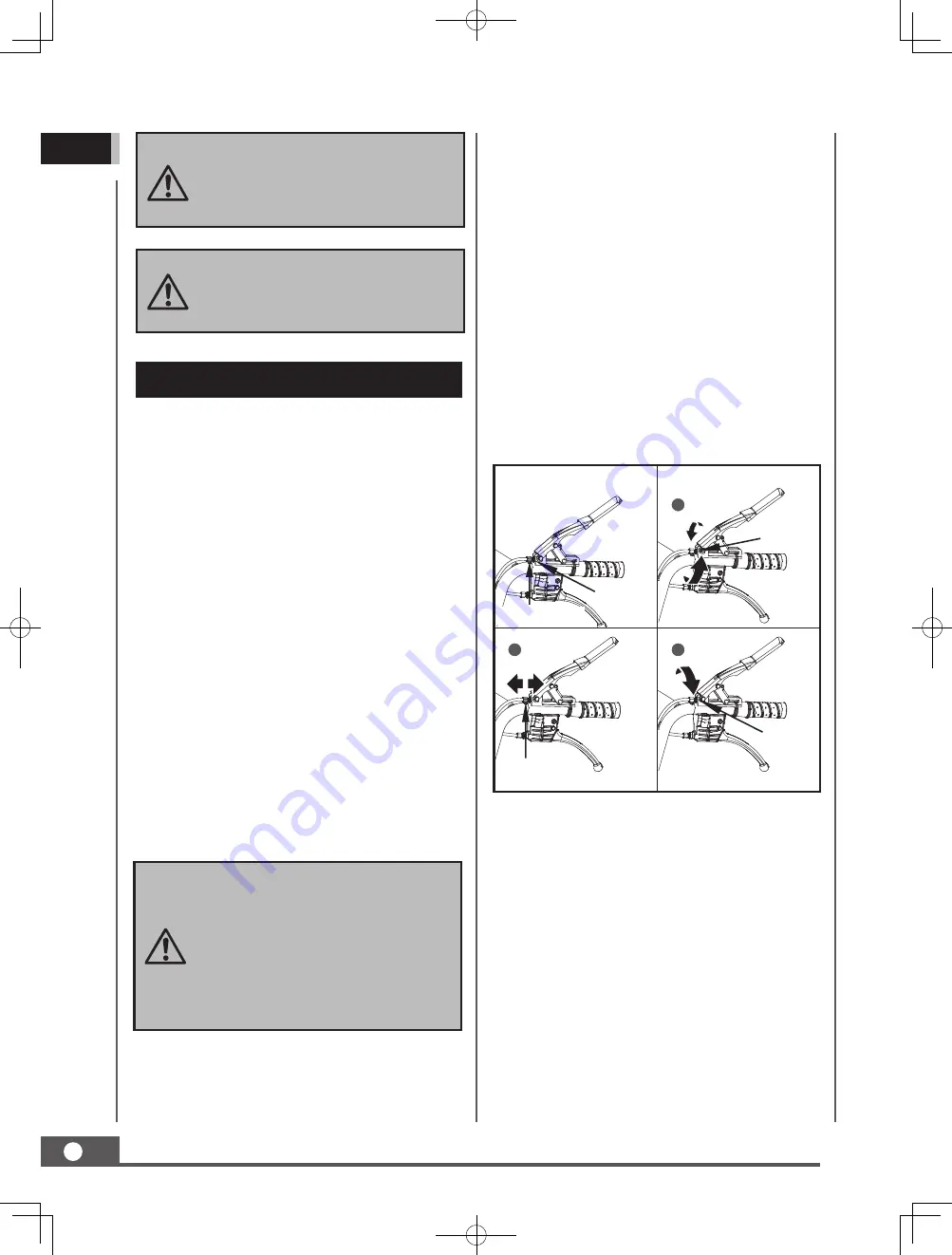
MINI TRACKED DUMPER
16
GB
MAINTENANCE
Never use a “pressure washer” to
clean your unit. Water can penetrate
tight areas of the machine and its
transmission case and cause damage
to spindles, gears, bearings, or the
engine. The use of pressure washers
will result in shortened life and
reduce serviceability.
S u d d e n s t o p p i n g a t a h i g h
speed under a heavy load is not
recommended. Engine damage may
result.
Do not move the choke control to
CLOSE to stop the engine. Backfire
or engine damage may occur.
1.
1.
1.
2.
2.
3.
3.
4.
5.
Adjusting Clutch
When the clutch begins to show wear, the
handle reach will become wider, making it
more difficult to reach. Follow these steps
to return the clutch lever back to its original
position.
Maintaining your mini tracked dumper will
ensure long life to the machine and its
components.
Preventive Maintenance
Jam Nut
Adjustment Nut
Adjustment Nut
Jam Nut
Jam Nut
1
2
3
Adjusting Steering
If steering becomes difficult to engage follow
these steps to adjust the cable tension.
Turn off the engine and disengage all
command levers. The engine must be cool.
Keep the engine’s throttle lever in its SLOW
position and remove the spark plug wire
from the spark plug and secure.
Inspect the general condition of the power
trackbarrow. Check for loose screws,
misalignment or binding of moving parts,
cracked or broken parts, and any other
condition that may affect its safe operation.
Use a soft brush, vacuum or compressed
air to remove all contaminants from the
machine. Then use high quality light oil to
lubricate all moving parts.
Check the spark plug wire regularly for
signs of wear, and replace when needed.
Loosen the jam nut by turning it counter
clockwise with 10mm wrench.
Tighten or loosen the cable by turning the
cable adjustment nut clockwise or counter
clockwise with 10mm wrench until you
have reached your required tightness.
Once tightness is set, return the jam nut
against the handle to hold the cable in
place.
Loosen the jam nut by turning it counter
clockwise with 10mm wrench.
2.
3.
Tighten or loosen the cable by turning the
cable adjustment nut clockwise or counter
clockwise with 10mm wrench until you
have reached your required tightness.
Once tightness is set, return the jam nut
against the handle to hold the cable in place.