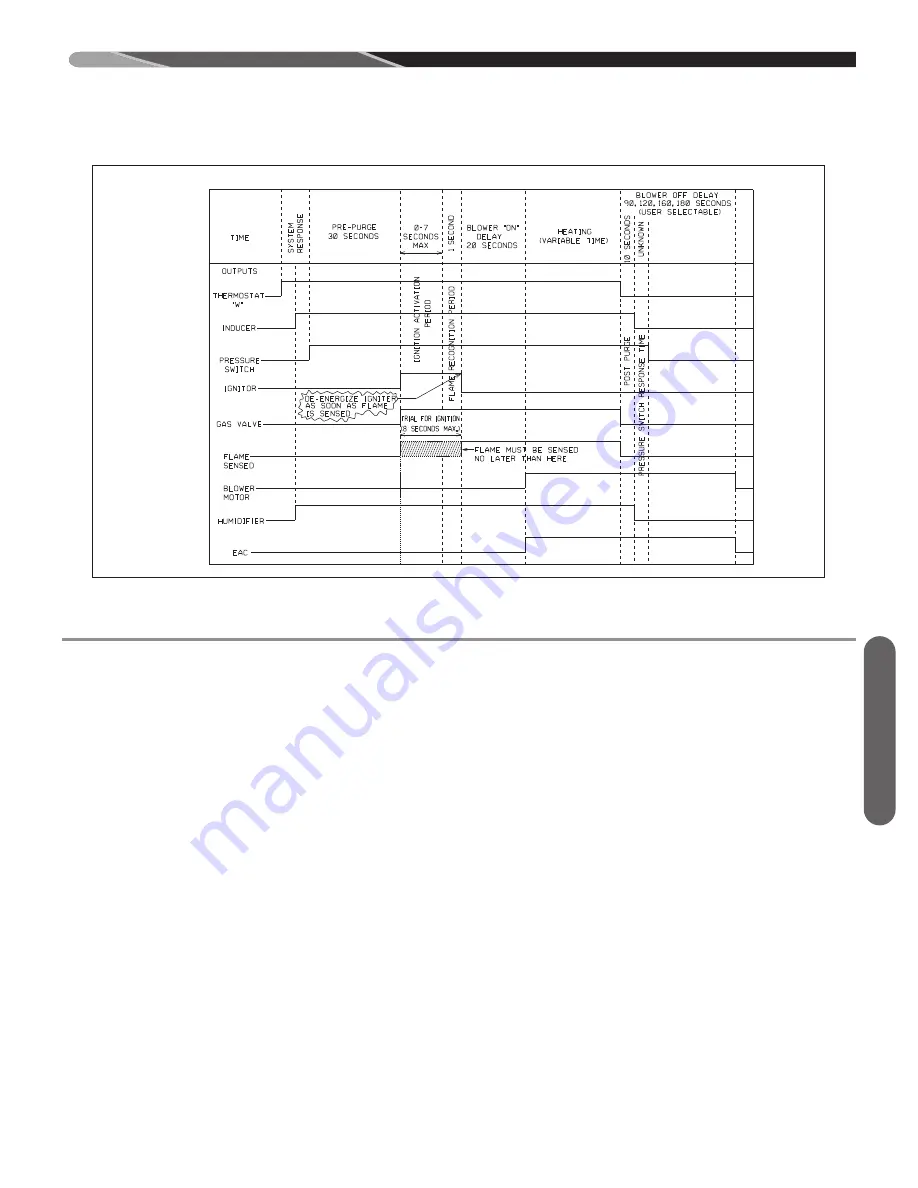
91
ADJUSTING OR CHECKING FURNACE INPUT
The maximum gas supply pressure to the furnace should
be 10.5" w.c. for natural gas and 13.0" w.c. for L.P. The
minimum gas supply pressure for purposes of input adjust-
ment to the furnace should be 5" w.c. for natural gas and
11.0" w.c. for L.P.
A calibrated manometer is required for accurate gas pres-
sure readings.
The manifold pressure should be set at 3.5" w.c. for natural
gas and 10.0" w.c. for L.P. Only small variations in the gas
flow should be made by means of the pressure regulator
adjustment. In no case should the final manifold pressure
vary more than plus or minus 0.3" w.c. from the above-
specified pressures. To adjust the pressure regulator, re-
move the regulator cap and turn the adjustment screw
clockwise to increase pressure or counterclockwise to de-
crease pressure. Then replace the regulator cap securely.
Any necessary major changes in the gas flow rate should
be made by changing the size of the burner orifices.
To change orifice spuds, shut off the manual gas valve and
remove the gas manifold. On LP gas furnaces, the LP gas
supply pressure must be set between 11" and 13" w.c. by
means of the tank or branch supply regulators. The fur-
nace manifold pressure should be set at 10" w.c. at the gas
control valve. For elevations up to 2,000 feet, rating plate
input ratings apply. For high altitudes (elevations over
2,000 ft.), see conversion kit index for derating and orifice
spud sizes.
Checking furnace input is important to prevent over firing
beyond its design-rated input. NEVER SET INPUT ABOVE
THAT SHOWN ON THE RATING PLATE. Use the follow-
ing table or formula to determine input rate. Start the fur-
nace and measure the time required to burn one cubic foot
of gas. Prior to checking the furnace input, make certain
that all other gas appliances are shut off, with the excep-
tion of pilot burners. Time the meter with only the furnace
in operation.
TABLE 17
TIMING DIAGRAM
ST-A1194-27-X0
OFF
OFF
OFF
OFF
OFF
OFF
OFF
OFF
OFF
OFF
OFF
OFF
OFF
OPEN
OFF
OFF
CLOSED
OPEN
ON
ON
ON
ON
ON
ON
OFF
ON
TIMING DIAGRAM, FIELD SELECTIONS &
ADJUSTMENTS
Field Selections
Summary of Contents for 92MSP SERIES
Page 34: ...34 Field Conversions ...
Page 35: ...35 Field Conversions ...
Page 36: ...36 Field Conversions ...
Page 37: ...37 Field Conversions ...
Page 38: ...Field Conversions 38 ...
Page 99: ...99 ...
Page 100: ...100 CM 0716 ...