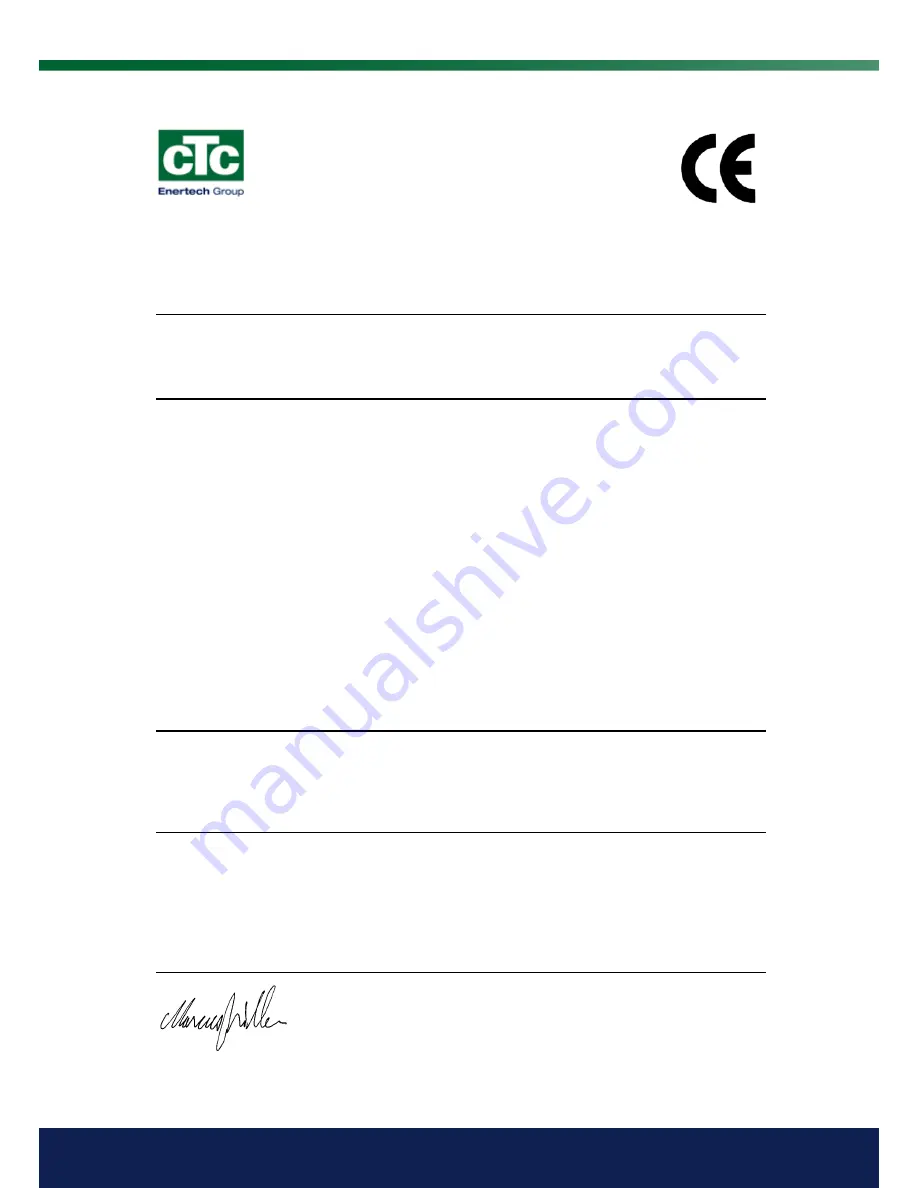
36
CTC EcoPart 400
General information
Declaration of conformity
Försäkran om överensstämmelse
Déclaration de conformité
Declaration of conformity
Konformitätserklärung
Enertech AB
Box 313
S-341 26 LJUNGBY
försäkrar under eget ansvar att produkten
confi rme sous sa responsabilité exclusive que le produit,
declare under our sole responsibility that the product,
erklären in alleiniger Verantwortung, dass das Produkt,
EcoPart 400
som omfattas av denna försäkran är i överensstämmelse med följande direktiv,
auquel cette déclaration se rapporte est en conformité avec les exigences des normes suivantes,
to which this declaration relates is in conformity with requirements of the following directive,
auf das sich diese Erklärung bezieht, konform ist mit den Anforderungen der Richtlinie,
EC directive on:
Pressure Equipment Directive (PED) 97/23/EC, Modul A
Electromagnetic Compatibility (EMC) 2004/108/EC
Low Voltage Directive (LVD) 97/23/EC
Överensstämmelsen är kontrollerad i enlighet med följande EN-standarder,
La conformité a été contrôlée conformément aux normes EN,
The conformity was checked in accordance with the following EN-standards,
Die Konformität wurde überprüft nach den EN-normen,
EMC
Emission: EN55014-1:2007 EN61000-3-2:2006 -A1:2009 -A2:2009 EN61000-3-3:2008
Immunity: EN55014-2:1997 -A1:2001 -A2:2008 EN61000-4-3 -4 -5 -6 -11*)
*) Maximum permissible system impedance : Zsys1 (dmax) = 0.349Ω
LVD
SS-EN 60 335-1
SS-EN 60 335-2-40
Ljungby 2013-06-26
Marcus Miller
Technical Manager