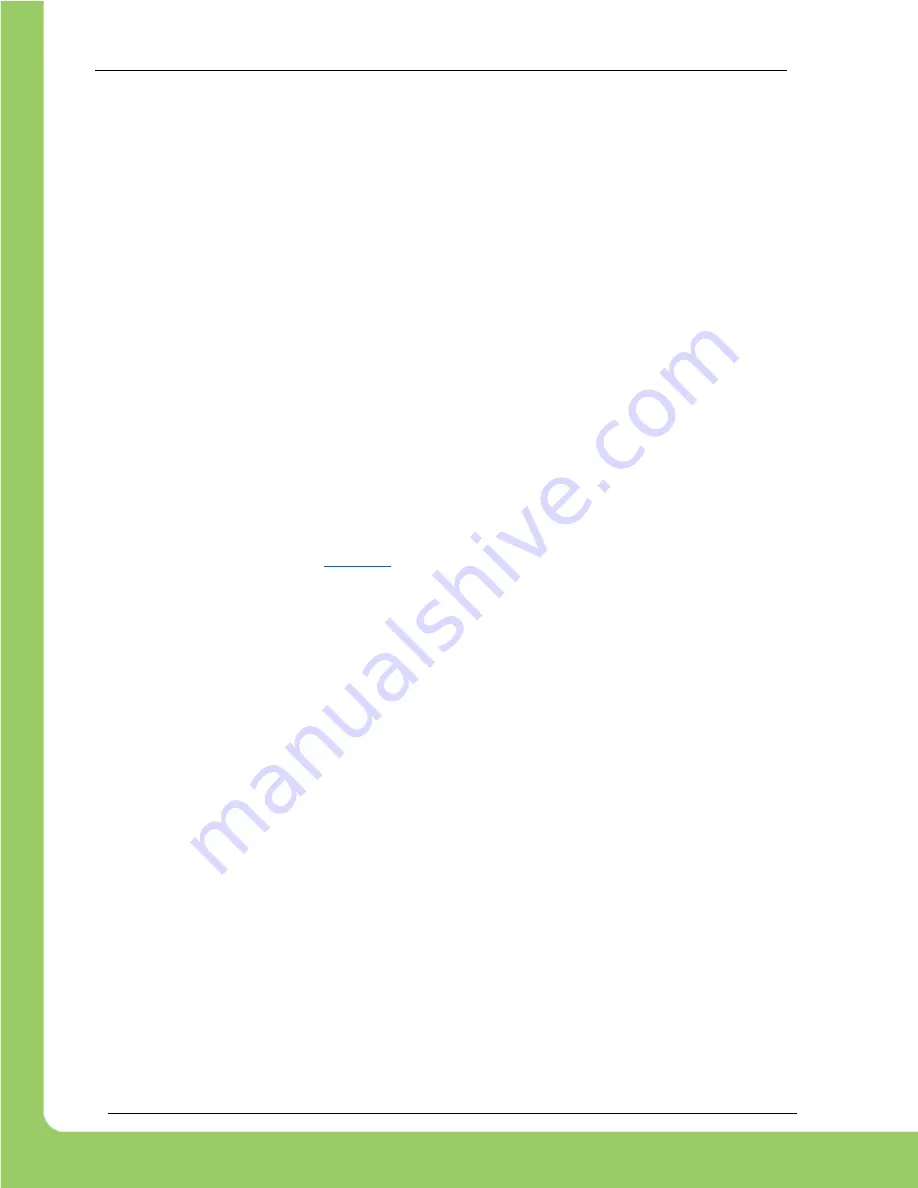
Pigeon 2.0
User’s Guide
___ www.ctr-electronics.com ______________________ 1/31/2022
Cross The Road Electronics Page 15 ____________________________ 1/31/2022
3. Calibration
3.1. Temperature Calibration
Pigeon 2.0 is factory temperature calibrated. Additional user calibration is not necessary.
3.2. Gyroscope Bias Calibration
Gyroscope is factory calibrated. Additional user calibration is not necessary.
Additionally, the gyroscope’s bias calibration is automatically
adjusted by firmware during runtime.
3.3. Gyroscope Sensitivity Calibration
Gyroscope sensitivity is factory calibrated. However, the required sensitivity precision may be application
dependent. As such there will be a future software update to allow for additional trimming.
If sensitivity error correction needs to be trimmed, calculate how many degrees your test rotation
overshot/undershot the expected result per rotation. Then configure the device with the overshot/undershot per-
rotation value.
Note that sensitivity error is positive if measurement overshot or produced a magnitude above expected value.
Similarly, sensitivity error is negative if measurement undershot or produced a magnitude below expected value.
Example below:
1.
Perform test procedure in
2.
IMU reports Yaw travel from 0 deg to -3602 deg.
3.
However mechanically IMU traveled -3600 deg.
4.
Therefore, measurement
overshot
by 2 deg.
5.
Set corrective error amount to +0.2 deg per rotation (See Phoenix API or Phoenix Tuner)
6.
Retest using above procedure to confirm improved result.
3.4. Accelerometer Calibration
Accelerometer is factory calibrated. Additional user calibration is not necessary.
3.5. Compass Calibration
2022 Pigeon 2.0 release firmware supports a compass calibration that requires rotating about the three principal
axis.
A GitHub example will be made available demonstrating how to leverage this.
Compass can then be enabled via software configuration. Note that the 9-axis compass is recommend for
outdoor
robotics applications
where stray magnetic fields caused by the environment are minimized.
We recommend leaving the compass disabled for
indoor robotics applications
as this means customers can use
the Pigeon 2 as is, with no supplemental calibration procedures.