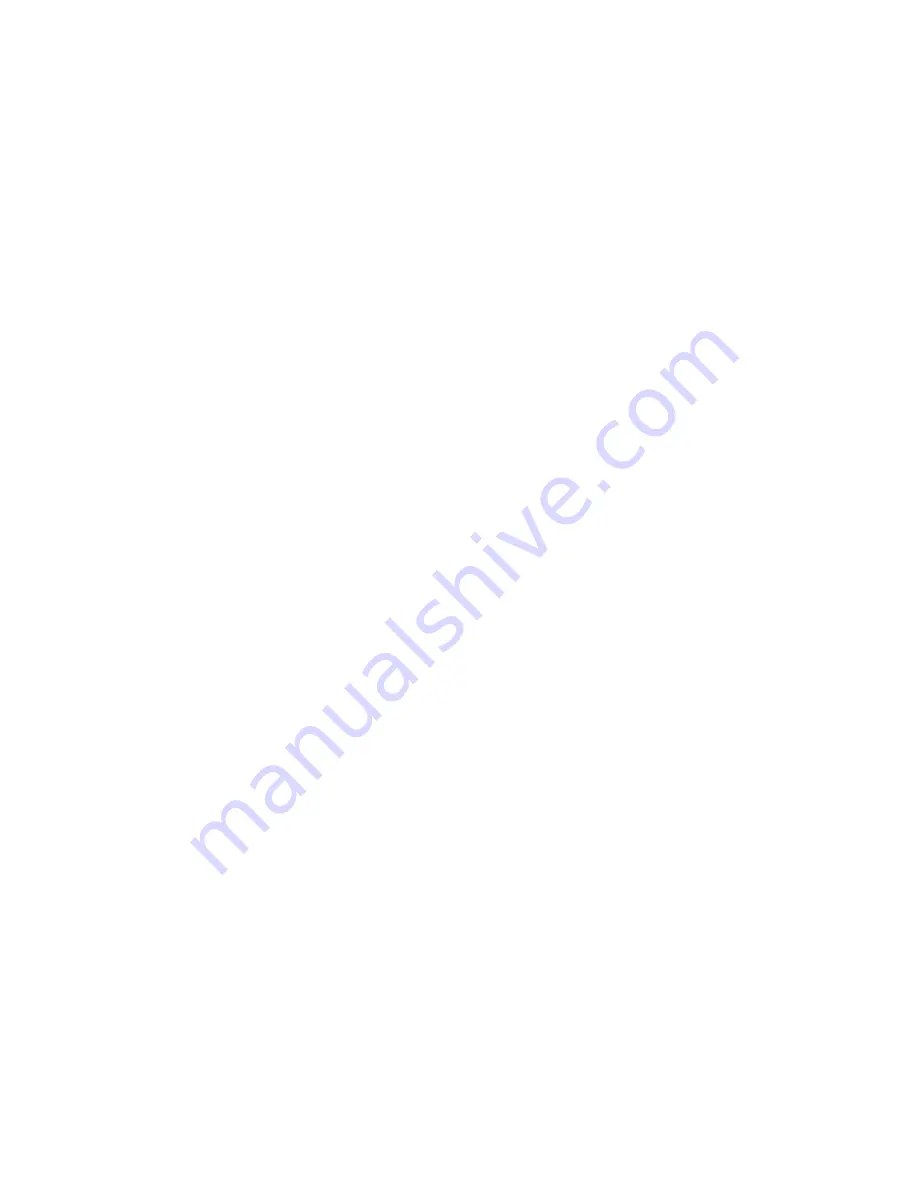
37
STORAGE
&
SHIPMENT
PREPARING THE BLOWER FOR STORAGE
In preparing the blower for storage, the inner workings of the blower must be coated
with a rust inhibiting oil. This is done by removing the air filter/silencer by turning it
counterclockwise (CCW). After the filter/silencer is removed, access to the inner
workings is possible. A rust inhibitor can then be sprayed into the blower while rotating
the blower shaft to insure all parts are oiled. A compatible rust inhibitor should also be
added to existing oil, and all bearings should be greased. Re-install filter onto blower
and cover the filter assembly with a plastic bag to prevent debris from accumulating in
the inlet tubes.
PREPARING THE ENGINE FOR STORAGE
An engine to be stored over 30 days should be completely drained of fuel to prevent
gum deposits forming on essential parts, fuel filter, and tank.
NOTE:
The use of a fuel additive, such as Dyna-Fog STA-BIL will minimize the formation
of fuel gum deposits during storage. Such an additive may be added to the
gasoline in the fuel tank of the engine, or to the gasoline in a storage container.
A. All fuel should be removed from the tank. Run the engine until it stops from lack of
fuel. The small amount of fuel that remains in the sump of tank should be removed
by absorbing it with a clean, dry cloth.
B. While the engine is still warm, drain the oil from the crankcase
.
Refill with fresh oil.
C. Remove the spark plug and pour approximately half ounce (15 cc.) of engine oil
into each cylinder and crank slowly to distribute the oil. Replace the spark plugs.
D. Clean dirt and chaff from cylinders, cylinder head fins, blower housing, rotating
screen and muffler areas.
E. Store in a clean dry area.
Summary of Contents for MAXI-PRO 2D ULV
Page 6: ...6 MAJOR COMPONENTS DIAGRAM ...
Page 9: ...9 ...
Page 39: ...39 ...
Page 43: ...43 BOOM ASSEMBLY MAXI PRO 2D P N 64905 ...
Page 50: ...50 ...