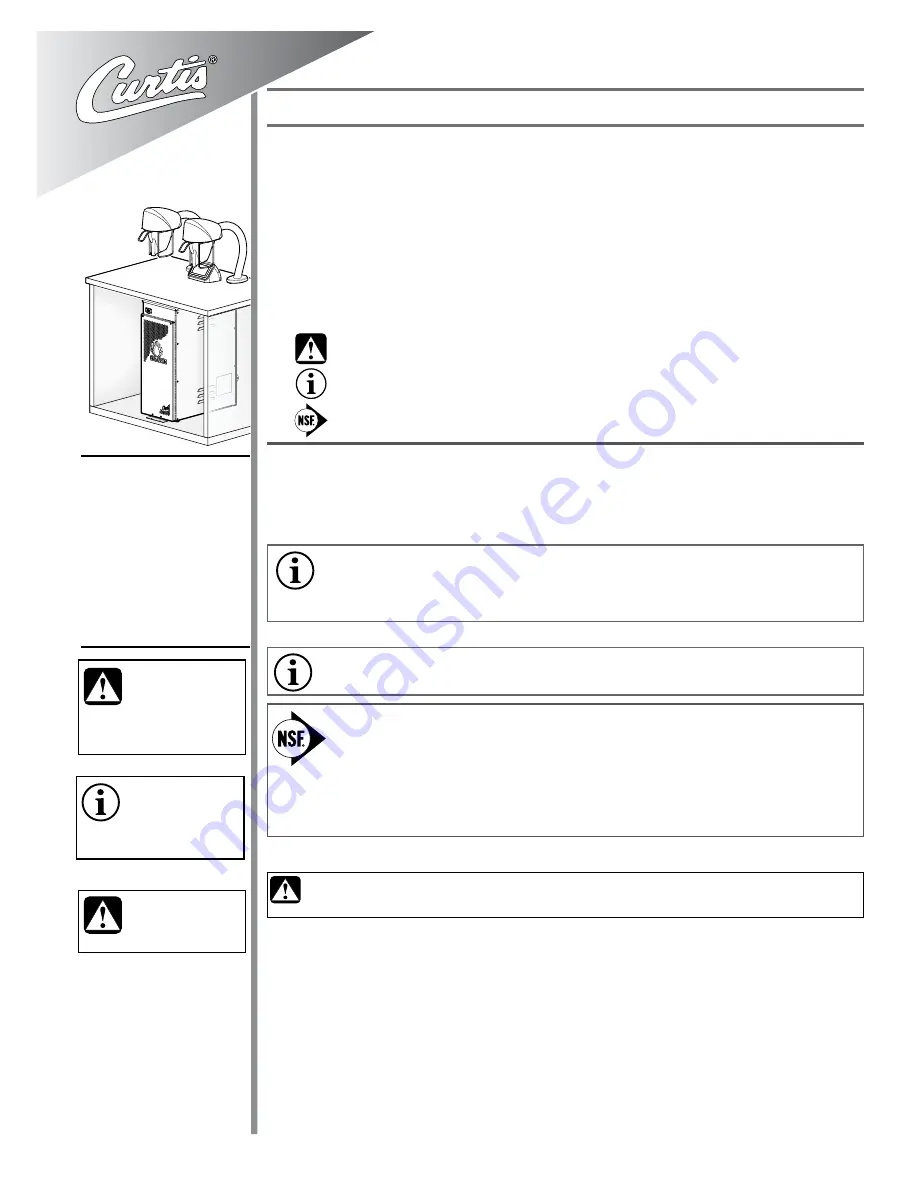
The Curtis G4 brewer is preset at the factory for optimal performance.
Following are the factory settings for the G4 Coffee Brewing System:
• Brew Temperature = 200°F • Brew Volume = Set to vessel requirement.
System Requirements:
• Water Source 20 – 90 psi (138 – 620 kPA) with a minimum flow rate of 2 gpm (7.5 lpm).
• Electrical: See attached schematic for standard model or visit www.wilburcurtis.com for your model.
INSTALLATION INSTRUCTIONS
Please adhere to these installation instructions to ensure proper set up.
Confirm that the planned location for the coffee brewer has the proper electric and water supply. In
addition, water drain pipes and the floor stability should be considered.
The water tower should be installed and grounded properly by a qualified installer or service
technician. This unit must be electrically grounded in accordance with local codes.
Carefully unpack the Seraphim brewer components from the shipping crates.
continued...
1
Models:
SERA2B, SERA2W,
SERA2W330033,
SERA2B330033,
SERA2B30,
SERA2W30,
SERA2B33,
SERA2W33,
SERA2B300293,
SERA2W300293
CAUTION:
DO NOT
connect this brewer to hot
water. The inlet valve is
not rated for hot water.
CAUTION:
Use this setup
procedure before attempt-
ing to use this brewer.
Failure to follow the instructions can
result in personal injury or void the
warranty.
IMPORTANT:
Equipment
to be installed to comply
with applicable govern-
mental plumbing/electrical codes
having jurisdiction.
ISO 9001:2008 REGISTERED
WILBUR CURTIS CO., INC.
6913 Acco Street
Montebello, CA 90640-5403
For the latest information go to
www.wilburcurtis.com
Tel: 800-421-6150
Fax: 323-837-2410
This equipment is designed for commercial use. Any servicing other than cleaning and routine maintenance
should be performed by an authorized Wilbur Curtis Co., Inc. service technician.
• DO NOT immerse the unit in water or any other liquid.
• To reduce the risk of fire or electric shock, DO NOT open service panels. There are no user serviceable
parts inside.
• Keep hands and other items away from hot areas of the unit during operation.
• Never clean with scouring powders or harsh chemicals.
Important Safeguards/Symbols
Service Manual – Seraphim Coffee Brewer
W
ilbur
C
urtis
C
o
., i
nC
.
NSF International requires the following water connection:
1. A quick disconnect or additional coiled tubing (at least 2x the depth of the unit) is required so
that the unit can be moved for cleaning.
2. This brewer must be installed with adequate back-flow protection to comply with applicable
federal, state and local codes.
3. Water pipe connections and fixtures directly connected to a potable water supply shall be
sized, installed and maintained in accordance with federal, state and local codes.
NOTE:
Electrical source should have a minimum 30 A internal common trip circuit breaker between
the brewer and the main supply, which breaks all poles with a contact separation of at least 3 mm.
NOTE:
A water filtration system must be used to help maintain trouble-free operation.
Air must be
purged from the cartridge prior to connection to equipment.
In areas with extremely hard water,
we highly recommend the use of a Curtis approved water filter. For our full line of filters, please visit
www.wilburcurtis.com.
Symbols:
WARNING
/
CAUTION
– To advise about conditions that may result in property damage,
personal injury or death
IMPORTANT
– Notes about proper operation
Sanitation requirements
CAUTION: Avoid Injury.
Do not turn on water or electricity until the brew head and water tower
assemblies are properly installed.