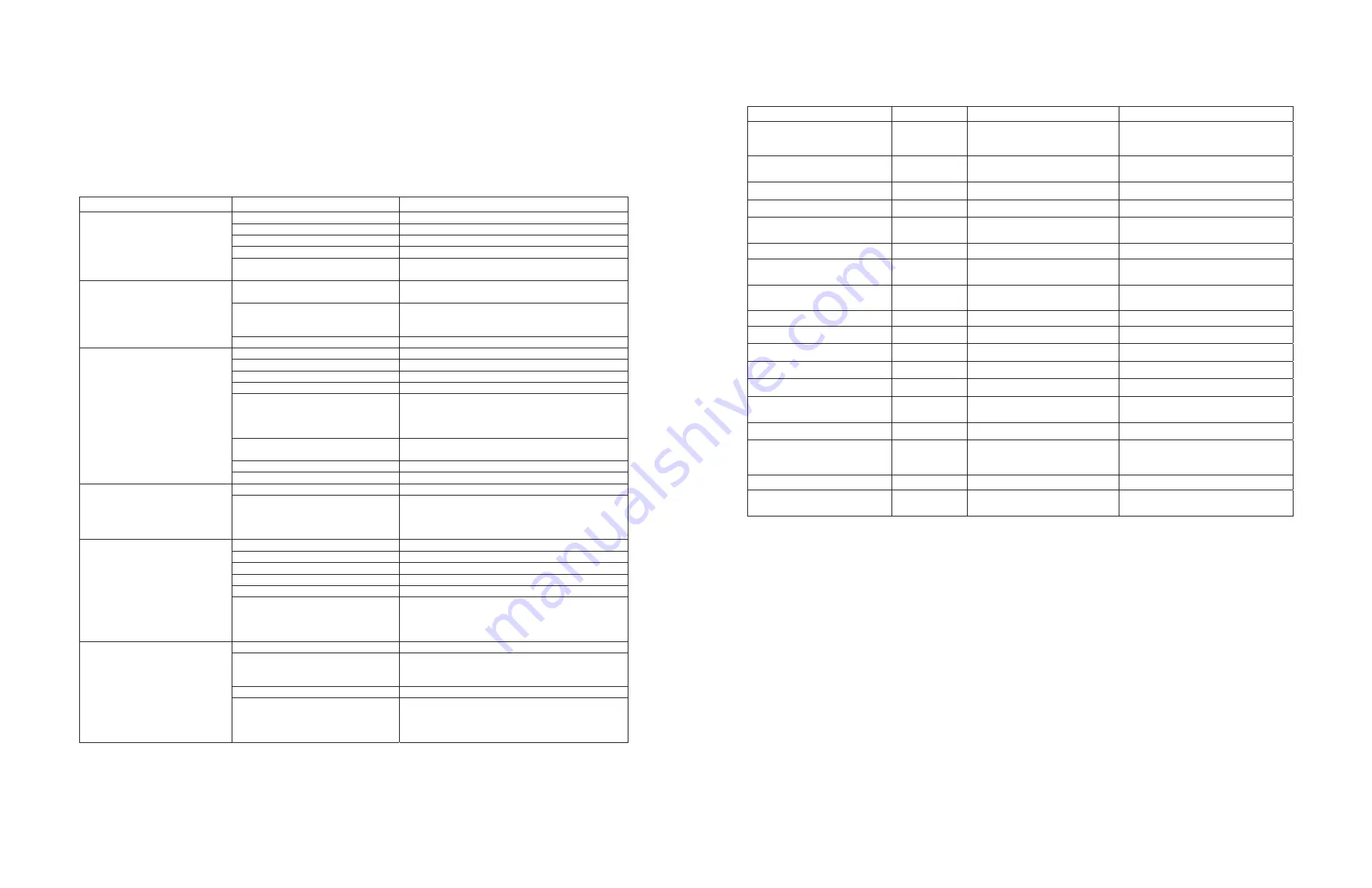
HB1030E Manual Revision: 7 Page 19 of 28
Troubleshooting
If unit is not functioning, check the following:
x
Battery is connected.
x
Key Switch is turned on.
x
Emergency stop switches are reset.
x
Enable Switch is held in for driving.
Troubleshooting Table
Problem Possible
Cause
Solution
Pump will not operate.
Key switch in
OFF
position.
Turn key switch to
ON
position.
Emergency stop activated.
Pull out emergency stop button.
Battery not sufficiently charged.
Fully charge battery.
Electrical circuitry defective.
Repair or replace wiring as needed.
Defective pump motor.
Remove pump assembly and obtain replacement
pump from factory.
Pump operates; lift will not
ascend.
Hydraulic fluid level low.
With platform lowered, fill pump reservoir to 1"
below top of reservoir.
Dump valve on pump stuck open.
Flush valve by simultaneously pressing the up
switch at base and the down switch on platform
control for 30 sec.
Emergency down valve open.
Close emergency down valve.
Ascent speed slow or erratic.
Battery not sufficiently charged.
Fully charge battery.
Emergency down valve open.
Close emergency down valve
Loose electrical connection.
Inspect & ensure all connections are secure.
Momentary short in wiring.
Repair or replace wiring as needed.
Foreign matter lodged in dump
valve.
Flush valve by simultaneously pressing the up
switch at base and the down switch on platform
control for 30 sec. If problem continues, replace
dump valve.
Bent structural member(s).
Make arrangements
w
/ factory to have member(s)
replaced.
Restriction in hydraulic hose.
Replace defective hydraulic hose.
Gears in pump worn or defective.
Return pump assembly to factory for replacement.
Descent speed slow.
Obstruction in hydraulic hose.
Replace defective hydraulic hose.
Obstruction in dump valve.
Flush valve by simultaneously pressing the up
switch at base and the down switch on platform
control for 30 sec. If problem continues, replace
dump valve.
Unit will not descend.
Key switch on
OFF
position.
Turn key to
ON
position.
Emergency stop activated.
Pull out emergency stop button.
Battery not sufficiently charged.
Fully charge battery.
Loose electrical connection.
Inspect & ensure all connections are secure.
Faulty dump solenoid.
Replace dump solenoid.
Actuated velocity fuse.
Check for hydraulic leak and repair as needed.
Reset velocity fuse by elevating platform
w
/
hydraulic pump. Check that the unit has proper
hydraulic fluid. Replace if needed.
Unit creeps down.
Emergency down valve open.
Close emergency down valve.
Foreign matter lodged in dump
valve.
Flush valve by simultaneously pressing the up
switch at base and the down switch on platform
control for 30 sec.
Defective down valve.
Replace down valve.
Damaged seal in hydraulic cylinder.
Replace hydraulic seals in cylinder
w
/ seal kit
available from factory.
Note:
If walls inside
cylinder are scratched or pitted, cylinder must be
replaced.
HB1030E Manual Revision: 7 Page 20 of 28
Motor Control Status LED Diagnostics
Programmer Display
LED Code Explanation
Possible Cause
THERMAL CUTBACK
¤ ¤
Over-/under-temp. cutback
1.
Temperature >92º C or <-25ºC.
2.
Excessive load on vehicle.
3.
Electromagnetic brake not releasing
properly.
THROTTLE FAULT 1
¤ ¤¤
Pot high or pot low signal out
of range
1.
Throttle input wire open or shorted.
2. Throttle
pot
device.
3. Wrong
type
selected
SPD LIMIT POT FAULT
¤ ¤¤¤
Speed limit pot fault
1.
Speed limit pot wire(s) broken or shorted.
2.
Broken speed limit pot.
LOW BATTERY VOLTAGE
¤ ¤¤¤¤
Battery voltage too low
1.
Battery voltage <17 volts.
2.
Bad connection at battery or controller.
OVERVOLTAGE
¤ ¤¤¤¤¤
Battery voltage too high
1.
Battery voltage >36 volts.
2.
Vehicle operating with charger attached.
3.
Intermittent battery connection.
MAIN OFF FAULT
¤¤ ¤
Main cont. Off fault
1.
Main contactor drive failed open.
MAIN CONT WELDED
¤¤ ¤¤
Main contactor did not open
1.
Main contactor welded.
2.
Main contactor driver fault.
3.
Brake coil resistance too high.
MAIN CONT DNC
¤¤ ¤¤¤
Main contactor did not close
1. Main
contactor
stuck
open.
2.
Main contactor driver fault.
3.
Brake coil resistance too high.
MAIN ON FAULT
¤¤ ¤¤¤¤
Main cont. driver On fault
1.
Main contactor driver failed closed.
PROC/WIRING FAULT
¤¤¤ ¤
HPD fault present > 100 sec.
1. Misadjusted
throttle.
2.
Broken throttle pot or throttle mechanism.
BRAKE ON FAULT
¤¤¤ ¤¤
Brake on fault
1.
Electromagnetic brake driver shorted.
2.
Electromagnetic brake coil open.
PRECHARGE FAULT
¤¤¤ ¤¤¤
Brake off fault
1. Controller
failure.
2.
Low battery voltage.
BRAKE OFF FAULT
¤¤¤ ¤¤¤¤
Precharge fault
1.
Electromagnetic brake driver open.
2.
Electromagnetic brake coil shorted.
HPD
¤¤¤ ¤¤¤¤¤
HPD fault
1.
Improper sequence of throttle and KSI,
push, or inhibit inputs.
2. Misadjusted
throttle
pot.
CURRENT SENSE FAULT
¤¤¤¤ ¤
Current sense voltage fault
1.
Short in motor or in motor wiring.
2. Controller
failure.
HW FAILSAFE
¤¤¤¤ ¤¤
Motor voltage fault
1.
Motor voltage does not correspond to
throttle request.
2.
Short in motor or in motor wiring.
3. Controller
failure.
EEPROM FAULT
¤¤¤¤ ¤¤¤
EEPROM fault
1. EEPROM failure or fault.
POWER SECTION FAULT
¤¤¤¤ ¤¤¤¤
Output section fault
1.
EEPROM failure or fault.
2.
Short in motor or motor wiring.
3.
Controller
failure.
Gp102 Control Module LED Diagnostics
LED on steady This indicates no fault with the
GP102
LED off always This indicates no power to the
GP102
, or idle timeout – activate a lift or drive function to cancel the idle timeout.
LED flash code 1 This indicates the
GP102
has not been properly calibrated.
LED flash code 2 This indicates a fault with the switch inputs to the
GP102
. Check wiring to connector P2.
LED flash code 3 This indicates a fault with the shutdown outputs of the
GP102
– a short to the supply has been detected. Check wiring from
pins P3-4 and P3-6.
LED flash code 4 This indicates that armguard is active, or that there is a fault with the elevation switch – the
GP102
verifies correct opening
and closing of the elevation switch against the height sensor. Checking the elevation switch on P2-10. If the height sensor has been
adjusted or replaced, repeat the CALIBRATE HEIGHT procedure.
LED flash code 5 This indicates a fault with the shutdown outputs of the
GP102
– a short to 0V (ground) has been detected. Check wiring from
pins P3-4 and P3-6.
LED flash code 6 This indicates a fault with the load measurement – check the pressure transducer and wiring from it to connector P4.
LED flash code 7 This indicates a fault with the supply to the
GP102
– check battery supply at least 8V on pin P2-12; also check that there is
not a short to 0V (ground) on pin P4-1. If load cells or strain gauges are connected to P5A/P5B/P6A/P6B, disconnect them – if the
fault changes then one or more is shorting the supply on each pin 1.
LED flash code 8 This is not a fault – it indicates the
GP102
has prevented a function; functions can be prevented if the platform is overloaded,
if the machine is tilted too far, or if the platform is too high.
LED flash code 9 This indicates a fault with the height measurement – check the height transducer (
EZfit
) and wiring from it to connector P4.