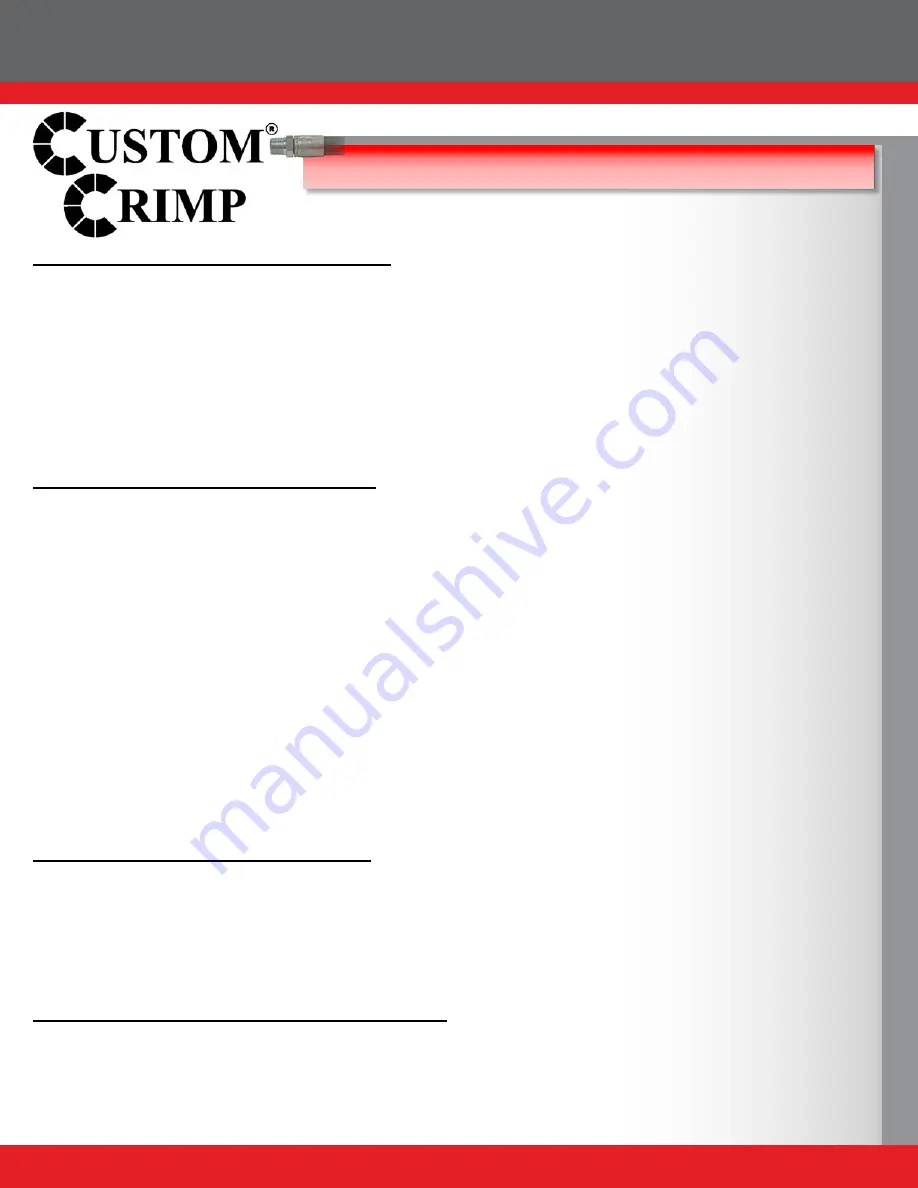
D165-T420 SERIES
Service Hose Crimpers
24
PROBLEM: CRIMPER WILL NOT RUN AT ALL
• The white rocker switch is also a circuit breaker. Check to see that the circuit breaker has not been tripped.
• Check the wall outlet. The crimper comes from the factory wired for a 115 volt single phase circuit. Use of extension
cords or outlets with inadequate power can damage the motor. Do not run the crimper from a portable power source.
• Check the stop switch mounted to the switch bracket under the Micro-Crimp Adjuster. This is a normally closed switch
and if it does not close the crimper will not operate.
CAUTION: Do not operate the crimper with this switch jumpered as the pump will not shut off and the brackets can be
damaged.
• Check the pneumatically actuated switch in the electrical box mounted on the motor. This switch controls power to the
motor and is actuated with air pressure from the pendant switch bulb.
PROBLEM: CRIMP DIAMETER TOO LARGE
•
Incorrect setting of the Micro-Crimp Adjuster. Check crimp specifications.
(NOTE: All published machine settings are approximate. To correct for slight variances, the gauge settings may need
to be adjusted for the specific hose, fitting and size combination).
•
Incorrect die being used. Each die has a useable range of approximately 3mm (.120 in) above the closed diameter
of the die. The closed diameter is the die size stamped on the die ring.
•
Check crimper calibration and re-calibrate if required.
•
Inadequate pump pressure. Check oil level in the pump. It should be 1-1/2 to 2 inches below the fill plug.
•
Replenish with ISO Viscosity Grade 46 hydraulic oil.
•
Inadequate lubrication of the dies and compression ring causing the pump to work harder than normal to reach the required
diameter. Use only the crimpx oil / grease shipped with the machine or a high pressure molybdenum high pressure
grease (equivalent).
•
Inadequate pressure being generated by the pump. This is most likely if the crimper can crimp the smaller size hoses
and not the larger hoses. When correctly adjusted, the pump should generate approximately 10,000 psi.
Do Not adjust pump to produce in excess of 10,000 psi as damage to components or personal injury may result.
•
No pressure being generated by the pump. There should be a definite change in pitch of the pump as it cycles into
high pressure mode and begins to “work” harder.
PROBLEM: CRIMP DIAMETER TOO SMALL
•
Incorrect setting of the Micro-Crimp Adjuster. Check crimp specifications
.
( NOTE: All published machine settings are approximate. To correct for slight variances, the gauge settings may be
adjusted for the specific hose, fitting and size combination).
•
Incorrect die being used (See die range under Crimp Diameter Too Large).
•
Check crimp diameter and re-calibrate if necessary.
PROBLEM: DIES STICKING IN COMPRESSION RING
•
Inadequate lubrication of the compression ring and die surfaces. Use only the crimpx oil / grease shipped with the machine
or a high pressure molybdenum high pressure grease (equivalent).
•
Refer to D165 Lubrication Procedure for more details.
TROUBLESHOOTING