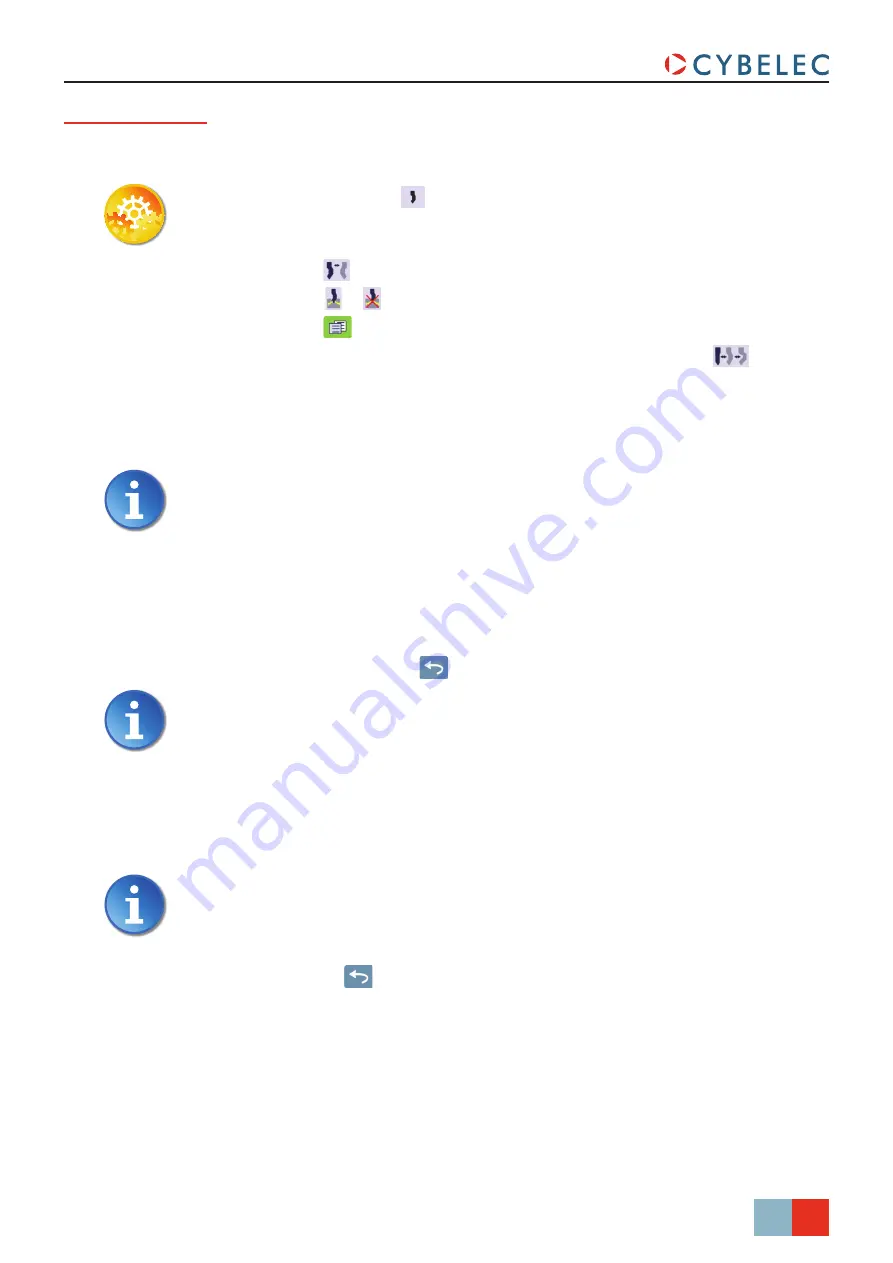
19/38
S
ept
.
2014
V3.1
CybTouch 12 PS User Manual
How to create or
modify a punch?
If no punch is yet created, the punch will have no name (
???
is displayed). If a punch
already exists, then the last punch used will be selected, here
60_N
(modifications will
not alter the existing punch as they will be saved under another name).
1. Touch the punch icon
to access the punch details.
2. Enter the basic characteristics (
α
(punch angle),
Height
,
Radius
and
Ton/m
) for the
new punch to be created.
3. Touch the
button to invert the punch if necessary.
4. Select the or icon to define the tool as resistant for bottoming.
5. Touch the
button to display the More page.
6. Select the punch type (straight, normal or gooseneck) with this icon
.
7. Enter the more specific dimensions L1 to Lx by referring to the graphic
representation on the right of the screen. Touching this image will display the default
representation of the tool, making it easier to identify the various dimensions.
The dimensions L1 to Lx are the same as the ones used in PC 1200, DNC 880S,
ModEva’s. If you use the same tools, print them from PC1200 to easily program
them in the CybTouch. Of course consider giving the same tools the same
name.
8. Enter the following values:
•
Safety XS
:
Security distance between the tool and the back gauge for X axis.
•
X correction
: If the punch is not perfectly aligned.
9. Return to previous page
.
To be allowed to save a tool, a level 2 password is required.
10. Touch the punch name (here 60_S_i).
11. Touch
Save punch
to overwrite the existing tool or
Save punch as
if you want to
save your tool under another name.
12. Enter the name of the new punch using the alphanumerical keypad.
We recommend that you follow the naming conventions explained in
13. Touching the
button brings you back to the program page, with the punch you
just saved being selected and ready to be used.