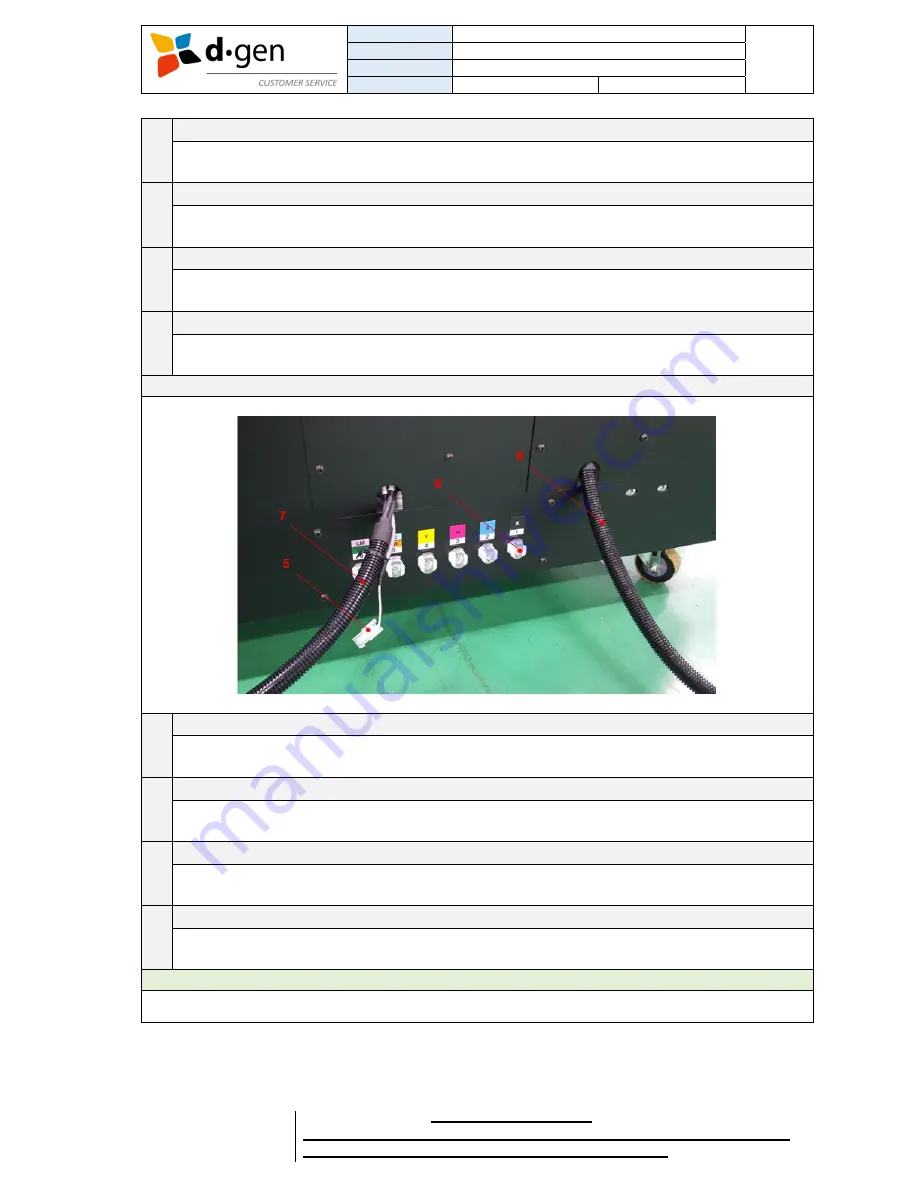
TITLE
OPERATOR MANUAL
PAGE
PRINTERS
PAPYRUS G5/H4, PAPYRUS G5/H6
11
VERSION
2017JAN23/1
OUT OF
REVISED BY
MUNOZ, ANTONIO
support@dgen.com
51
FOR THE USER
d·gen International, Inc. - COMPANY PRIVATE (LEVEL 1)
NOT TO BE DISCLOSED TO UNAUTHORIZED PERSONS – PROHIBIDA SU DIVULGACIÓN A PERSONAS NO AUTORIZADAS
DO NOT REPRODUCE WITHOUT AUTHORIZATION – NO REPRODUCIR SIN AUTORIZACIÓN
1
Cover.
Buzzer can be heard if this cover is opened. Cover normally closed when using the printer.
2
Lid and ink filter.
We suggest to pour the ink on the filter. Also, is suggested not to close the lid totally to let the air
flow in while the cylinder is getting empty.
3
Cover switch.
This device activated the buzzer when the cover is opened for refilling the inks.
4
Ink level photo sensor.
This photo sensor measures the ink level with a laser beam. Keep this area always free of ink.
BIG INK SYSTEM (BACK SIDE)
5
White LED bar’s power connector.
This cable powers up the white LED light bar in the Big Ink System.
6
Ink outlets.
By pushing down the silver fastening is possible to release or insert the ink line without spilling ink.
7
Sensor level connector (K C M Y inks).
This connector sends the signal from the photo-sensors located in the Big Ink System (to measure
the ink level in the cylinder) to the LED ink level indicators.
8
Sensor level connector (SP1 and SP2 inks).
This connector sends the signal from the photo-sensors located in the Big Ink System (to measure
the ink level in the cylinder) to the LED ink level indicators.
Important
Keep always the ink level’s photo sensor emitter and reflector free of ink and dust.
Summary of Contents for Papyrus G5/H4
Page 1: ...OPERATOR MANUAL ...