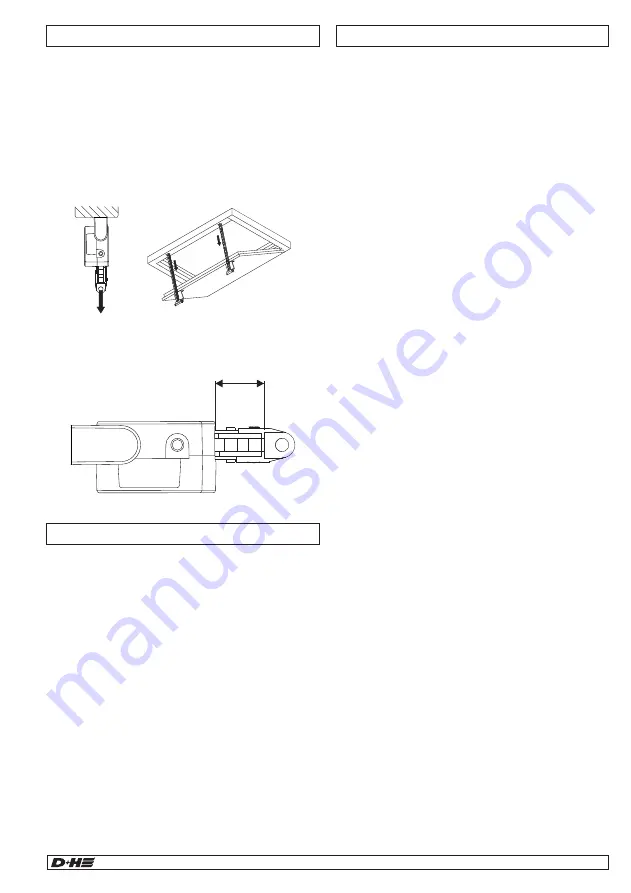
99.827.73 1.0/10/18
VCD-0203-1-ACB-R
VCD-0203-1-ACB-R
6/16
7/16
99.827.73 1.0/10/18
English
English
Closing edge protection
In the "CLOSE" direction the drive has an active
protection for the main closing edge. If there is an
overload in the closing ranges C3 and C2, the drive
runs "OPEN" for 10 seconds, then "CLOSE" again. If
closing is not possible after three attempts, the drive
remains in this position.
In addition, the drive is equipped with passive
protection. The closing speed in closing range C2
and C1 is reduced to 5 mm/s.
Significantly greater forces can be
exerted at the secondary closing
edges. Danger of crushing hands and
fingers!
Main closing edge
Beside closing edge
Beside closing edge
C3*
200 N
Opening and Closing Ranges
O1*
C1*
C2*
O2*
O3*
23 mm
150 N
77 mm
150 N
23 mm
200 N
15 mm
200 N
200 N
Technical Data
* Programmable with software SCS ** + approx. 20 % switch-off reserve (temporary)
Type
VCD-0203-0250-1-ACB-R
Power supply
Nominal force
24 V DC / ± 20 %
200 N**
Nominal current
0,35 A
Nominal stroke length*
250 mm
±
2 %
Running speed:
O1, O2
O3
C3
C2, C1
6 mm/s
5 mm/s
6 mm/s
5 mm/s
Nominal locking force
Service life
Duty cycle
Housing
Ingress protection
Temp. range
Ambient humidity
Emission sound pressure level
Additional functions*
approx. 2000 N (Excluding bracket)
>20.000 double strokes
30 % (With cycle time 10 minutes)
Zinc-diecasting powdercoated (~ RAL 9006)
IP 30
0 ... +60 °C
≤ 90 %, not condensing
LpA ≤ 46 dB(A)
Closing edge protection = activated (3 repetitions of stroke);
Locking relief = activated (retraction lift max. 0,2 mm)
ACB interface
Modbus RTU / RS 485, 19.200 bps, 8 data bits, 1 stop bit, parity: even
- The drive set is fully configured ex factory.The
drives must be reconfigured using the software
SCS in the event of changes to the ex-factory
configuration (e.g. when removing a drive from
existing set or integrating a new drive).
- Mount the drives whilst under zero stress. With
that, an even load distribution is provided by all
the drive chains.
- At vertical active pulling application (e.g. for a
skylight) the forces must be rearranged by
software SCS.
- If after mounting, the distance X is greater than 23
mm, null balance with software SCS is neccesary.
Closure Ranges will shift in relation to new zero
point.
Mounting information
ACB interface
ACB is used for secure communication between
the drive and compatible D+H control systems. It
enables activation, diagnostics and configuration
with perfect position, directly from the control
panel. In this process, all status messages, such
as the OPEN and CLOSED signals, opening
stroke and drive errors are transmitted to the
control panel.
The ACB bus is based on an open Modbus RTU
protocol via which the actuator can be directly
controlled and queried.
Further information can be found in the D+H ACB
Planning Manual.
BSY+ synchronised electronics:
A synchronous group can contain up to 8 drives,
which communicate via bus. Each drive has its
own address, configurable with SCS.
The last drive of a synchronous group is the
master, which controls the other drives, the slaves.
Differences in forces between the drives of a group
are balanced by means of intelligent force and
position control. In the event that a drive
malfunctions, all the drives are automatically cut
off.
In addition, up to 4 BSY+ lock drives and modules
can be connected.
Functional description
Visual inspection:
Only one master drive is allowed.
The master always has the last address of all the
drives; this can be found on a sticker attached to
the drive. Slaves are numbered downwards from
the master, so that in a group of three drives, for
example, the master is no. 3, with a slave 2 and
slave 1 drive. Please note that this only applies in
the ex-factory configuration. As soon as the drives
are reconfigured with SCS, the ex-factory
addressing no longer applies.
Wiring:
Is the drive or drive group wired properly?
See connection plans.
Diagnostics with SCS software:
The SCS software and a BSY+ interface is
required for further troubleshooting or
configuration.
Troubleshooting
≥ 23 mm ?
X