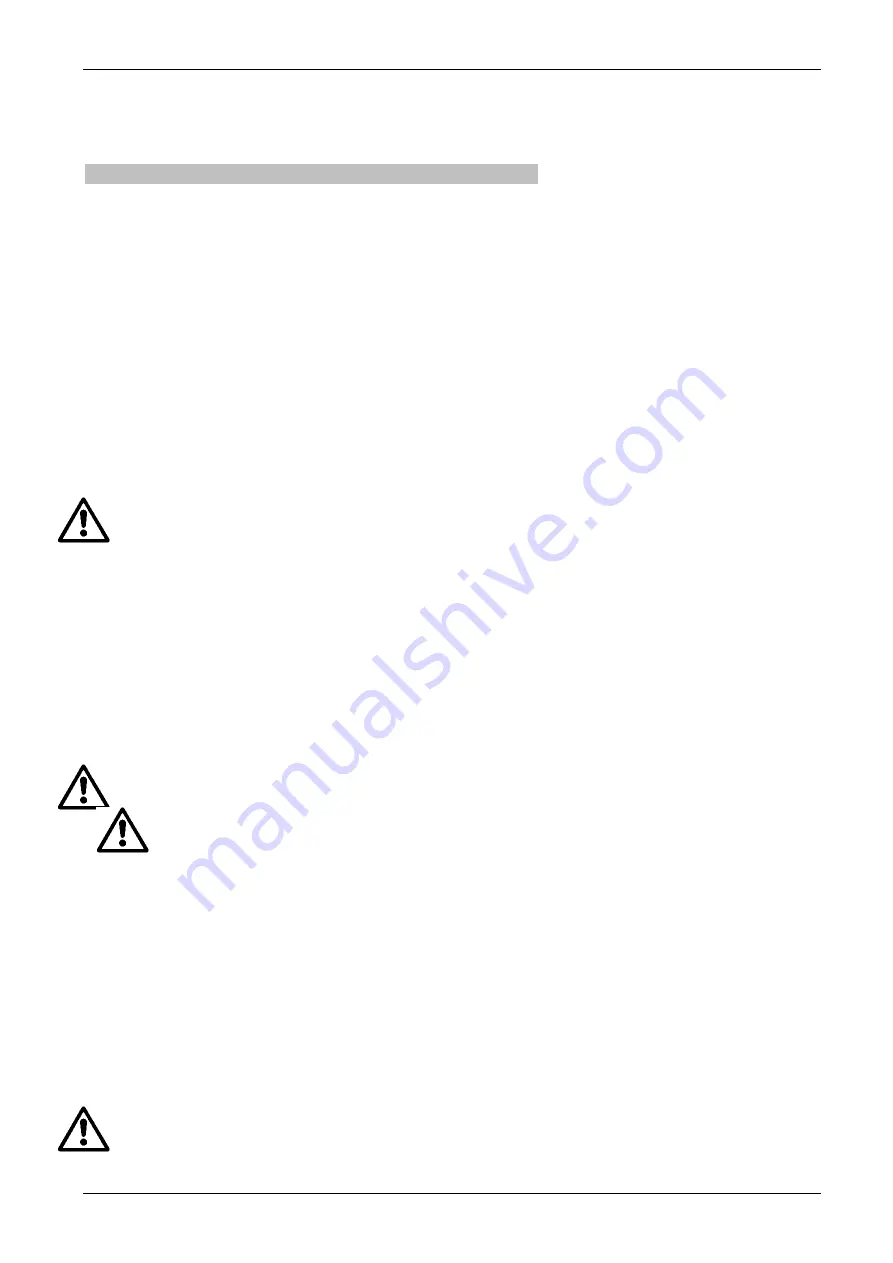
ENGLISH
50
Eb = 2 : The master-booster operating mode is enabled, therefore 2 electric pumps can be activated at the
same time. If during operation the master electric pump is not able to meet the utility requirements,
the booster electric pump will also be switched on and will work at the maximum frequency, while
the master machine will continue to modulate the rotation frequency according to the utility.
1.15
OPERATION: TECHNICAL ASSISTANCE MENU
Access keys MODE and SET and “+” for 5 seconds
1.15.1
tb : Setting the reaction time of the water low block
The setting of the reaction time of the water low block allows you to select the time (in seconds) taken by the
system to indicate the lack of water in the electric pump. The variation of this parameter may be useful if it is
known that there is a delay between the moment in which the electric pump is switched on and the moment
in which it actually starts delivering.
1.15.2
t1 : Running time after low pressure signal (kiwa)
This time is only active when the input is set to 3 or 4.
If a low pressure event is detected, as indicated on input 1, the ACTIVE DRIVER waits for the interval t1
and then shuts down, displaying F1. Reset may be automatic when the correct pressure is restored, or manual
by pr and - simultaneously.
1.15.3
t2 : Delay time in event of shutdown conditions
The setting of the delay time in the event of shutdown conditions enables the selection of the time interval
after which the ACTIVE DRIVER switches off the pump when shutdown conditions are present (in
seconds).
NOTE: If the ACTIVE DRIVERS are used, configured in communication mode and set to restart
according to Kiwa standards, the minimum pressure switch must be connected to input 1 of both
inverters and the parameters "i1", "t1" and "t2"must be manually aligned.
1.15.4
GP : Setting the gain of the PI proportional coefficient
For nearly all systems, the GP parameter set in the factory is the optimum value.
However, in the event
of any problems, this setting may be adjusted. As a guideline it may be said that, for example, the presence of
great variations in pressure or a slow response of the system to variations in pressure may be compensated
for by high GP values. On the other hand, pressure "vibrations" (extremely rapid pressure variations around
the set point) may be eliminated by reducing the GP value.
1.15.5
GI : Setting the gain of the PI integral coefficient
The integral value must be increased when the system is not very elastic, i.e. where there is no expansion. On
the contrary, in systems with deformable pipes or with delays due to considerable distances between the
electric pump and the ACTIVE DRIVER, the integral value must be lowered.
To obtain satisfactory pressure settings, both GP and GI should be adjusted. In fact only the correct
combination of these two parameters will enable the optimum pressure setting.
A typical example of a system in which the values GI and GP should be reduced is that in which
the inverter is located far from the electric pump. Reduce the values of GI and GP by half for
pump-inverter distances of over 60m.
1.15.6
FS :
Setting the maximum rotation frequency of the electric pump
The ACTIVE DRIVER allows the electric pump to be powered for short periods at a frequency higher than
the rated frequency, limiting the maximum frequency sent to the electric pump in the event of an excessive
increase in temperature.
The value of the set maximum frequency (FS) can therefore be reached with the motor cool, with a
decrease to Fn (rated frequency) as the temperature rises in the windings.
The
ACTIVE DRIVER
also allows a maximum working frequency to be set that is lower than the rated
frequency Fn. In this case, regardless of the set condition, the electric pump will never be run at a
frequency higher than the set rated frequency.
The maximum FS is Fn + 20%, while the minimum FS is Fn – 20%.
FS will align automatically with Fn whenever a new Fn is set.
When increasing the power supply frequency, take care not to exceed the Max. motor current phase;
otherwise shutdown may occur due to final stage current overload oF.
Summary of Contents for ACTIVE DRIVER M/T 1.0
Page 275: ...270...