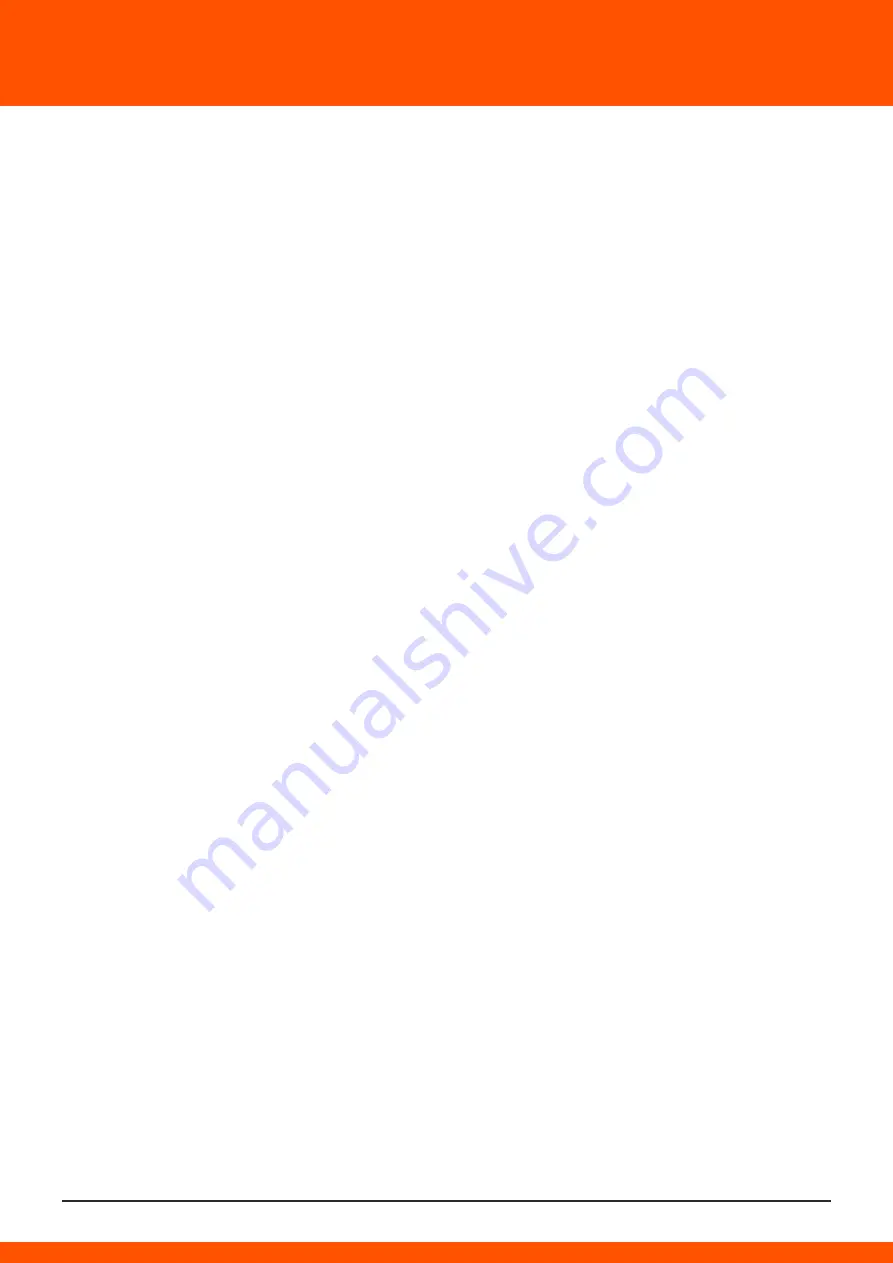
10
1. RULES FOR SAFE OPERATION
WARNING:
Failure to fallow instructions in this manual may lead to serious injury or even death! This equipment
is to be operated by trained and qualified personnel only! This equipment is far industrial use only.
The fallowing safety guidelines should always be used when operating these Floor Saws:
GENERAL SAFETY
• DO NOT operate or service this equipment befare reading the entire manual.
• This equipment should not be operated by persons under 18 years of age.
• NEVER operate this equipment without proper protective clothing, shatterproof glasses, steel-toed
boots and other protective devices required by the job.
• NEVER operate this equipment when not feeling well due to fatigue, illness or taking medicine.
• NEVER operate this equipment under the influence or drugs or alcohol.
• NEVER use accessories or attachments, which are not recommended by our company far this
equipment. Damage to the equipment and/or injury to user may result.
• The manufacturer does not assume responsibility far any accident due to equipment modifications.
• Whenever necessary, replace nameplate, operation and safety decals when they become difficult
to read.
• ALWAYS check the machine far loosened threads or bolts befare starting.
• NEVER touch the hot exhaust manifold, muffler or cylinder. Allow these parts to cool befare servi-
cing engine or saw.
• High Temperatures - Allow the engine to cool befare adding fuel or performing service and mainte-
nance functions. Contact with hot components can cause serous bums.
• The engine section of this saw requires an adequate free flow of cooling air. NEVER operate the
saw in any enclosed or narrow area where free flow of the air is restricted. lf the air flow is restricted it
will cause serious damage to the saw or engine and may cause injury to people. Remember the saw's
engine gives off DEADLY carbon monoxide gas.
• ALWAYS refuel in a well-ventilated area, away from sparks and open flames.
• ALWAYS use extreme caution when working with flammable liquids. When refueling, stop the
engine and allow it to cool. DO NOT smoke around or near the machine. Fire or explosion could result
from fuel vapors, or if fuel is spilled on a hot engine.
• NEVER operate the saw in an explosive atmosphere or near combustible materials. An explosion or
fire could result causing severe bodily harm or even death.
• Topping-off to the fue/ filler port is dangerous, as it tends to spill fuel.
• NEVER use fuel as a cleaning agent.
• ALWAYS read, understand, and fallow procedures in operator's Manual befare attempting to opera-
te equipment.
• ALWAYS be sure to operator is familiar with proper safety precautions and operating techniques
befare using the saw.
• Stop the engine when leaving the saw unattended.
• Block the unit when leaving or when using on a slope.
• Maintain this equipment in a safe operating condition at all times.
• ALWAYS stop the engine befare serving, adding fuel and oil.
• NEVER run engine without air filter. Severe engine damage may occur.
• ALWAYS service air cleaner frequently to prevent carburetor malfunction.
• ALWAYS store equipment properly when it is not being used. Equipment should be stored in a
clean, dry location out of the reach of children.
• NEVER operate this cutter in areas that contain combustible material or fumes. Fire and/or exploIV
LUBRICATION AND SERVICE from the equipment.
• DO NOT operate this equipment unless all guards and safety devices are attached and in place.
• Caution must be exercised while servicing this equipment. Rotating and moving parts can cause
injury if contacted.
• Keep all inexperienced and unauthorized people away from the equipment at all times.
• Unauthorized equipment modifications will void all warranties.
DIAMOND BLADE SAFETY
• Use appropriate steel centered diamond blades manufactured for use on Floor Saws.
• ALWAYS inspect diamond blades befare each use. The blade should exhibit no cracks, dings, or
flaws in the steel centered core and/or rim. Center (arbor) hole must be undamaged and true.
• Examine blade flanges far damage, excessive wear and cleanliness befare mounting blade. Blade
should fit snugly on the shaft and against the inside/outside blade flanges.
• Ensure that the blade is marked with an operating speed greater than the blade shaft speed of the
saw.
• Only cut the material that is specified by the diamond blade. Read the specifications of the
diamond blade to ensure the proper tool has been matched to the material being cut.
• ALWAYS keep blade guards in place. Exposure of the diamond blade must not exceed 180 degrees.
• Ensure that the diamond blade does not come into contact with ground or surface during transpor-
tation. DO NOT drop the diamond blade on ground or surface.
• The engine governor is designed to permit maximum engine speed in a no-load condition. Speeds
that exceed this limit may cause the diamond blade to exceed the maximum safe allowable speed.
• Ensure that the blade is mounted far proper operating direction.
FLOOR SAW TRANSPORTATION SAFETY
• Use the lifting bail and appropriate lifting equipment to ensure the safe movement of the saw.
• DO NOT use the handle bars and/or front pointer as lifting points.
• NEVER tow the saw behind a vehicle.
• Ensure that both pointer bars are positioned appropriately to minimize their exposure during trans-
portation.
• Safeguard against extreme saw attitudes relative to level. Engines tipped to extreme angles may
cause oil to gravitate into the cylinder head making the engine difficult to start.
• NEVER transport the saw with the blade mounted.
EMERGENCIES
• ALWAYS know the location of the nearest fire extinguisher and first aid kit. Know the location of the
nearest telephone. Also know the phone numbers of the nearest ambulance, doctor and tire depart-
ment. This infarmation will be invaluable in the case of an emergency.
MAINTENANCE SAFETY
• NEVER lubricate components or attempt service on a running machine.
• ALWAYS allow the machine a proper amount of time to cool befare servicing.
• Keep the machinery in running condition.
• Fix damage to the machine immediately and always replace broken parts.
• Dispose of hazardous waste properly. Examples of potentially hazardous waste are used motor oil,
fuel and fuel filters.
• DO NOT use faod or plastic containers to dispose of hazardous waste.
2. OPERATION
lntroduction/Determining the Right Machine
Congratulations on your purchase of our saw! You've made an excellent choice! Our floor saw has
been specifically designed as the ideal machine far the professional contractor who is engaged in
concrete and asphalt flat cutting.
The machines used far the primary purpose of "flat" cutting. This type of cutting is described as
"flat" because the pavement is cut somewhere clase to a horizontal plane. lt is the most common
type of diamond blade cutting.
Floor saws in the industry are available in a variety of types, sizes and styles, they range from manual
or self propelled in horsepower from 7-72hp. lt is possible to cut both concrete (green or cured, with
or without rebar) or asphalt with a floor saw. Our saw utilized far jobs requiring precision cutting
including floors, pavements, walkways, ramps and other flat sawing applications.
You will find a saw to fit a wide variety of job applications.
Upan receipt of your machine, CAREFULLY CHECK FOR ANY FREIGHT DAMAGE. Any damage
should be immediately reported to the carrier and a claim registered.
Operating Principle/Delivery Checks/
lnstalling Blade/Types of Cutting
OPERATING PRINCIPLE
The fallowing instructions were compiled to provide you infarmation on how to obtain long and
trouble free use of the unit. Periodic maintenance of this unit is essential. Read the manual in its
entirety and fallow the instructions carefully. Failure to do so may injure yourself or a bystander.
DELIVERY CHECKS
lmmediately upan taking delivery of your new equipment and befare putting it into service:
• Read the handbook completely-it could save a great deal of unnecessary expense.
• Read the engine manual supplied.
• Check the general condition of the equipment-has it been damaged during delivery?
• Check engine oil level.
• Check fuel levels.
Recommend lubricants are detailed in the CARE AND MAINTENANCE section.
INSTALLING BLADE
1. Be certain that the spark plug is disconnected or saw is unplugged.
2. Remove the blade shaft nut, and take off outside blade shaft flange.
3. Clean off any fareign particles on the clamping surfaces of flanges and on the mounting surface of
the blade.
4. Place the blade on the blade shaft, lining up the offset drive pin in the blade with the drive pin in
the mounting collar (if the pin system is available on the machine). lf your blade has a directional
ratational arraw, position arraw far down cut (diamond tail trailing far down cut).
5. Replace the outside blade shaft flange on the blade shaft. Orive pin on the inside collar must
praject thraugh the drive hale in the blade and into the outside collar (if the pin system is available on
the machine).
6. Tighten the blade shaft nut securely against star washer and outside flange, using wrench
supplied.
7. Reconnect the spark plug or (with switch "off") plug in the electric supply cord.
TYPES OF CUTTING
Cut speed depends entirely on using the correct blade far the material to be cut. Wet or dry, diamond
blades of various specifications are available far cutting concrete or asphalt.
Befare Starting/Cold Start/Hot Start/
To Start Cutting
BEFORE STARTING
1. Use correct blade far cutting conditions.
2. Ensure arbors and flanges are clean and undamaged.
3. Mount blade and tighten securely using wrench.
4. When wet cutting, check water jets far adequate flow.
5. Align pointer with cutter blade.
Caution - Set unit up in an open area. Avoid close proximity to structures or other equipment. Failure
to do so may cause inadvertent injury to operator or other persons in the area.
Cold start - Open the fuel valve under the gas tank all the way. Position the engine stop switch,
located on the engine, to run. Open the thrattle appraximately half way and apply the choke. Pull the
starter rape sharply. When the engine starts, open the choke and adjust the thrattle as necessary to
keep it running. Allow the engine to warm up far a few minutes befare placing it under the load. lf the
engine doesn't start after (3) pulls, open choke slightly to prevent flooding. Always operate the engine
at full thrattle when under load.
Hot Start - Open the valve under the gas tank all the way if it has been shut off. Open the thrattle
appraximately half way. Do not apply the choke. Pull the starter rape sharply until the engine starts.
When the engine starts, adjust the thrattle. Always operate the engine at full thrattle when under load.
NOTE: These starting instructions are general guidelines only. Since many engine options are availa-
ble, consult the Engine Manual included with this unit far specific instructions.
Caution - Gasoline Engines - To improve the engine service life, allow the engine to idle without load
for (2) to (5) minutes before shutting it down. When the idling period is up, use the stop switch loca-
ted on the engine and turn it to stop. Close the fuel valve under the gas tank. Engine flooding can
occur if the valve is left open during transport.
TO START CUTTING
1. Start engine and let engine warm up. AII cutting is done at full thrattle.
2. Align blade and saw with cut. lf wet cutting, open water valve and turn water safety switch on.
3. Step on the left side of PEDAL until hear a "click", then turn on the WHEEL HANDLE on the top of
the machine to remove the equipment farward and reverse, step down the right side of PEDAL to
change to "push" driving system.
4. Lower blade into cut slowly.
5. Cut as fast as blade will allow. lf blade climbs out of cut, reduce farward speed or depth of cut.
6. Use only enough side pressure on saw handles to fallow cutting line.
Cutting/Belts & Pulleys
CUTTING
Lower the blade into concrete to required depth by turning the tilt crank counterclockwise. Ease the
saw slowly forward. Slow forward pressure if the saw begins to stall.
Note: For deeper cuts (4 inches/102mm or more), several cuts should be made in incremental steps
of 1-1/2 inch (38mm) to 2 inches (51 mm) until the desired depth is reached.
Push the saw steadily forward using the front pointer as a guide. Exert enough forward pressure so
that the engine/motor begins to labor, but does not slow down. lf the saw begins to stall, retard
forward movement until full RPM is restored to the blade. lf saw stalls, raise the blade out of the cut
befare restarting. Avoid excessive side pressure or twisting of the blade in the cut.
BELTS & PULLEYS
NEVER MAKE ADJUSTMENTS TO V-BELTS AND PULLEYS WHILE ENGINE IS RUNNING.
1. The best tension for a v-belt drive is the lowest tension at which the belts will not slip under full load.
2. Take up tension until the belts are snug in the grooves. Run the drive for about five (5) minutes to
"seat" the belts. The impose the peak load. lf the belts slip, tighten them until they no longer slip at
peak load. Most new belts will need additional tensioning after seating.
3. Remember, too much tension shortens belt and bearing life.
4. Check the belt tension frequently during the first day of operation. Check the belt tension periodi-
cally thereafter and make any necessary adjustments.
5. The two most common causes of sheave misalignment are:
a) The engine drive shaft and the blade shaft are not parallel.
b) The pulleys are not located properly on the shafts.
6. To check alignment, use a steel straight edge. See Figure 1.
7. Line up the straight edge along the outside tace of both pulleys shown in the drawing. AII pulleys
have (2) set screws in the bottom of their grooves. Set screws require thread locking lock title.
8. Misalignment will show up as a gap between the pulley tace and straight edge. Make sure there is
clearance between arbor pulley and saw base on both sides.
DRY CUTTING
• Never operate any saw without safety guards in place.
• Do not exceed maximum operating speed established for blade diameter.
• Do not force blade into material: allow blade to cut at its own speed.
• Do not make long continuous cuts. Never dry cut for more than 30 seconds at a time. Allow blade
to cool.
• Do not cut or grind with side of blade or cut a curve or radius. Do not cut dry with blades recom-
mended for wet cutting.
• Do not operate saw with blade diameter larger than machine's capacity.
3. MAINTAINENACE - TROUBLESHOOTING
PROBLEM
CAUSE REMEDY
UNEVEN SEGMENT • (In wet cutting) lnsufficient
• Flush water system.
WEAR
water (usually on one side of blade).
• Check flow to both sides of blade.
• Equipment defects also can
• Replace bad bearings, worn arbor
cause the segments to wear unevenly. shaft or misalignment to spindle.
• Saw head is misaligned.
• Check alignment far squareness,
both
vertically
and
horizontally,
of
the
saw
blade.
SEGMENT CRACKS • Blade is too hard far material being cut. • Use a blade with a softer
bond/matrix.
SEGMENT LOSS
• Blade overheats because
• (Wet Cutting) Check water lines.
of lack of coolant (water or air).
• Make sure flow is adequate on
• Core is worn from undercutting.
both sides of blade and there are
• Detective collars/flanges set
no blockages
blade out of alignment.
• Use sufficient water to flush
• Blade is too hard far material
out the cut.
being cut.
• (Dry Cutting) Run blade free of cut
• Blade is cutting out of round,
periodically to air cool.
causing a pounding motion.
• Clean collars/flanges or replace if
• lmproper blade tension.
they are under recommended
diameter.
•
Use
proper
blade
specification
far
material
being
cut.
•
Replace
worn
bearings;
realign
blade shaft or replace worn blade
mounting
arbor.
•
When
ordering
blades
match
shaft
speed
of
saw.
•
Check
spindle
speed
to
ensure
blade
is
running
at
correct
RPM.
•
Avoid
twisting
or
turning
blade
in
the
cut.
CRACKS IN CORE • Blade flutters in cut as a result
• Tighten the blade shaft nut.
of losing blade tension.
• Make sure blade is running at
• Blade specification is too hard
proper speed and that drive pin is
far the material being cut.
functioning properly.
•
Use
a
softer
bond/matrix
to
elimi
nate
stress.
LOSS OF TENSION • Core overheating.
• Make certain blade RPM is correct.
• Core overheating as a result
• Check water flow, distribution and
of blade spinning on arbor.
lines.
• Core overheating from rubbing
• Tighten the blade shaft nut. Make
the material being cut.
certain the drive pin is functioning.
• Unequal pressure at blade
• Properly align the saw to square cut.
clamping
collars/flanges.
• Collars/flanges must be identical in
• Blade is too hard far the material
diameter and the recommended size.
being cut.
• Use a softer bond/matrix to reduce
stress.
BLADE WOBBLES • Blade is on a damaged or
• Check far bad bearings, bent shaft,
worn saw.
or worn mounting arbor.
•
Worn
collar.
• Check collars/flanges to make sure
• Blade runs at an incorrect speed.
they are clean , flat and of correct
• Collar/flange diameters are not
diameter.
identical.
• Set engine at proper RPM
• Blade is bent as a result of
• Use proper size blade
dropping or twisting.
collars/flanges.
• DO NOT use bent blade.
Contact
blade
manufacturer.
BLADE WILL NOT CUT
• Blade is too hard far material
• Select proper blade far material
being cut.
being cut.
• Blade has become dull.
• Sharpen by cutting on softer
• Blade does not cut material
abrasive material to expose
it was specified far.
diamonds. lf continually
sharpening, the blade is too hard
far
the
material
being
cut.
•
Break-in
on
the
material
to
be
cut.
lf it does not dress itself, sharpen
as
you
would
a
dull
blade.
UNDERCUTTING
• Abrasive wearing of the core
• Use water to flush out fines
THE CORE
faster than the segments.
generated during cutting
• Use wear-restardant cores.
ARBOR HOLE
• Collars/flanges are not properly • Make certain the blade is mounted
OUT-OF-ROUND
tightened, permitting blade to
on the proper shaft diameter.
rotate or vibrate on the shaft.
Tighten the shaft nut with a wrench
• Collars/flanges are worn or dirty. to make certain that the blade is
Blade is not properly mounted. secure.
•
Clean
collars/flanges,
make
sure
they
are
not
worn.
Tighten
arbor
nut.
•
Make
sure
the
pin
hale
slides
over
drive
pin.
BLADE WORN OUT
• Shaft bearings are worn.
• lnstall new blade shaft bearings or
OF ROUND
• Surges occur because engine
blade shaft, as required.
is not properly tuned.
• Tune engine according to
• Blade arbor hale is damaged
manufacturer's manual.
from incorrectly mounting
• lf core is worn or arbor hale dama
the blade.
ged, DO NOT USE. Contact blade
• Bond/matrix is too hard far
manufacturer.
material.
• Replace worn shaft or mounting
• Blade si slipping, wearing one
arbor bushing.
half of blade more than other.
• Make certain that drive pin is
functioning.
•
Tighten
spindle
nut.
4. LUBRICATION AND SERVICE
• Check oil levels, wiring, hoses (air, fuel, water) and lubricate machine daily.
• Repair or replace all worn or damaged components immediately.
• Check drive belt tension, do not over-tension.
• Make sure machine has full set of matched belts.
• Check blade shaft, make sure arbor and threads are not worn, damaged, or bent.
• Blade shaft bearings should be tight, no free play side-to-side or up and down.
• Grease blade shaft bearings daily.
• Blade collars should be clean, free of nicks and burrs. No diameter wear and not out of round.
• Drive pin not excessively worn or bent and free of gouges.
• AII guards in place and secure. AII fasteners tight and secure.
• Air filter/ oil filter (hydraulic or engine) clean.
• Flush clean water thraugh the pump and spray the assembly every night. This pralongs the pump
and blade life.
• Clean machine befare starting lubrication maintenance.
• lnsure machine is on salid, level graund befare starting maintenance.
• During lubrication maintenance insure strict cleanliness is observed at all times.
• To avoid the risk of accidents, use the correct tool far the job and keep tools clean.
• The draining of engine oil is best carried out when the oil is warm NOT hot.
• Any spilled oil must be cleaned up immediately.
• Use only clean containers far oil and only CLEAN, FRESH oils and grease of correct grade.
• Contaminated Water/Fluids/ Oils/Filters must Be Disposed of Safely.
5. SPECIFICATION
DATMF16-2
Fuel:
Diesel
Max. output:
9 hp
Max. cutting depth:
14 cm
Blade size:
30-40 cm
Depth adjustment:
Handle rotation
Driving:
Manual push
Water tank capacity:
35 L
Dimensions:
107x55x104 cm
Net Weight:
169 kg
Gross Weight:
175 kg
DATMF16-4
Fuel:
Gasoline
Max. output:
13 hp
Max. cutting depth:
14 cm
Blade size:
30-40 cm
Depth adjustment:
Handle rotation
Driving:
Manual push
Water tank capacity:
35 L
Dimensions:
107x55x104 cm
Net Weight:
146 kg
Gross Weight:
155 kg
DATMF20-2
Fuel:
Diesel
Max. output:
9 hp
Max. cutting depth:
17 cm
Blade size:
35-50 cm
Depth adjustment:
Handle rotation
Driving:
Semi-self propelled
Water tank capacity:
40 L
Dimensions:
115x55x100 cm
Net Weight:
216 kg
Gross Weight:
220 kg
DATMF20-4
Fuel:
Gasoline
Max. output:
13 hp
Max. cutting depth:
17 cm
Blade size:
30-50 cm
Depth adjustment:
Handle rotation
Driving:
Semi-self propelled
Water tank capacity:
40 L
Dimensions:
115x55x100 cm
Net Weight:
193 kg
Gross Weight:
202 kg
6. TRANSPORTATION
l. Always shut off engine when transporting machine.
2. Make sure lifting device has enough capacity to hold machine (see identification plate on machine
for weight).
3. Use lifting point when lifting machine.
4. Trolley wheel as optional is used for short distance transportation.