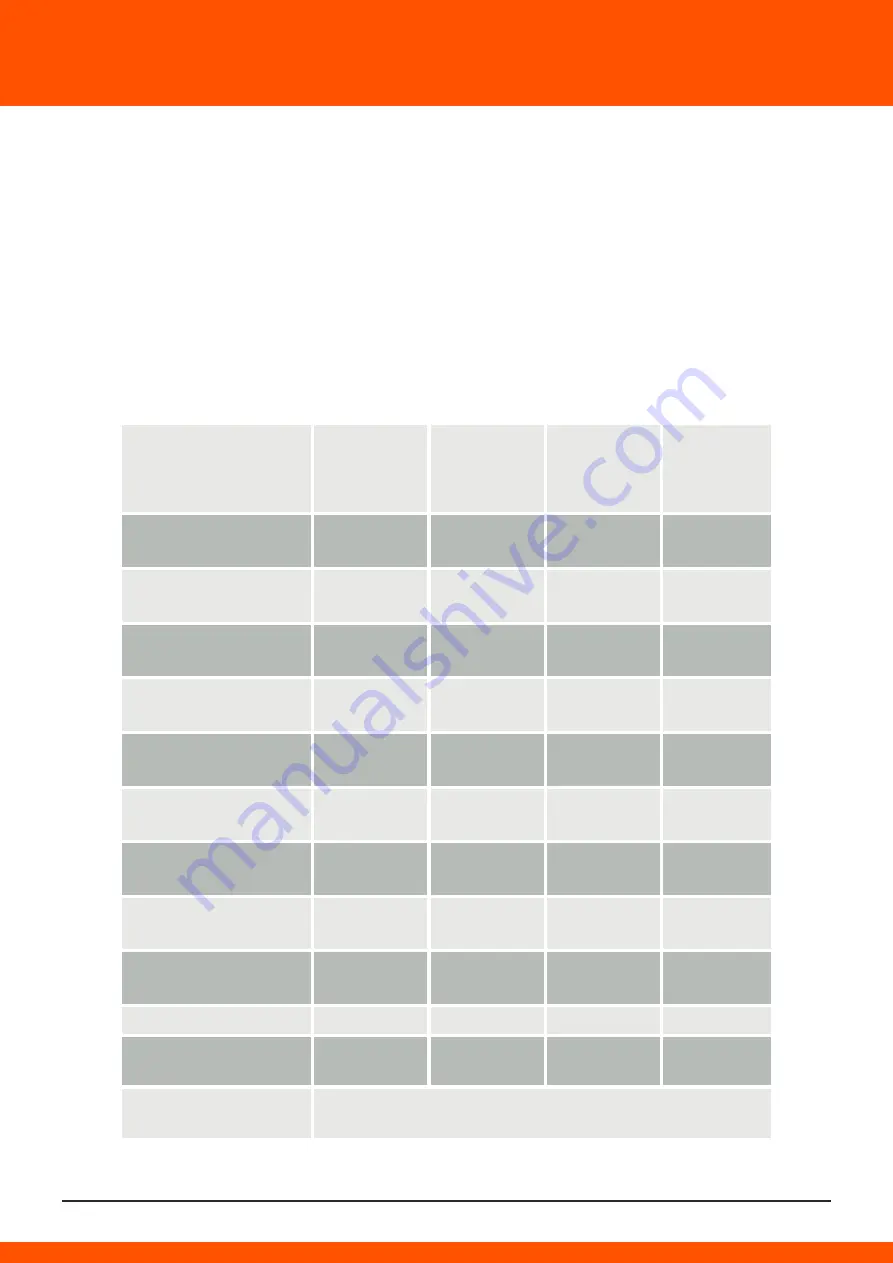
2
1. INTRODUCTION
The alternating current arc welder is designed and manufactured by our company, and has many
advantageous features: use of national techniques, innovative style, maneuverable size, and an
excellent performance.
The machine is made with automatic temperature control, and a cooling wind device to ensure an
efficient and safe work in the long term. It adopts the design of moving coil, with the use of the 220V,
60Hz alternating current.
It’s easy to use, and belongs to the portable products in domestic market.
Its quality is stable and reliable, with a good performance against all odds in the welding. It can use
only one phase of power supply, specially suitable for mobile operating service.
2. SPECIFICATIONS
3. PARTS IDENTIFICATION DIAGRAM
1.WHEEL
2.INFIX SUPPORT
3.BENCH SURFACE? (VENTILATION HOLES)
4.TORCH CONNECTION
5.TOOL CONTACTS
6.REGULATING WHEEL
7.TEMPERATURE INDICATOR
8.ON/OFF SWITCH
9.HAND BAR (YOU MUST TURN THE KNOB SELECTING 110V OR 220V)
10.HANDLE
11.BLOCKING VOLTAGE
4. EXPOSITION SCHEME
5. PLACEMENT AND CONECTION
Placement of the welder
1. Please, set the welder in lower vibration and place it in a plain surface, more than 20cm far from the
wall.
2. Please, put it in a dry and clean place, with no iron powder, dust or paint.
3. Avoid placing it in the rain or in sites eroded by the sea water.
Connection
1. Ground
a. There’s a land terminal on the commands board. Please, connect it to the ground with a more than
14mm wide copper wire.
b. Please, be aware that arrangements and ground connections must be made by an expert or a
qualified electrician.
2. Net connections:
Every welder needs to be equipped with a distribution box with a switch and an over-current protec-
tion device. Please, sent the electric power from the distribution box to the terminal income key of the
welder with a cable. The distribution box capacity and the transversal section area of the cable are
referred in the table.
*The overhead cable has copper coil.
3.The welding torch connections:
One end is adjacent to the cable for the welding torch through a quick connection, and the other end
is coupled to the work piece using a terminal with a quick joint.
The rapid joint at the end of output should be screwed firmly to the right for safety.
WARNING:
1.Turn off the power distribution box when connecting the cable.
2.The cables must be connected with the copper terminal. Please, use isolating tape after the fixtion
with screw and nut.
6. OPERATING INSTRUCTIONS
You must operate it in the following way:
1. Turn on the power distributer box 220V~ 50HZ.
2. Turn the power switch of the welder.
3. Select the welding current.
Turn the hand wheel clockwise to increase the power.
Turn the hand wheel against the clockwise to decrease the power.
4. Operate the welder
Use adeccuate clothes and protection accessories
5. Finish the operation.
6. Unplug the power supply of the welder.
7. Turn off the power distribution box.
7. SAFETY INSTRUCTIONS
Read this manual carefully before using the welder, in order to avoid accidents. The incorrect opera-
tion of the tool can cause injuries in three different degrees. The signs are indicated in this manual.
Warning: malfunction will lead to serious injury or death.
Be careful: incorrect operation could result in serious injury or potential accidents.
Attention: misuse may cause medium grade injuries or destruction of the machine.
Severe injuries refer to those that need long term treatment in a hospital caused by visible damage,
wounds (high temperature or low temperature), electric shock injury, broken bones, intoxication, and
so on; and minor injuries means an electric shock or burns without long-term cure
The destruction of the machine indicates the loss of the adeccuate shape or its total breakage.
DANGER!: In order to prevent serious bodily injury from accidents, you should carefully observe the
following:
1. The construction of the power supply, the selection of the site to place the machine, the maintenan-
ce of the work piece after welding, and waste management, must be done according to internal rules
and standards of your company.
2. Prohibit the entrance to the welding-site of irrelevant or unauthorized people.
3. People with pacemakers can not approach to the welder in use or surround the welding site without
a doctor’s permission.
4. Let a professional or expert to install, maintain or repair the welder.
5. Leave the operation of the machine to personnel with technical skills and safety knowledge.
6. Use the machine only to weld.
DANGER!: In order to avoid to suffer an electric shock, please, follow the next rules. Once you touch
electrical parts, it may cause a lethal electric shock or burns, so:
1. Do not touch electric parts
2. Let a qualified electrician to do the machine’s land connections according to the regulations.
3. For installation and repair, switch off the power distribution box, and operate in five minutes.
4. Do not use the cable with insulating protective cover damaged and exposed conductor.
5. Ensure the cable insulation.
6. Please, dont use the machine without the proper safety helmet.
7.Please, use dry insulating gloves.
8. Please use a safety net when working in high places.
9. Regularly maintain and repair it, and use it after it’s repaired.
10. Please turn off all input switches.
11. Please use a shockproof device when the machine is used in narrow or high places.
WARNING: In order to prevent accidents such as fires, explosions, etc., please obey the following
rules:
1. Do not put flammable things in the place where you will weld.
2. Do not weld near inflammable gas.
3. Do not leave the hot machine near flammable material.
4. The parts of cable splicing must be fully insulated.
5. When welding the floor and the wall, please remove the flammable material in the back.
6. The cable joint with the tool contact side of the machine must be aproched to what you are welding.
7. Do not weld gas pipes, sealed containers and others alike.
8. Please place fire extinguisher near the welding site.
WARNING: The entrance into the interior of the machine, of iron splash and dust caused by welding
and polishing, will lead to the deterioration of the insulation.
In order to prevent fire caused by deterioration of electrical insulation, please obey the next rules:
1. Please, separate the welding machine from the welding and polishing operations.
2. Please, maintain and repair regularly to prevent damage to the isolation caused by the accumula-
tion of dust.
3. When you splash iron powder in the interior of the machine, please turn off the power of the welder
and the distribution box, then clean by air blow.
8. CONSERVATION AND MANTEINANCE
In order to prolong the life of the machine, please pay close attention to the maintenance and repair.
Please make at least once every six months the maintenance as shown in the following points.
The power distribution box and the welder must be off.
1. Use a resistance messure tool to know the resistance between the ground and the primary winding,
secondary, and / or any other winding. Resistance must be greater than 1M.
2. Dust can reduce the isolation performance and reheating the winding too much. Therefore, it is
necessary to use compressed air to blow the dust off the coil and other parts.
3. Examine the state of the power switch contact. If it’s burned on the surface, it must be changed.
4. Examine whether the screw and the nut are tightened. If they are loose, it is necessary to screw
them better.
5. Once the machine needs to be repaired, please inform the distributor the model number and the
product as soon as possible.
WARNING:
1. Please, confirm the class specifications and then use them.
2. Avoid the excess of use load.
a. An excessive overload can burn the machine and shorten its life.
b. Overloading can cause noise and make it difficult to rotate the wheel.
3. The connection of the cable and the terminal of the machine must be stable, or you can burn both.
4. An output cable too long will lead to an impairment of current circulation and loss of electric power.
If the insulation of the cable surface is in bad shape, the arch will be unstable. So you must change
the old cable.
5. The power must be turned off after operation.
6. The movable inner core of iron and the structure should be adapted very well. Do not move unless
necessary.
7. Place the welder in the shade. Do not use the machine in the sun too long.
8. The cover’s temperature will rise in the operation. The coil insulation belongs to grade H.
9. Keep voltage as steady as possible.
If the voltage is lower than the nominal input voltage, it will result in:
(1) The welding current is too low.
(2) The arc will broke or turn unstable.
If tension is higher than that of the rated input voltage, it will result in:
(1) The welding current be too high.
(2) Make noise
(3) The current adjust the rotation of the wheel.
(4) Shorten the life of the welder.
10. Please remember to use suitable protective equipment in case of accident.
Model
Regulation
DAX1-160C1
DAX1-180C1
DAX1-200C1
DAX1-250C1
Rated output current
(
A
)
160
180
200
250
Rated input voltage
(
V
)
220 V±10%
Rated input voltage ( V )
50
50
60
50
60
50
60
Rated input capacity (KW
)
6.5
7
7.5
10
Power load without
tension (V)
48
48
48
48
Rated duty cycle
(
%
)
10
10
10
10
Electric load with
voltage
(
V
)
26.4
27.2
28
30
Current range
(
A
)
55-160
60-180
Appropriate welding rod
diameter (MM
)
2.0-4.0
2.0-4.0
2.0-4.0
2.0-5.0
Weight
(
KG
)
19.7
20.5
21.2
21.5
Isolation degree
H
H
H
H
External size (MM
)
500*300*435
220 V ± 10%
110 V ± 10%
220 V ± 10%
110 V ± 10%
220 V ± 10%
110 V ± 10%
80-200
85-250
Summary of Contents for DAX1-160C1
Page 6: ...5...