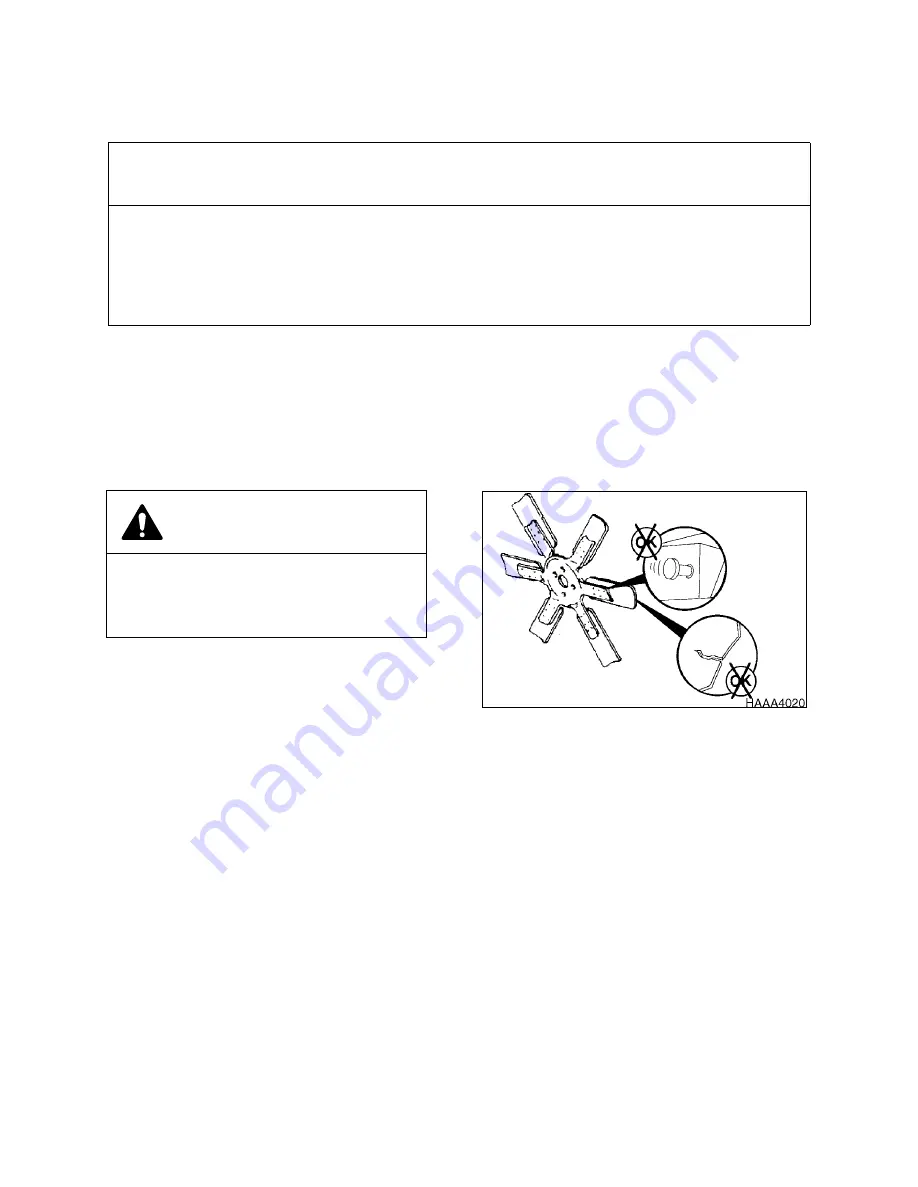
4-18 Inspection, Maintenance and Adjustment
K1000896E Operation and Maintenance Manual
START ENGINE, CHECK STARTING ABILITY, AND OBSERVE EXHAUST COLOR AT START-UP
AND AT NORMAL OPERATING TEMPERATURE. LISTEN FOR ANY ABNORMAL SOUNDS
CHECK OPERATION OF ALL CONTROLS
1.
With engine at rated speed, operate all of the controls.
2.
Follow cold weather hydraulic system warm-up procedures.
3.
Note any slow operations or unusual movements. Determine the cause and repair fault before
operating.
INSPECT ENGINE FAN BLADE
NOTE:
Manually rotate the crankshaft
by using a wrench on the
accessory drive pulley nut.
1.
An inspection of the cooling fan is required
daily. check for cracks, loose rivets, bent or
loose blades, and for contact between the
blade tips and the fan shroud. Check the
fan to make sure it is securely mounted.
Tighten the bolts if necessary. Replace
any fan that is damage.
IMPORTANT
Cold weather operation requires that the operator fully warm up the hydraulic oil before
beginning machine operation. Follow all warm up instructions listed in the Operating Instruction
section of this manual. Make sure to cycle oil through all of the components, including all
cylinders, both travel motors and the swing motor. Cold hydraulic oil in the lines and
components needs to be warmed before beginning full operation. If this is not done, damage to
the cylinders or hydraulic motors can occur.
WARNING!
Personal injury can result from a fan blade
failure. Never pull or pry on the fan. This
can damage the fan blade(s) and cause
fan failure.
Figure 23
Summary of Contents for Mega 250-V
Page 2: ......
Page 6: ......
Page 32: ......
Page 110: ......
Page 184: ......
Page 199: ...K1000896E Operation and Maintenance Manual Troubleshooting 6 13...
Page 200: ...6 14 Troubleshooting K1000896E Operation and Maintenance Manual...
Page 208: ......