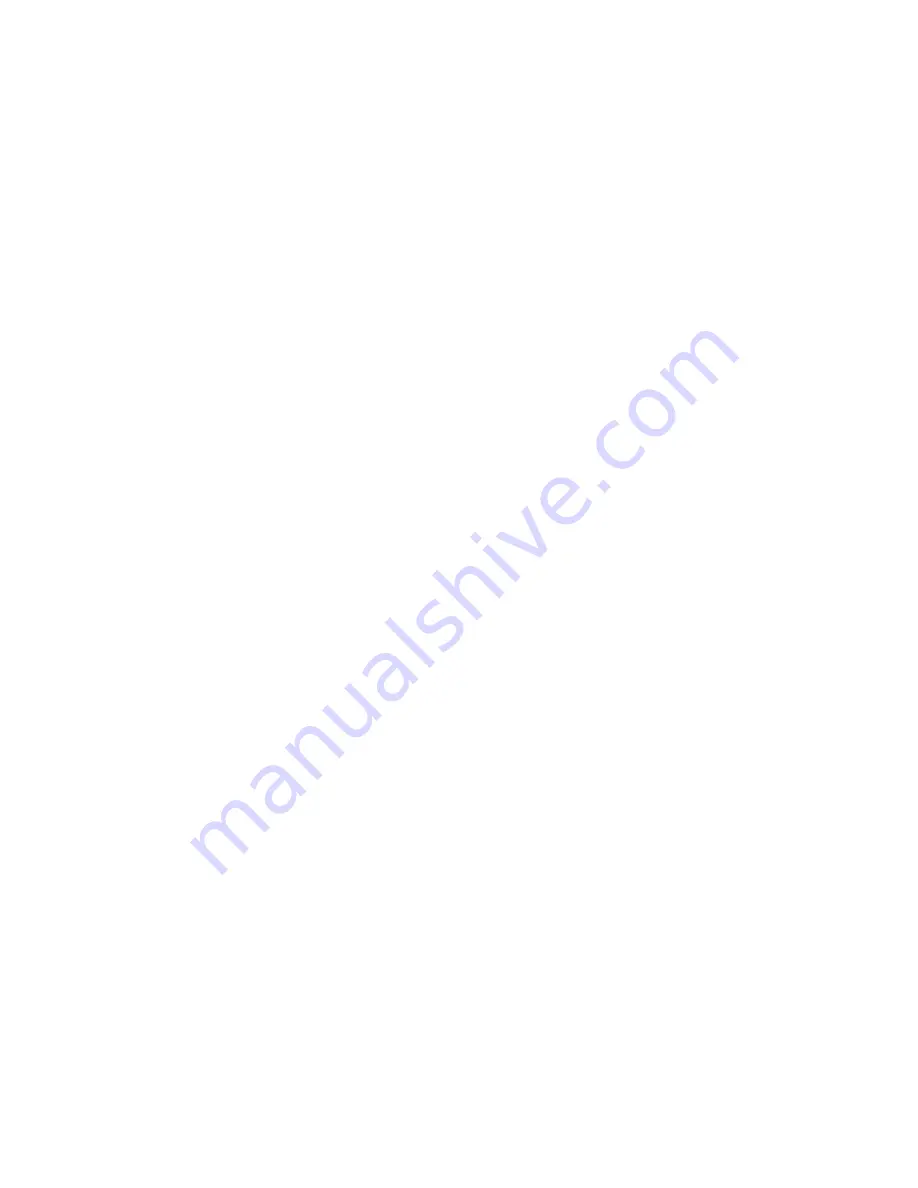
Page 8
General Maintenance Procedures
Return to Master Table of Contents
scratching. Curling under of any seal lip will seriously impair its efficiency. Apply a thin coat of Loctite
#120 to outer diameter, of metal casing, on oil seals to assure an oil tight fit into retainer. Use extreme
care not to get Loctite on lips of oil seals. If this happens, that portion of the seal will become brittle
and allow leakage.
When replacing lip type seals, make sure spring loaded side is towards oil to be sealed.
5.
If available, use magna-flux or similar process for checking for cracks that are not visible to the eye.
Examine teeth on a ll gears carefully for wear, pitting, chipping, nicks, cracks or scores. Replace all
gears showing cracks or spots where case hardening has worn through. Small nicks may be removed
with s uitable ho ne. Ins pect sh afts and qui lls to ma ke ce rtain they have n ot be en s prung, ben t, or
splines twisted, and that shafts are true.
NOTE:
Spline wear is no t c onsidered de trimental except w here it affects tightness o f s plined
parts.
Inspect thr ust washers for distortion, scores, burs, and wear. Replace thrust washer if defective or
worn.
6.
Inspect bores and bearing surfaces of cast parts and machined surfaces for scratches, wear, grooves
and dirt. Remove any scratches and burrs with crocus cloth. Remove foreign matter. Replace any
parts that are deeply grooved or scratched which would affect their operation.
BEARING INSPECTION
The conditions of the bearing are vital to the smooth and efficient operation of the machinery. When any
component containing bearings is disassembled, always carefully examine the condition of the be arings
and all of its components for wear and damage.
Once the bearing is removed, clean all parts thoroughly using a suitable cleaning solution. If the bearing is
excessively dirty soak th e bearing a ssembly in a l ight solution an d move th e bearing a round u ntil all
lubricants and or foreign materials are dissolved and the parts are thoroughly clean.
When d rying be arings, m oisture fr ee c ompressed air c an b e us ed. Be c areful no t to di rect the air in a
direction which will force the bearing to dry spin while not being properly lubricated.
After the bearings have been cleaned and dried, carefully inspect all bearing rollers, cages and cups for
wear, c hipping or ni cks. If the bearing c an no t b e r emoved an d i s to be inspected in place, c heck foe
roughness of rotation, scoring, pitting, cracked or chipped races. If any of these defects are found replace
the whole bearing assembly. NEVER replace the bearing alone without replacing the ma ting cup or the
cone at the same time.
After inspection lightly coat the bearing and related parts with oil and wrap in a clean lintless cloth or paper
and protect them from moisture and other foreign materials until installation.
It is also important to inspect the bearing housing and/or shaft for grooved, galled or burred conditions that
indicate that the bearing has been turning in its housing or on its shaft.
If available, use magna-flux or similar process for checking for cracks that are not visible to the naked eye.
The following illustrations will aid in identifying and diagnosing some of the bearing related problems.
NOTE:
The i llustrations wil l o nly s how tap ered r oller b earings, but the p rinciples o f id entifying,
diagnosing and remedying the defects are common to all styles and types of bearings.
Summary of Contents for Solar 200W-V
Page 1: ...Shop Manual 2023 7139E Serial Number 0001 and Up March 2000 Solar 200W V...
Page 3: ......
Page 6: ...Return to Master Table of Contents 1SAFETY...
Page 28: ...S0102020 Page 22 Wheel Excavator Safety Return to Master Table of Contents...
Page 29: ...Return to Master Table of Contents 1SPECIFICATIONS...
Page 30: ...Return to Master Table of Contents...
Page 37: ...S0202040 Page 7 Specifications for Solar 200W V Return to Master Table of Contents...
Page 57: ...Return to Master Table of Contents 1GENERAL MAINTENANCE...
Page 58: ...Return to Master Table of Contents...
Page 72: ...S0302000 Page 14 General Maintenance Procedures Return to Master Table of Contents...
Page 85: ...Return to Master Table of Contents 1UPPER STRUCTURE...