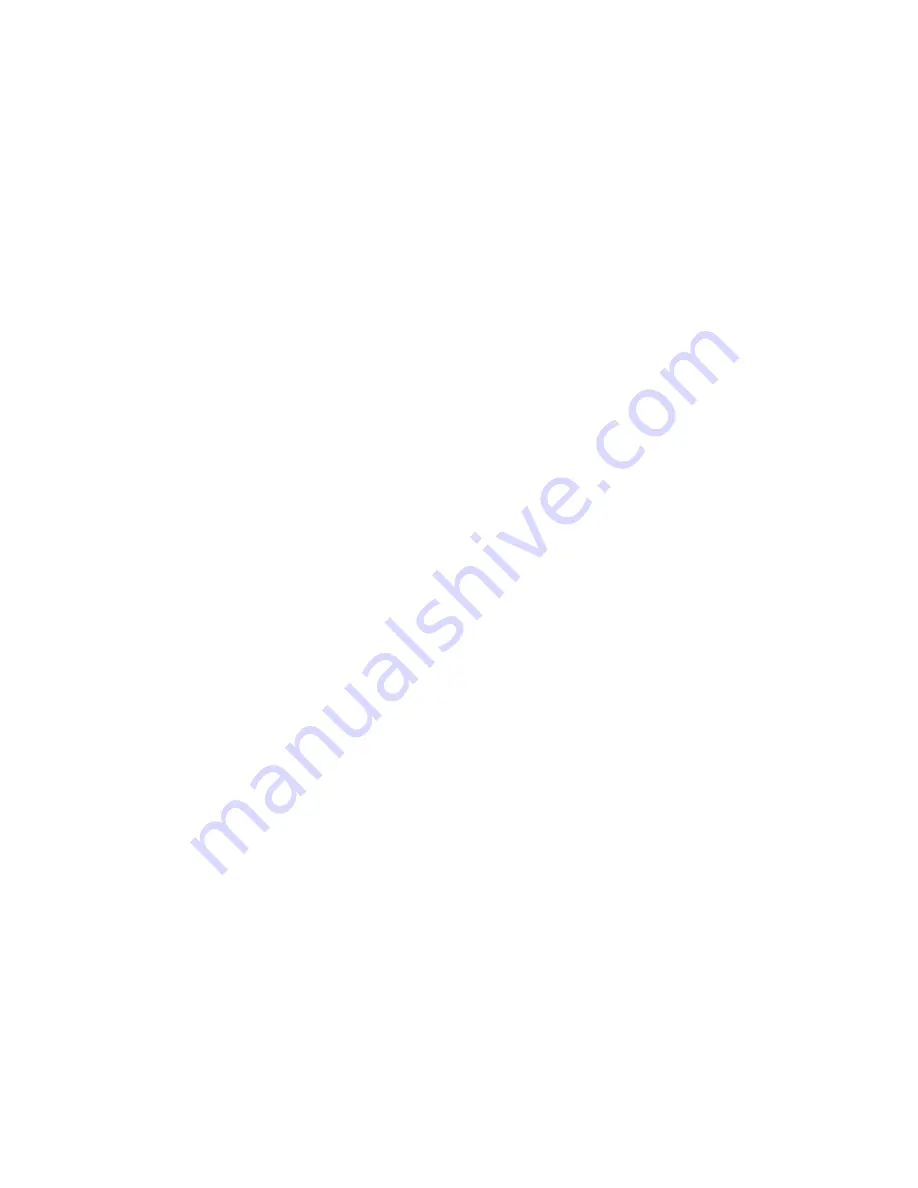
– 6 –
6.
Requirements
6.1 When mounting this torch onto a robot, connect a lead cable bundled with a power
cable to the connection part of the workpiece-side welding cable on the welding power
source.
6.2 If there is any loosened part in every connection of a torch, heating, a water leak or a
gas leak might occur. Make sure to tighten the connections sufficiently.
6.3 Keep a gas flow rate at 7 – 8 liter / min for AC and 5 – 6 liter / min for DC for normal
operations. When a gas lens is in use, sufficient shield effect will be obtained at a
lower rate. When it is windy, or a workpiece and a torch need to be moved farther
away from each other, raise the flow rate at the appropriate times.
6.4 Keep the flow rate of coolant at more than 1.2 liter / min. 1.2 – 1.5 kg / cm
2
is
appropriate for water pressure. DO NOT use with water pressure of more than 3 kg /
cm
2
. Lower than 25ºC is desirable for the temperature at the inlet.
6.5 Although a cable hose, a gas hose and a coolant hose are all protected by hose
sheaths, DO NOT put anything heavy on top, let them touch heated parts of the
welded, nor bent them by force.
6.6 Always keep a tungsten electrode clean.
1) When spatters stick to an electrode:
Generate arc on other steel plate, and it will be cleaned.
2) When the tip of an electrode makes a tiny spherical shape:
Sharpen the tip by a grinder and so on to form acute angles.
3) When an electrode sticks into the molted pool:
Turn off POWER, take out the electrode and break it at the lowermost part of the tip.
Then, fix the tip of the electrode with a grinder and so on.
6.7 Keep a nozzle clean as well. Remove its cap occasionally and check whether there
is any abnormality.
6.8 Even when an abnormality cannot be observed from outside, doing periodic inspection
to check out the wearing out of parts is desirable for maintaining a touch in a good
shape and obtaining fine results of welding.