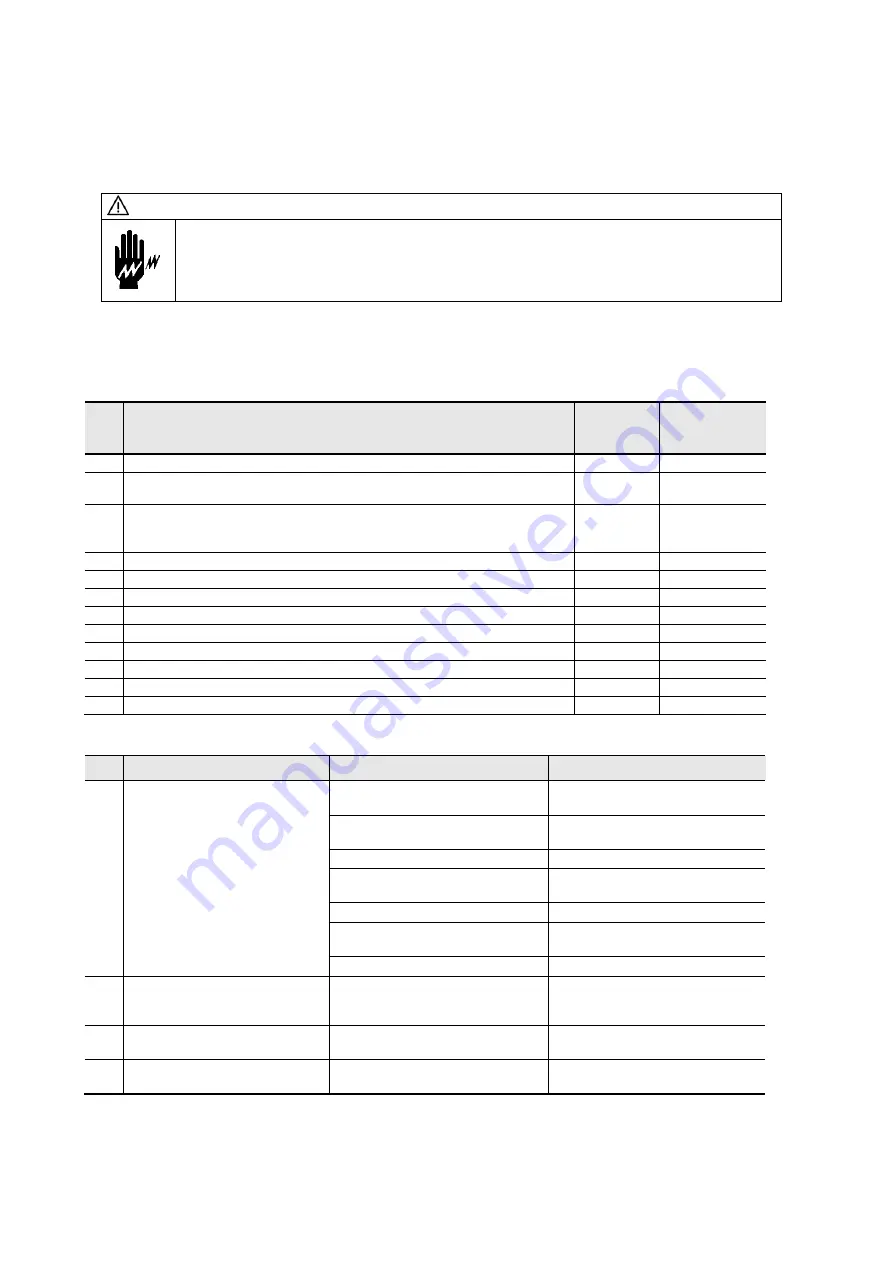
-
26
-
9 MAINTENANCE AND TROUBLESHOOTING
9.1 CARRYING OUT MAINTENANCE
WARNING
•
Do not touch live electrical parts inside or outside the wire feeder.
•
Disconnect the wire feeder from the welding power source by turning off the line
disconnect switch in the power box to avoid an electric shock before carrying the
equipment.
In order to use the wire feeder safely and efficiently, be sure to conduct periodical maintenance and
inspection. If flaw is found, ask for change or repair of the object part.
◯
: Necessary inspection item, −: Omissible inspection item
No.
Inspection item
Daily
inspection
Periodical
inspection in
3 to 6 months
1
Is there not abnormal vibration, buzz or odor?
◯
−
2
Are there not discoloration of terminal parts and melting and deterioration
of cable jackets?
◯
−
3
Are fastening screws not loosened or is contact not deteriorated by rust at
power cable connection part on the inlet side of wire feeder?
Is insulation not problematic?
◯
◯
4
Is there not portion of cable that is beginning to break?
◯
−
5
Is there not break in frames or covers or deformation?
◯
◯
6
Are covers and knobs fixed firmly? Are there no broken?
◯
◯
7
Is power cable, torch cable and gas hose connected firmly?
◯
◯
8
Is there not crack or break in parts and sheet metals inside wire feeder?
−
◯
9
Is there not portion of wiring inside wire feeder that is beginning to break?
−
◯
10 Is there no loosening of parts fixing?
−
◯
11 Is there no connecting part of connector that is beginning to come out?
−
◯
12 Remove dirt and dust inside wire feeder.
−
◯
Failure and countermeasures
No.
Phenomenon
Cause of failure/anomaly
Treatment
1
Wire is not fed.
Wire gets deformed.
Wire pressure is too weak.
Wire pressure is too strong.
Refer to “7.3. Adjusting of the wire
pressure and straightener”
Feed roll of wrong wire size is
used.
Replace it with the feed roll of
proper wire size.
Feed roll are worn.
Replace the feed roll, if necessary.
Poor contact or breakdown in the
control cable.
Confirm state of connection.
Confirm cables. Replace cables.
Trouble with the motor
Replace the motor, if necessary.
Dust or chip is accumulated on the
outlet guide and on the feed roll.
Remove the dust and chip.
Feeding roll bearing failure
Replace it, if necessary.
2
Shield gas supply does not
come out or does not stop.
Failure of gas solenoid valve.
Check for the operation of the gas
solenoid valve, and then replace it
if necessary.
3
Gas or water leakage from gas
or water hose.
There are defects such as cracks. Replace it, if necessary.
4
Wire is not fed smoothly through
the wire reel.
Adjustment of the brake is either
too strong or too weak.
Refer to “7.4. Adjusting of the wire
reel hub”.