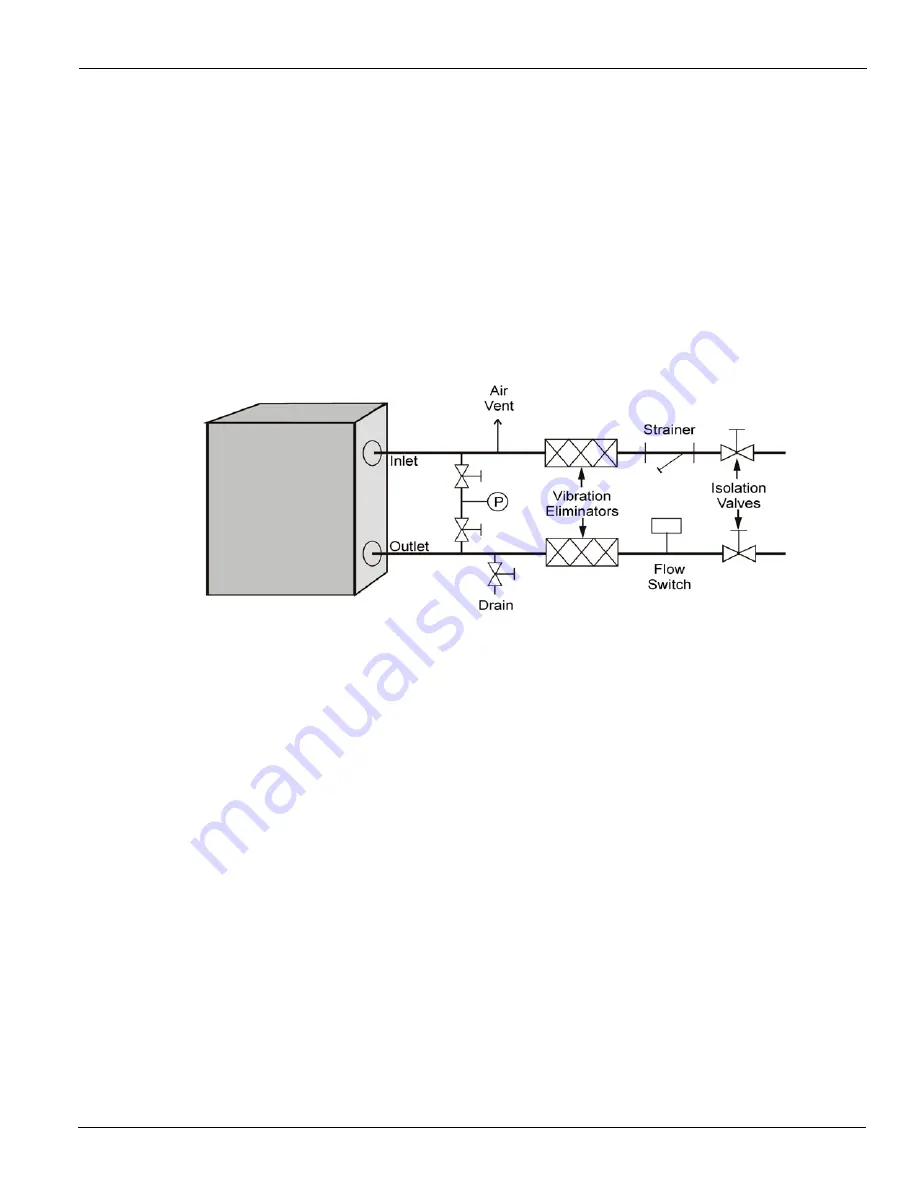
IOM 1206-1
7
Installation and Application Information
Water Flow Limitations
Constant Evaporator Flow
The evaporator flow rates and pressure drops shown on
page 18
are for full load design purposes. The maximum flow
rate and pressure drop are based on a 6°F temperature drop.
Avoid higher flow rates with lower temperature drops to
prevent potential control problems resulting from a very small
control band and limited start up/shut off temperature changes.
The minimum flow and pressure drop is based on a full load
evaporator temperature drop of 16°F. Evaporator flow rates
below the minimum values can result in laminar flow causing
freeze-up problems, scaling and poor control. Flow rates above
the maximum values will result in unacceptable pressure drops
and can cause excessive erosion, potentially leading to failure.
Variable Evaporator Flow
Reducing evaporator flow in proportion to load can reduce
system power consumption. The rate of flow change should be
a maximum of 10 percent of the flow per minute. For example,
if the maximum design flow is 200 gpm and it will be reduced
to a flow of 140 gpm, the change in flow is 60 gpm. Ten
percent of 200 gpm equals 20 gpm change per minute or a
minimum of three minutes to go from maximum to minimum.
Do not reduce flow lower than the minimum flows listed in the
evaporator pressure drop section,
page 18
. The water flow
through the evaporator must remain between the minimum and
maximum values listed. If flow drops below the minimum
allowable, large reductions in heat transfer can occur. If the
flow exceeds the maximum rate, excessive pressure drop and
tube erosion can occur.
Figure 7: Typical Piping, Brazed-Plate Evaporator (models AGZ030E-070E)
Install piping with minimum bends and changes in elevation to
minimize pressure drop. The following issues should be
considered when designing and installing water piping:
1
Vibration eliminators to reduce vibration and noise
transmission to the building.
2
Shutoff valves are required to isolate the unit from the
piping during unit servicing.
3
Manual or automatic air vent valves at the high points of
the system. Drains must be installed at the lowest points
in the system.
4
Adequate water pressure must be maintained (expansion
tank or regulating valve).
5
Temperature and pressure indicators located at the unit
are required to aid in unit servicing.
6
Chilled water piping and strainer must be supported
independently from the unit.
7
Flush the system water piping thoroughly before making
connections to the unit evaporator. Design the water
piping so the chilled water circulating pump discharges
into the evaporator inlet.
8
The unit's evaporator has a thermostat and heater to
prevent freeze-up down to -20 F ( 29 C). The heating
cable can be wired to a separate 115 V supply circuit. As
shipped from the factory, the heating cable is wired to the
control circuit. All water piping to the unit must also be
protected to prevent freezing.
9
If the unit is used as a replacement chiller, flush the
system thoroughly before unit installation. Regular water
analysis and chemical water treatment for the evaporator
loop is recommended immediately at equipment start-up.
10
The total water volume in the system should be sufficient
to prevent frequent "on-off" cycling. Turnover rate
should not be less than 4 minutes for normal variable
cooling loads.
11
When glycol is added to the water system for freeze
protection, the refrigerant suction pressure will be lower,
cooling performance less, and water side pressure drop
greater. If the percentage of glycol is high, or if
propylene is used instead of ethylene glycol, the added
pressure drop and loss of performance could be
substantial. When Glycol or Ice are selected as Unit
Mode, the MicroTech III control will automatically reset
the available range for the Leaving Water Temperature,
Freezestat and Evaporator Pressure settings.
12
Reset the freezestat setting to 6 degrees F (3.3 degrees C)
below the leaving chilled water setpoint temperature
after the glycol percentage is verified safe for the
application. See the section titled "Glycol Solutions" on
page 9
for additional information concerning glycol.