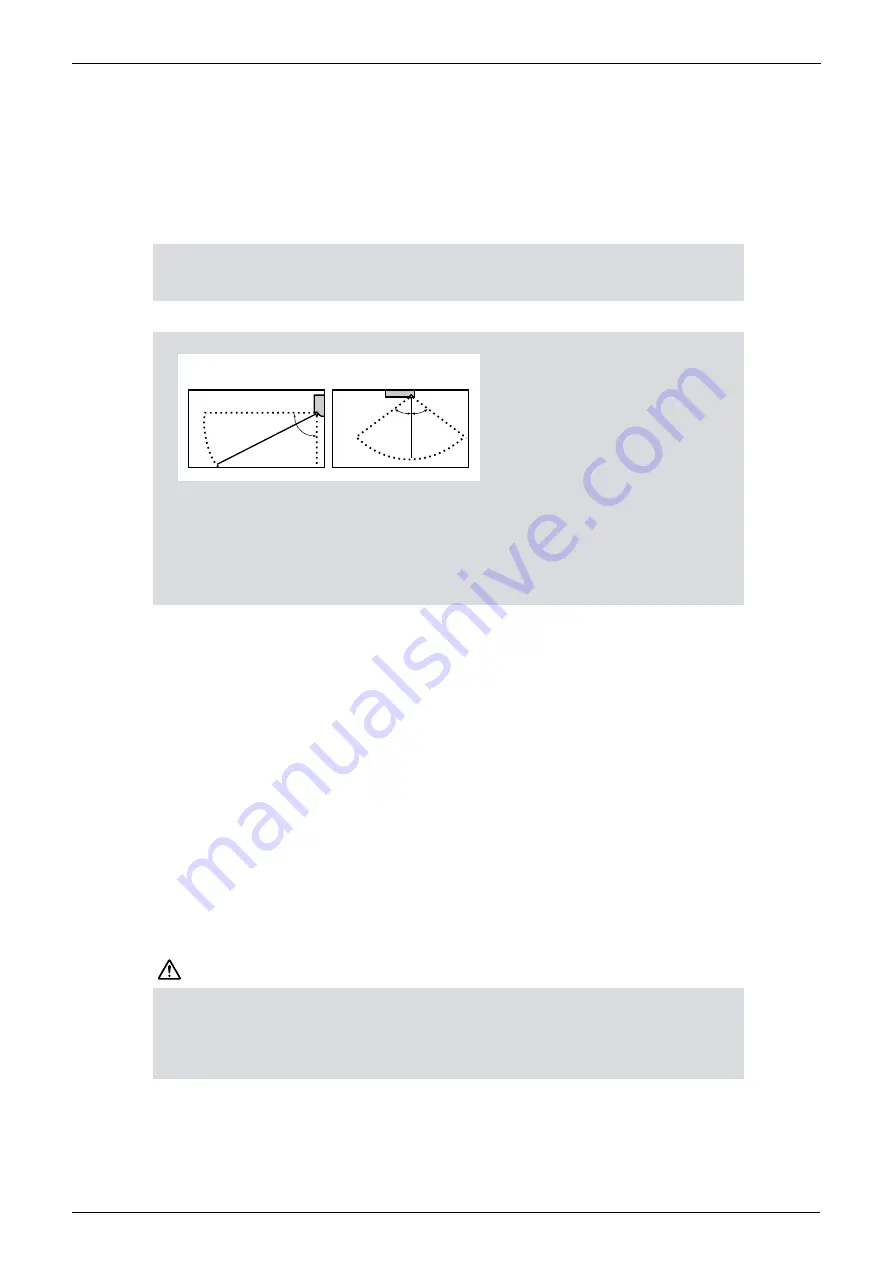
Instruction
Si12-714
142
Operation Manual
“INTELLIGENT EYE” is useful for Energy Saving.
Notes on “INTELLIGENT EYE”
CAUTION
Energy saving operation
• Change the temperature –2
°
C in heating / +2
°
C in cooling / +1
°
C in dry mode from set temperature.
• Decrease the air flow rate slightly in fan operation. (In FAN mode only)
• Application range is as follows.
• Sensor may not detect moving objects further than 7m away. (Check the application range)
• Sensor detection sensitivity changes according to indoor unit location, the speed of
passersby, temperature range, etc.
• The sensor also mistakenly detects pets, sunlight, fluttering curtains and light reflected off of
mirrors as passersby.
• INTELLIGENT EYE operation will not go on during powerful operation.
• Night set mode will not go on during you use INTELLIGENT EYE operation.
• Do not place large objects near the sensor.
Also keep heating units or humidifiers outside the sensor’s detection area. This sensor can
detect objects it shouldn’t as well as not detect objects it should.
• Do not hit or violently push the INTELLIGENT EYE sensor. This can lead to damage and
malfunction.
90˚
55˚
7m
55˚
7m
Vertical angle 90˚
(Side View)
Horizontal angle 110˚
(Top View)