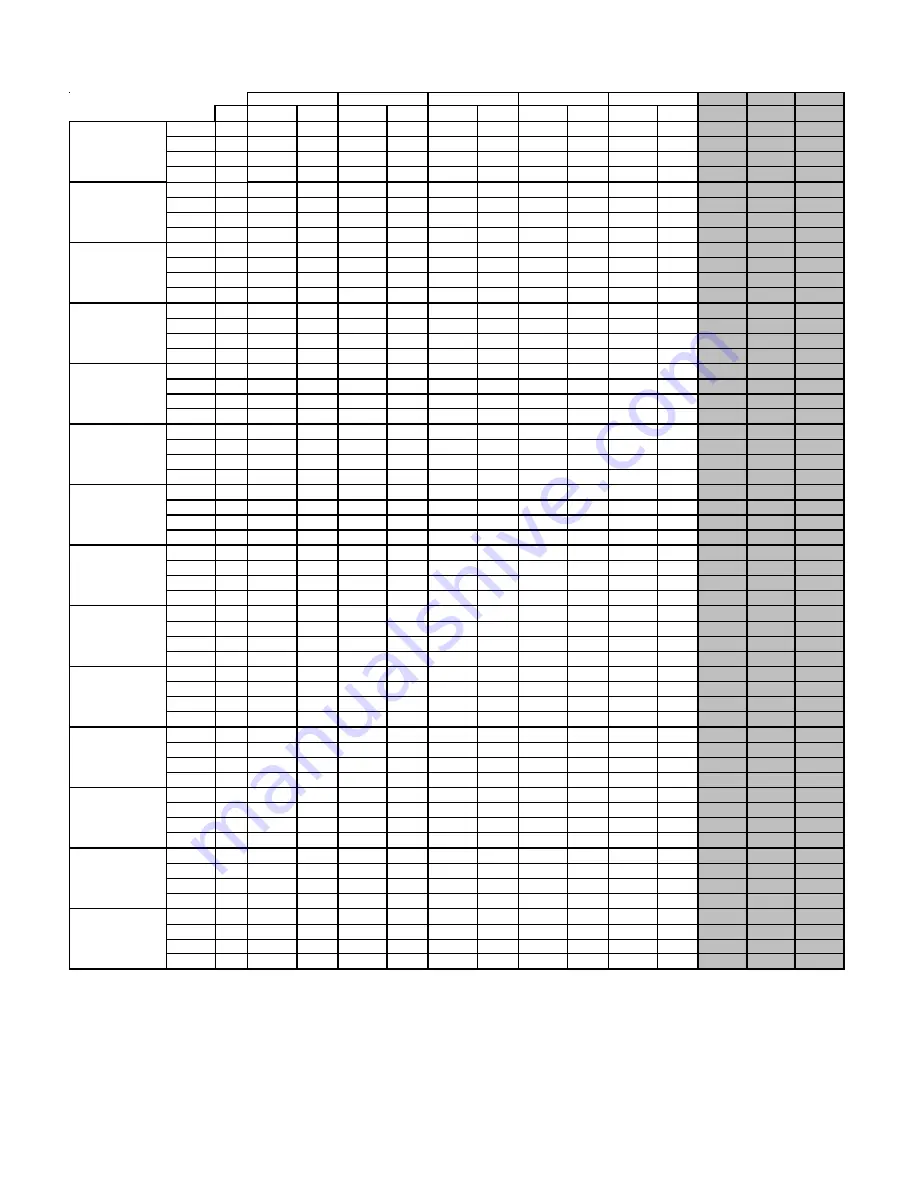
41
AIRFLOW
1.
CFM in chart is without filter(s). Filters do not ship with this furnace, but must
be provided by the installer. If the furnace requires two return filters, this
chart assumes both filters are installed.
2.
All furnaces ship as high speed cooling and medium-speed heating. Installer
must adjust blower cooling & heating speed as needed.
3.
For most jobs, about 400 CFM per ton when cooling is desirable.
4.
INSTALLATION IS TO BE ADJUSTED TO OBTAIN TEMPERATURE RISE WITHIN THE
RANGE SPECIFIED ON THE RATING PLATE.
0.6
0.7
0.8
AC
CFM
RISE
CFM
RISE
CFM
RISE
CFM
RISE
CFM
RISE
CFM
CFM
CFM
HIGH
3.0
1260
N/A
1205
N/A
1153
N/A
1081
31
1023
33
946
871
790
MED
2.5
1156
N/A
1115
N/A
1074
31
1019
33
959
35
893
817
742
MED-LO
2.0
1028
33
993
34
959
35
915
36
866
39
810
742
671
LOW
1.5
938
36
903
37
873
38
834
40
791
42
746
672
597
HIGH
3.0
1545
N/A
1495
N/A
1438
N/A
1369
N/A
1295
N/A
1212
1141
1034
MED
2.5
1322
N/A
1290
N/A
1246
N/A
1209
N/A
1149
30
1078
1013
921
MED-LO
2.0
1099
31
1077
32
1048
33
1019
33
985
35
928
859
772
LOW
1.5
976
35
969
35
923
37
896
38
858
40
817
763
683
HIGH
3.0
1543
N/A
1484
N/A
1427
36
1363
37
1296
39
1209
1122
1020
MED
2.5
1344
38
1315
39
1274
40
1223
42
1172
44
1097
1024
920
MED-LO
2.0
1138
45
1108
46
1083
47
1046
49
1008
51
956
876
791
LOW
1.5
1002
51
987
52
962
N/A
929
N/A
899
N/A
847
796
716
HIGH
3.0
1560
44
1505
45
1426
48
1366
50
1288
53
1194
1116
1006
MED
2.5
1362
50
1313
52
1275
53
1225
56
1166
58
1097
1009
912
MED-LO
2.0
1138
60
1116
61
1099
62
1053
65
1005
N/A
948
876
779
LOW
1.5
1010
N/A
1004
N/A
966
N/A
944
N/A
900
N/A
851
783
690
HIGH
5.0
2053
N/A
1994
N/A
1921
35
1827
37
1720
40
1614
1501
1344
MED
4.0
1858
37
1811
38
1749
39
1676
41
1589
43
1500
1397
1264
MED-LO
3.5
1538
44
1516
45
1494
46
1459
47
1400
49
1335
1239
1129
LOW
3.0
1256
54
1244
55
1216
56
1206
57
1170
58
1113
1063
987
HIGH
5.0
2256
30
2172
31
2107
32
2058
33
1959
35
1859
1762
1654
MED
4.0
1980
34
1923
35
1882
36
1808
38
1722
40
1633
1559
1454
MED-LO
3.5
1630
42
1593
43
1561
47
1523
49
1476
51
1432
1358
1270
LOW
3.0
1387
53
1332
54
1305
55
1258
N/A
1215
N/A
1159
1101
1032
HIGH
5.0
2059
41
1952
44
1900
45
1802
47
1703
50
1609
1470
1340
MED
4.0
1860
46
1792
48
1733
49
1656
51
1576
54
1477
1367
1248
MED-LO
3.5
1530
56
1505
57
1470
58
1452
59
1385
62
1305
1221
1097
LOW
3.0
1255
N/A
1253
N/A
1223
N/A
1203
N/A
1158
N/A
1111
1058
932
HIGH
5.0
2235
38
2166
39
2110
40
2021
42
1956
44
1855
1740
1618
MED
4.0
1955
44
1921
44
1860
46
1808
47
1746
49
1645
1572
1461
MED-L O
3.5
1658
51
1634
52
1590
54
1549
55
1494
57
1432
1359
1266
LOW
3.0
1418
60
1374
62
1348
63
1297
NA
1265
N/A
1219
1152
1106
HIGH
5.0
2489
N/A
2420
35
2330
37
2250
38
2183
39
2091
1963
1803
MED
4.0
2102
41
2050
42
2005
42
1944
44
1880
45
1798
1693
1602
MED-LO
3.5
1768
48
1723
49
1690
50
1624
52
1580
54
1493
1436
1339
LOW
3.0
1474
58
1429
60
1388
61
1370
62
1313
65
1253
1168
1082
HIGH
5.0
2355
43
2275
45
2177
47
2105
49
2014
51
1897
1770
1633
MED
4.0
2050
50
1996
51
1957
52
1882
54
1815
56
1708
1598
1505
MED-LO
3.5
1753
58
1703
60
1650
62
1601
64
1548
N/A
1461
1369
1264
LOW
3.0
1521
N/A
1451
N/A
1409
N/A
1328
N/A
1298
N/A
1237
1155
1042
HIGH
3.0
1512
N/A
1446
N/A
1375
N/A
1301
N/A
1222
N/A
1137
1033
940
MED
2.5
1356
N/A
1310
N/A
1261
N/A
1193
N/A
1122
30
1041
963
869
MED-LO
2.0
1168
N/A
1133
30
1092
31
1053
32
984
35
929
858
753
LOW
1.5
1053
32
1006
34
976
35
934
36
887
38
811
754
663
HIGH
3.0
1431
36
1363
37
1303
39
1236
41
1168
44
1082
1003
910
MED
2.5
1305
39
1251
41
1197
43
1148
45
1076
48
1012
931
842
MED-LO
2.0
1141
45
1109
46
1070
48
1017
50
969
53
904
826
737
LOW
1.5
1041
49
996
51
962
53
913
56
876
58
807
729
658
HIGH
4.0
1881
36
1762
39
1703
40
1601
43
1516
45
1393
1310
1171
MED
3.5
1758
39
1686
40
1628
42
1533
44
1441
47
1339
1249
1153
MED-LO
3.0
1577
43
1523
45
1458
47
1400
49
1303
52
1228
1126
1030
LOW
2.5
1338
51
1306
52
1267
54
1215
56
1146
59
1086
1011
909
HIGH
4.0
2119
40
2040
42
1940
44
1903
45
1834
46
1732
1638
1524
MED
3.5
1953
44
1878
45
1815
47
1754
49
1670
51
1590
1497
1398
MED-LO
3.0
1704
50
1646
52
1598
53
1532
56
1467
58
1389
1307
1220
LOW
2.5
1458
58
1409
60
1371
62
1298
N/A
1251
N/A
1187
1130
1040
DM92SS0402BN*
0.1
0.2
0.3
0.4
0.5
DM92SS0403ANA*
DM92SS0603BNA*
DM92SS0803BNA*
DM92SS0804CNA*
DM92SS0805CNA*
DM92SS1004CNA*
DM92SS1005CNAA
DC92SS0402BNA*
DC92SS0603BNA*
DC92SS0804CNA*
DC92SS1005CNA*
DM92SS1005CNAB
DM92SS1205DNA*
5.
The chart is for information only. For satisfactory operation, external static
pressure must not exceed value shown on rating plate. The shaded area
indicates ranges in excess of maximum external static pressure allowed when
heating. The data for 0.6" w.c. to 0.8" w.c. is shown for air conditioning
purposes only.
6.
At higher altitudes, a properly derated unit will have approximately the same
temperature rise at a particular CFM, while the ESP at that CFM will be lower.
DM92SS* & DC92SS*