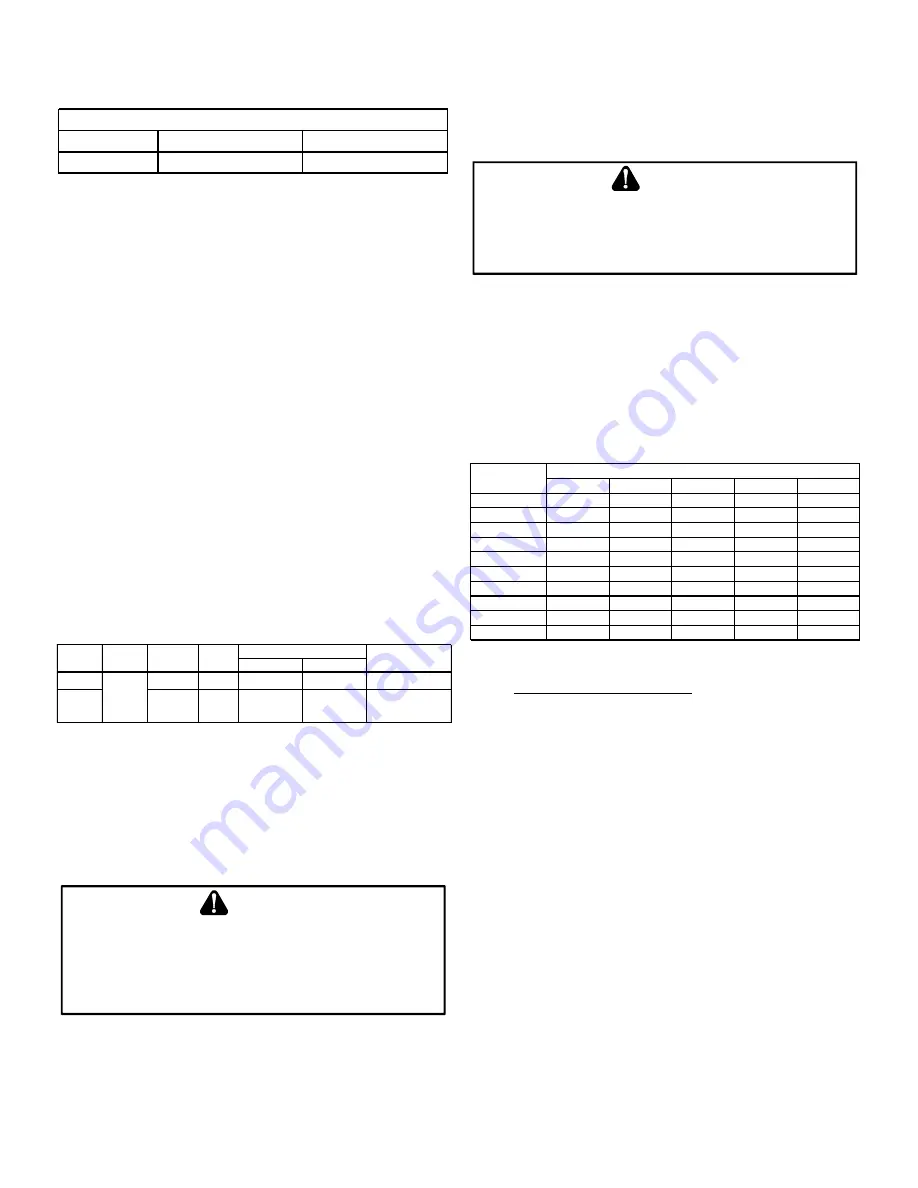
21
NOTE:
Do not remove the gas valve inlet plug before the gas
line is installed. Replace if water or debris has been introduced.
Natural Gas
Minimum: 4.5" w.c.
Maximum: 10.0" w.c.
Propane Gas
Minimum: 11.0" w.c.
Maximum: 13.0" w.c.
INLET GAS SUPPLY PRESSURE
NOTE:
Adjusting the minimum supply pressure below the limits
in the above table could lead to unreliable ignition. Gas input to
the burners must not exceed the rated input shown on the
rating plate. Overfiring of the furnace can result in premature
heat exchanger failure. Gas pressures in excess of 13 inches
water column can also cause permanent damage to the gas
valve.
At all altitudes, the manifold pressure must be within 0.3 inches
w.c. of that listed in the Specification Sheet applicable to your
model for the fuel used. At all altitudes and with either fuel, the
air temperature rise must be within the range listed on the fur-
nace nameplate. Should this appliance be converted to LP,
refer to the instructions included in the factory authorized LP
conversion kit.
H
IGH
A
LTITUDE
D
ERATE
High altitude installations may require both a pressure switch
and an orifice change. These changes are necessary to com-
pensate for the natural reduction in the density of both the gas
fuel and the combustion air at higher altitude.
For installations above 7000 feet, please refer to your distribu-
tor for required kit(s).
High Stage Low Stage
Natural
None
#45
3.5" w.c.
1.9" w.c.
None
Propane
LPM-06
#55
10.0" w.c.
6.0" w.c.
None
Gas
0-7000
Manifold Pressure
Pressure
Switch Change
Altitude
Kit
Orifice
Consult the furnace Specification Sheet for appropriate
manufacturer’s kits for propane gas and/or high altitude instal-
lations. The indicated kits must be used to insure safe and
proper furnace operation. All conversions must be performed
by a qualified installer, or service agency.
P
ROPANE
G
AS
C
ONVERSION
WARNING
P
OSSIBLE
PROPERTY
DAMAGE
,
PERSONAL
INJURY
OR
DEATH
MAY
OCCUR
IF
THE
CORRECT
CONVERSION
KITS
ARE
NOT
INSTALLED
. T
HE
APPROPRIATE
KITS
MUST
BE
APPLIED
TO
ENSURE
SAFE
AND
PROPER
FURNACE
OPERATION
. A
LL
CONVERSIONS
MUST
BE
PERFORMED
BY
A
QUALIFIED
INSTALLER
OR
SERVICE
AGENCY
.
This unit is configured for natural gas. The appropriate
manufacturer’s propane gas conversion kit, must be applied for
propane gas installations.
If converting to LP gas, it is recommended that an LPLP0* kit
also be installed. The use of this kit will prevent the furnace
from firing when the LP gas supply pressure is too low to sup-
port proper combustion.
G
AS
P
IPING
C
ONNECTIONS
T
O
AVOID
POSSIBLE
UNSATISFACTORY
OPERATION
OF
EQUIPMENT
DAMAGE
DUE
TO
UNDERFIRING
OR
EQUIPMENT
,
USE
THE
PROPER
SIZE
OF
NATURAL
/
PROPANE
GAS
PIPING
NEEDED
WHEN
RUNNING
PIPE
FROM
THE
METER
/
TANK
TO
THE
FURNACE
.
WARNING
When sizing gas lines, be sure to include all appliances which
will operate simultaneously.
The gas piping supplying the furnace must be properly sized
based on the gas flow required, specific gravity of the gas, and
length of the run. The gas line installation must comply with
local codes, or in their absence, with the latest edition of the
National Fuel Gas Code, NFPA 54/ANSI Z223.1.
Natural Gas Capacity of Pipe
In Cubic Feet of Gas Per Hour (CFH)
Length of
Nominal Black Pipe Size
Pipe in Feet
1/2"
3/4"
1"
1 1/4"
1 1/2"
10
132
278
520
1050
1600
20
92
190
350
730
1100
30
73
152
285
590
980
40
63
130
245
500
760
50
56
115
215
440
670
60
50
105
195
400
610
70
46
96
180
370
560
80
43
90
170
350
530
90
40
84
160
320
490
100
38
79
150
305
460
(Pressure 0.5 psig or less and pressure drop of 0.3" W.C.; Based on
0.60 Specific Gravity Gas)
CFH =
BTUH Furnace Input
Heating Value of Gas (BTU/Cubic Foot)
To connect the furnace to the building’s gas piping, the installer
must supply a ground joint union, drip leg, manual shutoff valve,
and line and fittings to connect to gas valve. In some cases,
the installer may also need to supply a transition piece from 1/
2" pipe to a larger pipe size.
The following stipulations apply when connecting gas piping.
•
Gas piping must be supported external to the furnace
cabinet so that the weight of the gas line does not
distort the burner rack, manifold or gas valve.
•
Use black iron or steel pipe and fittings for the building
piping.
•
Use pipe joint compound on male threads only. Pipe
joint compound must be resistant to the action of the
fuel used.
•
Use ground joint unions.
•
Install a drip leg to trap dirt and moisture before it can
enter the gas valve. The drip leg must be a minimum
of three inches long.