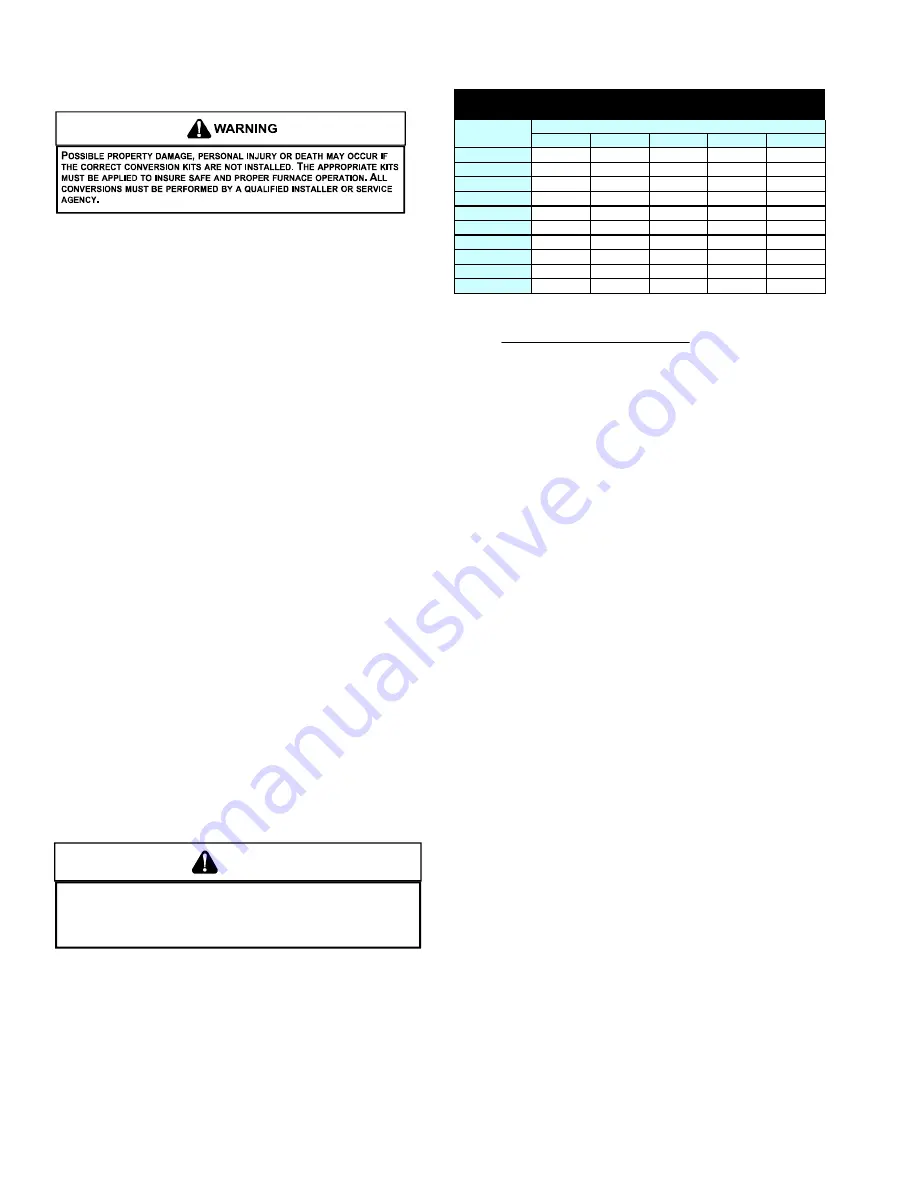
PRODUCT DESIGN
26
PROPANE GAS CONVERSION
This unit is configured for natural gas. The appropriate
manufacturer’s propane gas conversion kit, must be applied
for propane gas installations.
• Two-stage furnace models using a White-Rodgers
36G54 two-stage valve require an LPM-05 or LPM-06
LP conversion kit.
• Two-stage furnace models using a Honeywell VR9205
two-stage valve require an LPM-06 LP conversion kit.
Refer to the specification sheet for the model you are servic-
ing.
Refer to the “propane gas and/or High Altitude Installa-
tions” section for details.
GAS VALVE
This unit is equipped with a 24 volt gas valve controlled dur-
ing furnace operation by the integrated control module. As
shipped, the valve is configured for natural gas. The valve is
field convertible for use with propane gas by using the ap-
propriate propane gas conversion kit. Taps for measuring
the gas supply pressure and manifold pressure are provided
on the valve.
NOTE: The gas supply pressure on White-Rodger "G"
model gas valve, used on single stage furnaces, can
be checked with a gas pressure test kit (Part
#0151K00000S) available through our authorized dis-
tributors.
The gas valve has a manual ON/OFF control located on the
valve itself. This control may be set only to the “ON” or “OFF”
position. Refer to the
Lighting Instructions Label
or the
“Put-
ting the Furnace Into Operation”
section of this manual or
the installation instructions for use of this control during start
up and shut down periods.
GAS PIPING CONNECTIONS
CAUTION
T
O AVOID POSSIBLE UNSATISFACTORY OPERATION OR EQUIPMENT DAMAGE
DUE TO UNDERFIRING OF EQUIPMENT, USE THE PROPER SIZE OF
NATURAL/PROPANE GAS PIPING NEEDED WHEN RUNNING PIPE FROM THE
METER/TANK TO THE FURNACE.
The gas piping supplying the furnace must be properly sized
based on the gas flow required, specific gravity of the gas,
and length of the run. The gas line installation must comply
with local codes, or in their absence, with the latest edition
of the National Fuel Gas Code, NFPA 54/ANSI Z223.1.
Length of
Nominal Black Pipe Size
Pipe in Feet
1/2"
3/4"
1"
1 1/4"
1 1/2"
10
132
278
520
1050
1600
20
92
190
350
730
1100
30
73
152
285
590
980
40
63
130
245
500
760
50
56
115
215
440
670
60
50
105
195
400
610
70
46
96
180
370
560
80
43
90
170
350
530
90
40
84
160
320
490
100
38
79
150
305
460
CFH =
(Pressure 0.5 psig or less and pressure drop of 0.3" W.C.; Based on 0.60 Specific
Gravity Gas)
Natural Gas Capacity of Pipe
In Cubic Feet of Gas Per Hour (CFH)
BTUH Furnace Input
Heating Value of Gas (BTU/Cubic Foot)
To connect the furnace to the building’s gas piping, the in-
staller must supply a ground joint union, drip leg, manual
shutoff valve, and line and fittings to connect to gas valve. In
some cases, the installer may also need to supply a transi-
tion piece from 1/2" pipe to a larger pipe size.
The following stipulations apply when connecting gas pip-
ing. Refer to the following figures for typical gas line con-
nections to the furnace.
1.
Use black iron or steel pipe and fittings for the build-
ing piping.
2.
Use pipe joint compound on male threads only. Pipe
joint compound must be resistant to the action of the
fuel used.
3.
Use ground joint unions.
4.
Install a drip leg to trap dirt and moisture before it can
enter the gas valve. The drip leg must be a minimum
of three inches long.
5.
Install a 1/8" NPT pipe plug fitting, accessible for test
gage connection, immediately upstream of the gas
supply connection to the furnace.
6.
Use two pipe wrenches when making connection to
the gas valve to keep it from turning. The orientation of
the gas valve on the manifold must be maintained as
shipped from the factory.
7.
Install a manual shutoff valve between the gas meter
and unit within six feet of the unit. If a union is in-
stalled, the union must be downstream of the manual
shutoff valve, between the shutoff valve and the fur-
nace.
8.
Tighten all joints securely.
9.
Connect the furnace to the building piping by one of
the following methods:
– Rigid metallic pipe and fittings.