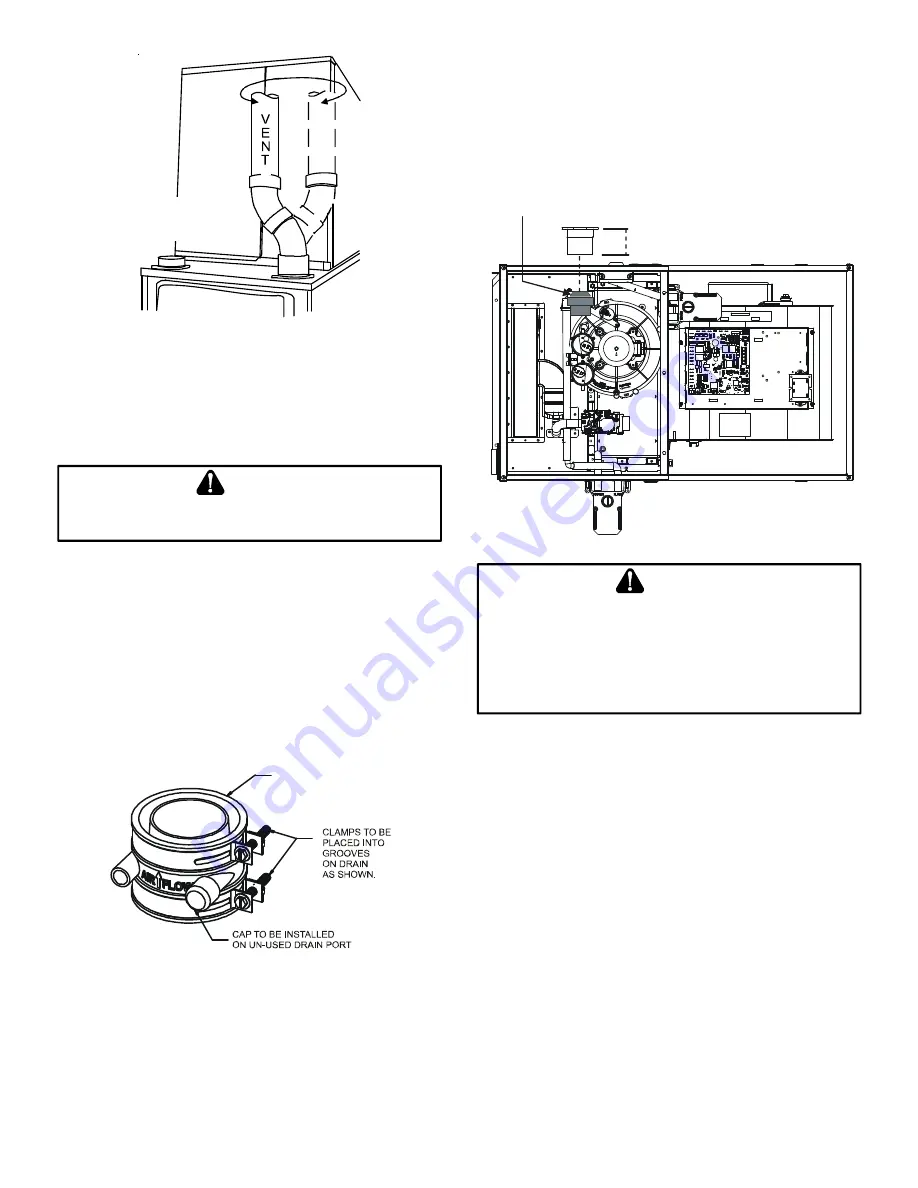
12
45 DEGREE
ELBOWS
Increased Clearance Configuration
Figure 8A
NOTE:
For
non-direct vent
installations, a minimum of
one 90° elbow should be installed on the combustion air
intake coupling to guard against inadvertent blockage.
E
DGES
OF
SHEET
METAL
HOLES
MAY
BE
SHARP
. U
SE
GLOVES
AS
A
PRECAUTION
WHEN
REMOVING
HOLE
PLUGS
.
WARNING
C
OMBUSTION
A
IR
P
IPE
D
IRECT
V
ENT
I
NSTALLATIONS
On
upflow
units secure the combustion air intake pipe to the
air intake coupling by using a take apart rubber coupling
supplied with the furnace or a plastic coupling. Also, the
intake coupling may be inverted to allow the intake pipe
to be glued directly to it. After inverting the coupling,
secure it to the furnace top with screws.
VENT-DRAIN
The RF000142 Coupling
Figure 8B
COMBUSTION AIR INTAKE OPTIONS:
The RF000142 coupling
can be secured directly to the furnace intake coupling if con-
densation is a concern. If the RF000142 is used on the com-
bustion air inlet, it must be installed with the arrow pointing
up. It should be noted, the combustion air will actually be
moving in a direction opposite of the arrow on the RF000142
coupling. It must have a field supplied, trapped drain tube
free-draining to proper condensate disposal location. A loop
in the drain tube can serve as a trap. The unused RF000142
drain fitting should be capped. (Figure 8B) A tee installed in
the intake pipe is also an acceptable method of catching
condensation. It must have a field supplied, trapped drain
tube or pipe, free-draining to proper condensate disposal
location. A loop in the drain tube can serve as a trap.
Insert flange. Cut 2 ½” long
.
RF000142
2 ½”
Figure 9
T
HE
RUBBER
ELBOW
IS
NOT
DESIGNED
TO
SUPPORT
A
LOAD
. W
HEN
THE
RUBBER
ELBOW
IS
MOUNTED
EXTERNALLY
TO
THE
FURNACE
CABINET
,
EXTREME
CARE
MUST
BE
TAKEN
TO
ADEQUATELY
SUPPORT
FIELD
-
SUPPLIED
VENT
/
FLUE
PIPING
,
AS
DAMAGE
CAN
RESULT
IN
LEAKS
CAUSING
BODILY
INJURY
OR
DEATH
DUE
TO
EXPOSURE
TO
FLUE
GASES
,
INCLUDING
CARBON
MONOXIDE
WARNING
N
ON
-D
IRECT
V
ENT
I
NSTALLATIONS
A minimum of one 90° elbow should be installed on the combus-
tion air intake “coupling” to guard against inadvertent block-
age.
A
LTERNATE
V
ENT
/F
LUE
L
OCATION
The alternate vent/flue location is the large hole directly
in
line with the induced draft blower outlet. To use the alter-
nate vent/flue location refer to the following steps and the
Alternate Vent/Flue Location Figure 9.
NOTE: In the horizontal left installation position, a means
of condensate collection must be provided to keep vent
pipe condensate from entering the draft inducer housing.
If the vent drain elbow is eliminated from the installa-
tion, an RF000142 kit must be used.
1. Remove the four screws from the vent pipe flange on
top the furnace.