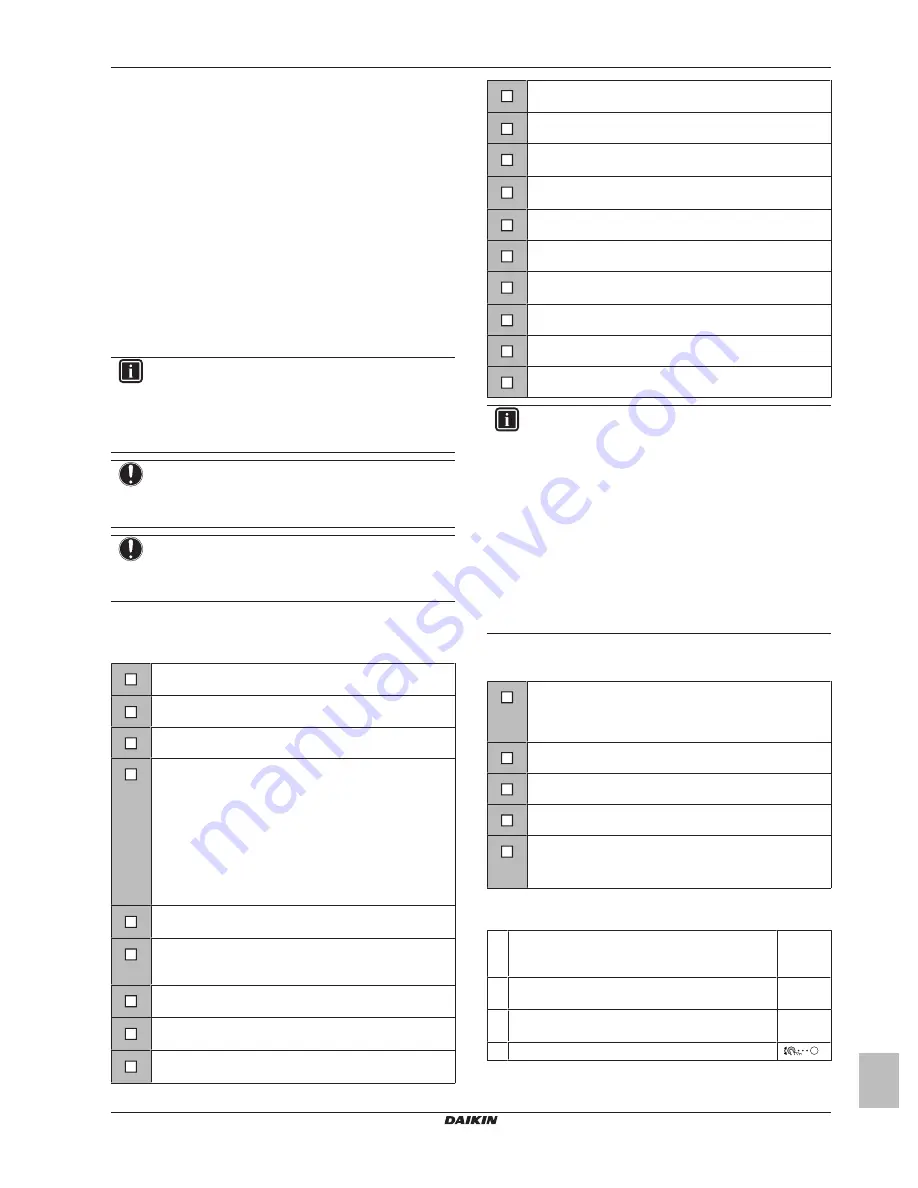
9 Commissioning
Installer reference guide
77
ERGA04~08DAV3(A) + EHVH/X04+08S18+23DA
Daikin Altherma – Low temperature split
4P495248-1 – 2017.12
9
Commissioning
9.1
Overview: Commissioning
This chapter describes what you have to do and know to
commission the system after it is configured.
Typical workflow
Commissioning typically consists of the following stages:
1
Checking the "Checklist before commissioning".
2
Performing an air purge.
3
Performing a test run for the system.
4
If necessary, performing a test run for one or more actuators.
5
If necessary, performing an underfloor heating screed dryout.
9.2
Precautions when commissioning
INFORMATION
During the first running period of the unit, the required
power may be higher than stated on the nameplate of the
unit. This phenomenon is caused by the compressor, that
needs a continuous run time of 50 hours before reaching
smooth operation and stable power consumption.
NOTICE
NEVER operate the unit without thermistors and/or
pressure sensors/switches. Burning of the compressor
might result.
NOTICE
Do NOT operate the unit until the refrigerant piping is
complete (when operated this way, the compressor will
break).
9.3
Checklist before commissioning
Do NOT operate the system before the following checks are OK:
You read the complete installation instructions, as
described in the
installer reference guide
.
The
indoor unit
is properly mounted.
The
outdoor unit
is properly mounted.
The following
field wiring
has been carried out according
to this document and the applicable legislation:
▪ Between the local supply panel and the outdoor unit
▪ Between indoor unit and outdoor unit
▪ Between the local supply panel and the indoor unit
▪ Between the indoor unit and the valves (if applicable)
▪ Between the indoor unit and the room thermostat (if
applicable)
The system is properly
earthed
and the earth terminals
are tightened.
The
fuses
or locally installed protection devices are
installed according to this document, and have NOT been
bypassed.
The
power supply voltage
matches the voltage on the
identification label of the unit.
There are NO
loose connections
or damaged electrical
components in the switch box.
There are NO
damaged components
or
squeezed
pipes
on the inside of the indoor and outdoor units.
Backup heater circuit breaker
F1B (field supply) is
turned ON.
There are NO
refrigerant leaks
.
The
refrigerant pipes
(gas and liquid) are thermally
insulated.
The correct pipe size is installed and the
pipes
are
properly insulated.
There is NO
water leak
inside the indoor unit.
The
shut-off valves
are properly installed and fully open.
The
stop valves
(gas and liquid) on the outdoor unit are
fully open.
The
air purge
valve is open (at least 2 turns).
The
pressure relief valve
purges water when opened.
The
domestic hot water tank
is filled completely.
INFORMATION
The software is equipped with an "installer-on-site" mode
([9.G]: Disable protections), that disables automatic
operation by the unit. At first installation, setting Disable
protections is by default set to Yes, meaning automatic
operation is disabled. All protective functions are then
disabled. If the user interface home pages are off, the unit
will NOT operate automatically. To enable automatic
operation and the protective functions, set Disable
protections to No.
36 hours after the first power-on, the unit will automatically
set Disable protections to No, ending "installer-on-site"
mode and enabling the protective functions. If – after first
installation – the installer returns to the site, the installer
has to set Disable protections to Yes manually.
9.4
Checklist during commissioning
The
minimum flow rate
during backup heater/defrost
operation is guaranteed in all conditions. See "To check
the water volume and flow rate" in
"6.4 Preparing water
piping" on page 25
.
To perform an
air purge
.
To perform a
test run
.
To perform an
actuator test run
.
Underfloor screed dryout function
The underfloor screed dryout function is started (if
necessary).
9.4.1
To check the minimum flow rate
1
Confirm according to the hydraulic configuration
which space heating loops can be closed due to
mechanical, electronic, or other valves.
—
2
Close all space heating loops that can be closed
(see previous step).
—
3
Start the pump test run operation (see
"9.4.4 To
perform an actuator test run" on page 78
).
—
4
During pump test run operation, go to Sensors.
Final English - Tanslations in progress