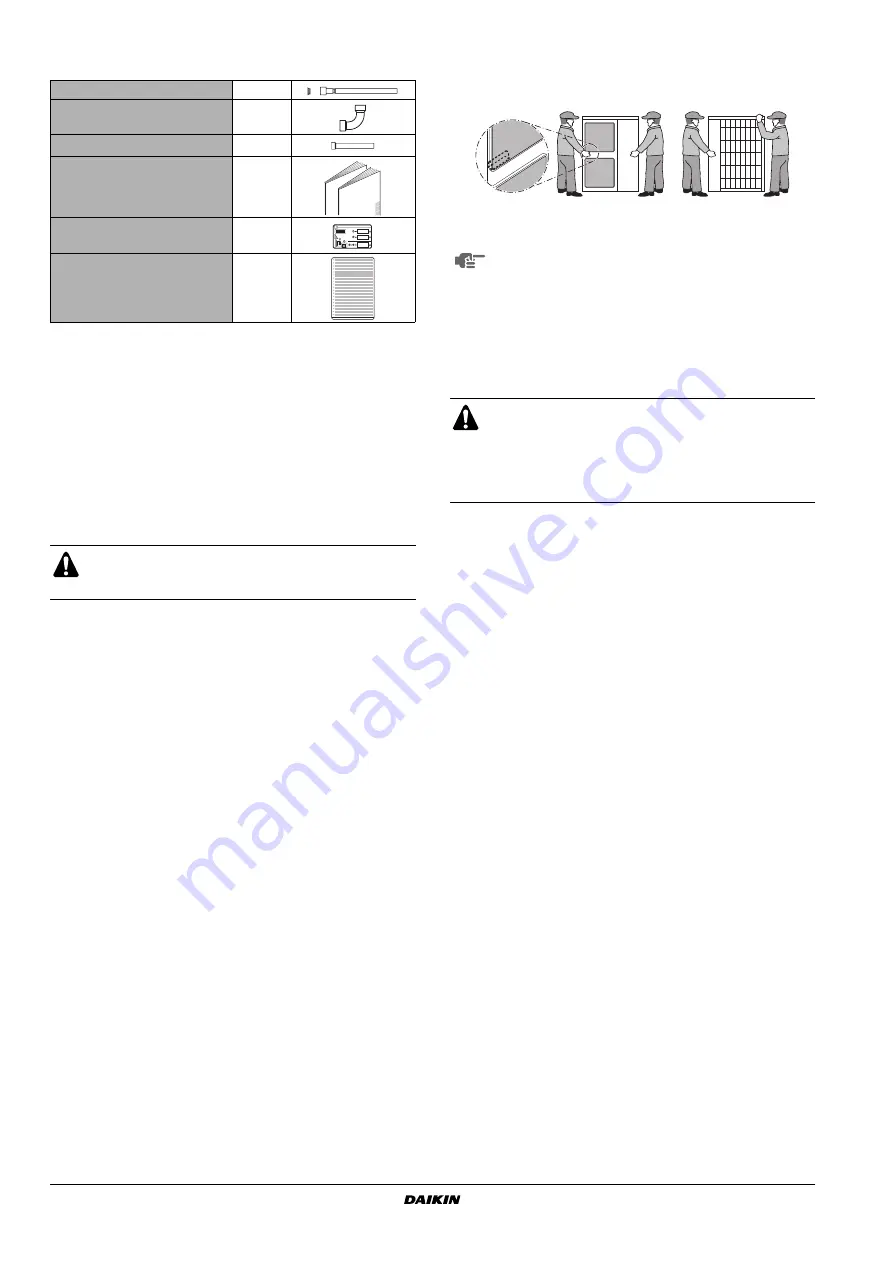
Installation manual
3
ERQ100~140A7V1B
Inverter condensing unit
4PW51321-1
2.2.
Standard supplied accessories
Location of accessories: refer to
2.3.
Technical and electrical specifications
Refer to the Engineering Data Book for the complete list of
specifications.
3.
B
EFORE
INSTALLATION
3.1.
Precautions for R410A
■
The refrigerant requires strict cautions for keeping the system
clean, dry and tight.
-
Clean and dry
Foreign materials (including mineral oils or moisture) should be
prevented from getting mixed into the system.
-
Tight
Read
"8. Precautions on refrigerant piping" on page 6
and follow these procedures correctly.
■
Since R410A is a mixed refrigerant, the required additional
refrigerant must be charged in its liquid state. (If the refrigerant
is in state of gas, its composition changes and the system will
not work properly).
■
The connected air handling units must be air handling units
designed exclusively for R410A.
3.2.
Installation
■
For installation of the air handling unit(s), refer to the air handling
unit installation manual.
■
Never operate the air conditioner with the discharge pipe
thermistor (R2T), suction pipe thermistor (R3T) and pressure
sensors (S1NPH, S1NPL) removed. Such operation may burn
out the compressor.
■
Be sure to confirm the model name and the serial no. of the
outer (front) plates when attaching/detaching the plates to avoid
mistakes.
■
When closing the service panels, take care that the tightening
torque does not exceed 4.1 N•m.
3.3.
Handling
As shown in the figure, bring the unit slowly by grabbing the left and
right grips.
Place your hands on the corner instead of holding the suction inlet in
the side of the casing, otherwise the casing could be deformed.
4.
S
ELECTING
INSTALLATION
SITE
This is a class A product. In a domestic environment this product may
cause radio interference in which case the user may be required to
take adequate measures.
1
Select an installation site where the following conditions are
satisfied and that meets with your customer’s approval.
-
Places which are well-ventilated.
-
Places where the unit does not bother next-door neighbours.
-
Safe places which can withstand the unit’s weight and
vibration and where the unit can be installed level.
-
Places where there is no possibility of flammable gas or
product leak.
-
Places where servicing space can be well ensured.
-
Places where the air handling and outdoor units’ piping and
wiring lengths come within the allowable ranges.
-
Places where water leaking from the unit cannot cause
damage to the location (e.g. in case of a blocked drain pipe).
-
Places where the rain can be avoided as much as possible.
2
When installing the unit in a place exposed to strong wind, pay
special attention to the following.
Strong winds of 5 m/sec or more blowing against the outdoor
unit’s air outlet causes short circuit (suction of discharge air),
and this may have the following consequences:
-
Deterioration of the operational capacity.
-
Frequent frost acceleration in heating operation.
-
Disruption of operation due to rise of high pressure.
-
When a strong wind blows continuously on the face of the
unit, the fan can start rotating very fast until it breaks.
Refer to the figures for installation of this unit in a place where
the wind direction can be foreseen.
Gas line piping (1)
(*)
+ copper gasket
(*)
Only for ERQ140.
1
Gas line piping (2)
1
Gas line piping (3)
1
Installation manual
Operation manual
1
1
Fluorinated greenhouse gases label
1
Multilingual fluorinated greenhouse
gases label
1
1
Accessories
Since design pressure is 4.0 MPa or 40 bar, pipes of larger
wall thickness may be required. Refer to paragraph
"7.1. Selection of piping material" on page 6
+
Take care not to let hands or objects come in contact with
rear fins.
■
Make sure to provide for adequate measures in order
to prevent that the outdoor unit be used as a shelter
by small animals.
■
Small animals making contact with electrical parts can
cause malfunctions, smoke or fire. Please instruct the
customer to keep the area around the unit clean.