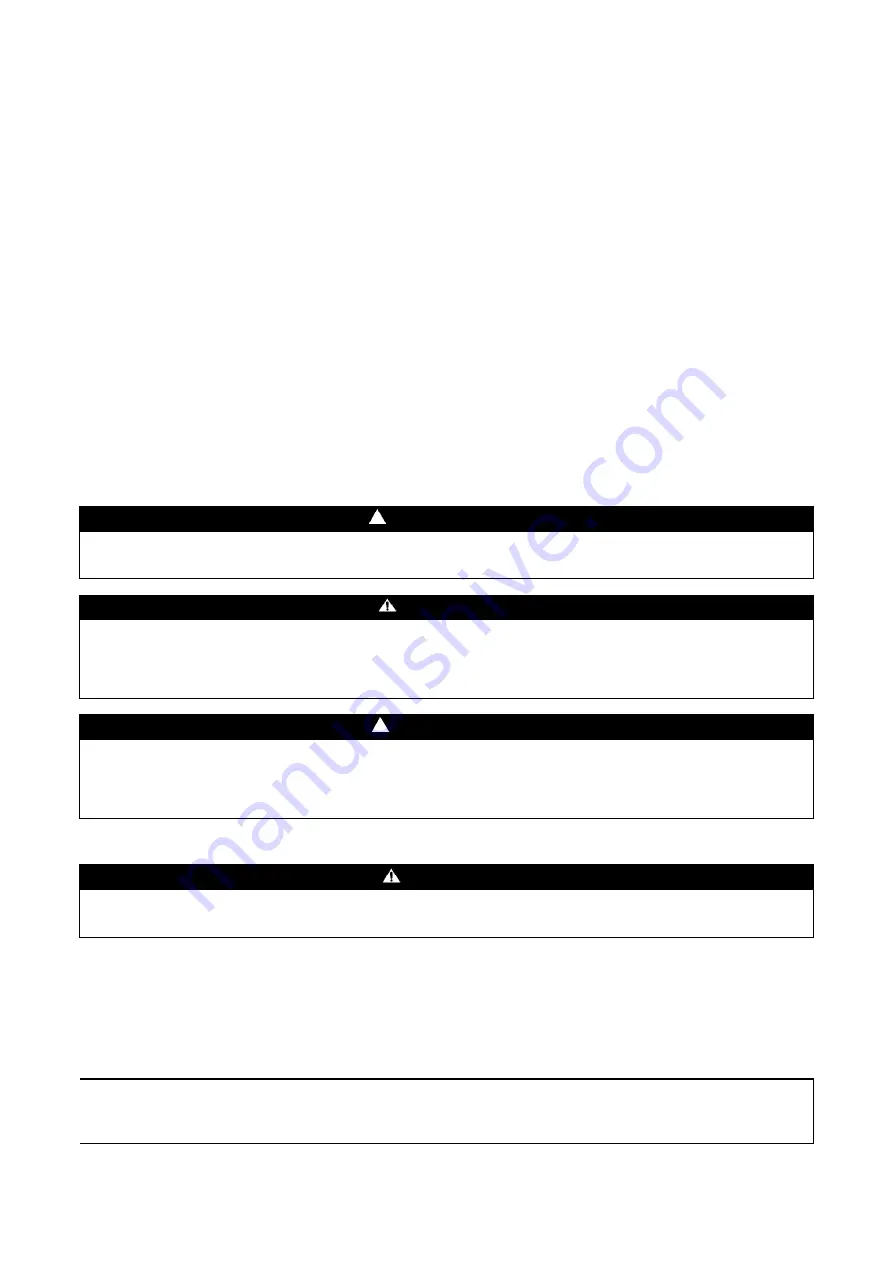
D
–EIMAC00708-16EN - 67/76
5)
Connect the recuperator to the compressor and recover the refrigerant in a suitable and clean storage
container.
6)
Evacuate the refrigerant until the internal pressure has turned negative (compared to atmospheric pressure).
The amount of refrigerant dissolved in the oil is reduced to a minimum in this way.
7)
Remove the oil in the compressor by opening the discharge valve located under the motor
8)
Remove the oil filter cover and remove the internal filtering element.
9)
Replace the cover and internal sleeve gasket. Do not lubricate the gaskets with mineral oil in order not to
contaminate the system.
10)
Insert the new filtering element.
11)
Reposition the filter closing cover and tighten the screws. The screws must be tightened alternately and
progressively setting the torque wrench at 60Nm.
12)
Charge the oil from the upper tap located on the oil separator. Considering the high hygroscopicity of ester oil, it
should be charged as quickly as possible. Do not expose ester oil to the atmosphere for more than 10 minutes.
13)
Close the oil charging tap.
14)
Connect the vacuum pump and evacuate the compressor up to a vacuum level of 230 Pa.
15)
On reaching the abovesaid vacuum level, close the vacuum pump tap.
16)
Open the system’s discharge, suction and liquid injection valves.
17)
Disconnect the vacuum pump from the compressor.
18)
Remove the warning plate from the general disconnector switch.
19)
Close the general disconnecting switch Q10 to supply power to the machine.
20)
Start the machine by following the startup procedure described above.
Refrigerant charge
ATTENTION
The units have been designed to function with R134a refrigerant. So DO NOT USE refrigerants other than R134a.
WARNING
When refrigerant gas is added to or removed from the system, ensure proper water flow through the evaporator for the
entire charge/discharge time. Interrupting the water flow during this procedure would cause the evaporator to freeze with
consequent breakage of its internal piping.
Damage from freezing voids the warranty.
ATTENTION
Removal of the refrigerant and replenishing operations must be performed by technicians who are qualified to use the
appropriate materials for this unit. Unsuitable maintenance can result in uncontrolled losses in pressure and fluid. Do
not disperse the refrigerant and lubricating oil in the environment. Always be equipped with a suitable recovery system.
The units ship with a full refrigerant charge, but in some cases it could be necessary to replenish the machine in the field.
WARNING
Always verify the causes of a loss of refrigerant. Repair the system if necessary then recharge it.
The machine can be replenished under any stable load condition (preferably between 70 and 100%) and under any
ambient temperature condition (preferably above 20°C). The machine should be kept on for at least 5 minutes to allow
the ventilator steps, and thus the condensation pressure, to stabilise.
Approximately 15% of the condenser batteries is dedicated to subcool the liquid refrigerant. The subcooling value is
approximately 5-6°C (10-15°C for the economised machines).
Once the subcooling section has been completely filled, additional refrigerant does not increase system efficiency.
However, a small additional quantity of refrigerant (1
2 kg) makes the system slightly less sensitive.
Note:
W hen the load and the number of active fans vary, so does the subcooling and it requires several minutes to
stabilise again. However, it should never fall below 3°C under any condition. Also, the subcooling value can change
slightly as the water temperature and the intake overheating vary. As the intake overheating value decreases, there is a
corresponding decrease in subcooling.
One of the following two scenarios can arise in a machine without refrigerant: