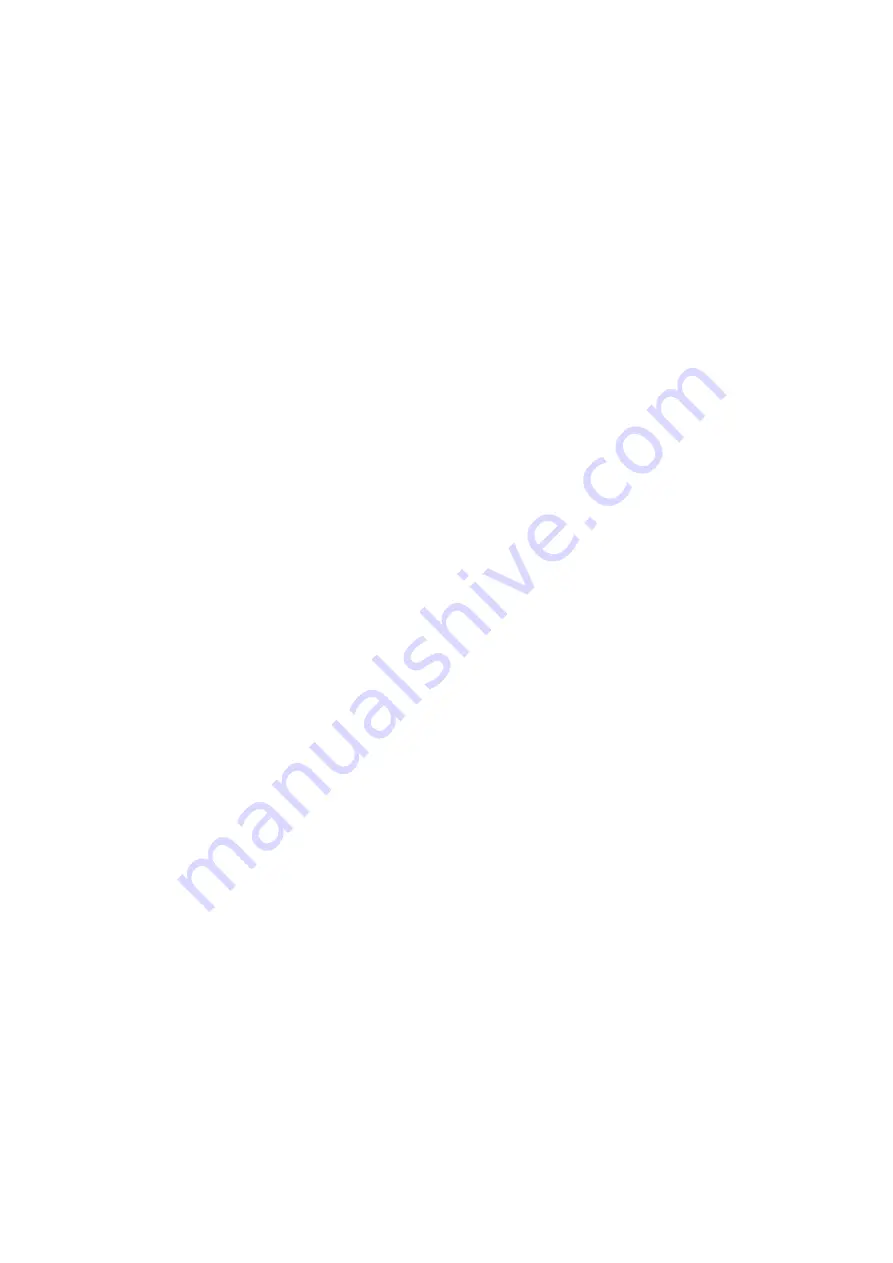
D-EIMWC00208-16EN - 18/48
Electrical components
All power and interface electrical connections are specified in the wiring diagram that is shipped with the machine.
The installer must supply the following components:
-
Power supply wires (dedicated conduit)
-
Interconnection and interface wires (dedicated conduit)
-
Thermalmagnetic circuit breaker of suitable size (please see electrical data).
Electrical wiring
Power circuit:
Connect the electrical power supply cables to the terminals of the general circuit breaker on the machine’s
terminal board. The access panel must have a hole of appropriate diameter for the cable used and its cable
gland. A flexible conduit can also be used, containing the three power phases plus earth.
In any case, absolute protection against any water penetrating through the connection point must be ensured.
Control circuit:
Every machine of the series is supplied with an auxiliary 400/115V control circuit transformer. No additional
cable for the control system power supply is thus required.
Only if the optional separate accumulation tank is requested, the electrical antifreeze resistance must have a
separate power supply.
Electrical heaters
Each circuit has an electrical heater installed in the compressor, whose purpose is to keep the oil warm thus preventing
the presence of liquid refrigerant mixed with the oil in the compressor. Obviously, the operation of the electrical heat ers is
guaranteed only if there is a constant power supply. If it is not possible to keep the machine powered when inactive
during winter, apply at least two of the procedures described in the “Mechanical Installation” section under the “Anti -
freeze protec
tion of evaporator and exchangers”.
If the plant uses pumps outside the machine (not supplied with the unit), the power line of each pump must be provided
with a magnetothermic switch and a control switch.
Water pump control
Connect the control contactor coil power supply to terminals 27 and 28 (pump #1) and 401 and 402 (pump 2) located on
terminal board M3, and install the contactor on a power supply having the same voltage as the pump contactor coil.
The
terminals are connected to a clean microprocessor contact.
The microprocessor contact has the following commutation capacity:
Maximum voltage:
250 Vac
Maximum current:
2 A Resistive 2 A Inductive
Reference standard:
EN 607301
The wiring described above allows the microprocessor to manage the water pum p automatically. It is good practice to
install a clean status contact pump’s thermalmagnetic circuit breaker and to connect it in series with the flow switch.
Alarm relays
– Electrical wiring
The machine has a cleancontact digital output that changes state whenever an alarm occurs in one of the refrigerant
circuits. Connect this signal to an external visual, sound alarm or to the BMS in order to monitor its operation. See the
machine’s wiring diagram for wiring.
Unit On/Off remote control
– Electrical wiring
The machine has a digital input that allows remote control. A startup timer, a circuit breaker or a BMS can be connected
to this input. Once the contact has been closed, the microprocessor launches the startup sequence by first turning on the
water pump and then the compressors. W hen the contact is opened the microprocessor launches the machine shutdown
sequence. The contact must be clean.
Double Setpoint
– Electrical wiring
The Double Setpoint function allows to change over the unit setpoint between two predefined values in the unit
controller. An example of an application is ice production during the night and standard operation during the day.
Connect a circuit breaker or timer between terminals 5 and 21 of terminal board M3. The contact must be clean.
External water Setpoint reset
– Electrical wiring (Optional)
The machine’s local setpoint can be modified by means of an external analogue 420 mA signal. Once this function has
been enabled, the microprocessor allows to modify the setpoint from the set local value up to a differential of 3°C. 4 mA
corresponds to a 0°C differential, 20 mA corresponds to the setpoint plus the maximum differential.
The signal cable must be directly connected to terminals 35 and 36 of the M3 terminal board.
The signal cable must be of the shielded type and must not be laid in the vicinity of the power cables, so as not to induce
interference with the electronic controller.
Summary of Contents for EWLD160~550G-SS
Page 21: ...D EIMWC00208 16EN 21 48 Fig 10 Refrigeration cycle EWWD G SS EWWD G XS 23 5 bar...
Page 23: ...D EIMWC00208 16EN 23 48 Fig 12 Refrigeration cycle EWLD G SS OPTIONAL 23 5 bar...
Page 45: ...D EIMWC00208 16EN 45 48...
Page 46: ...D EIMWC00208 16EN 46 48...
Page 47: ...D EIMWC00208 16EN 47 48...