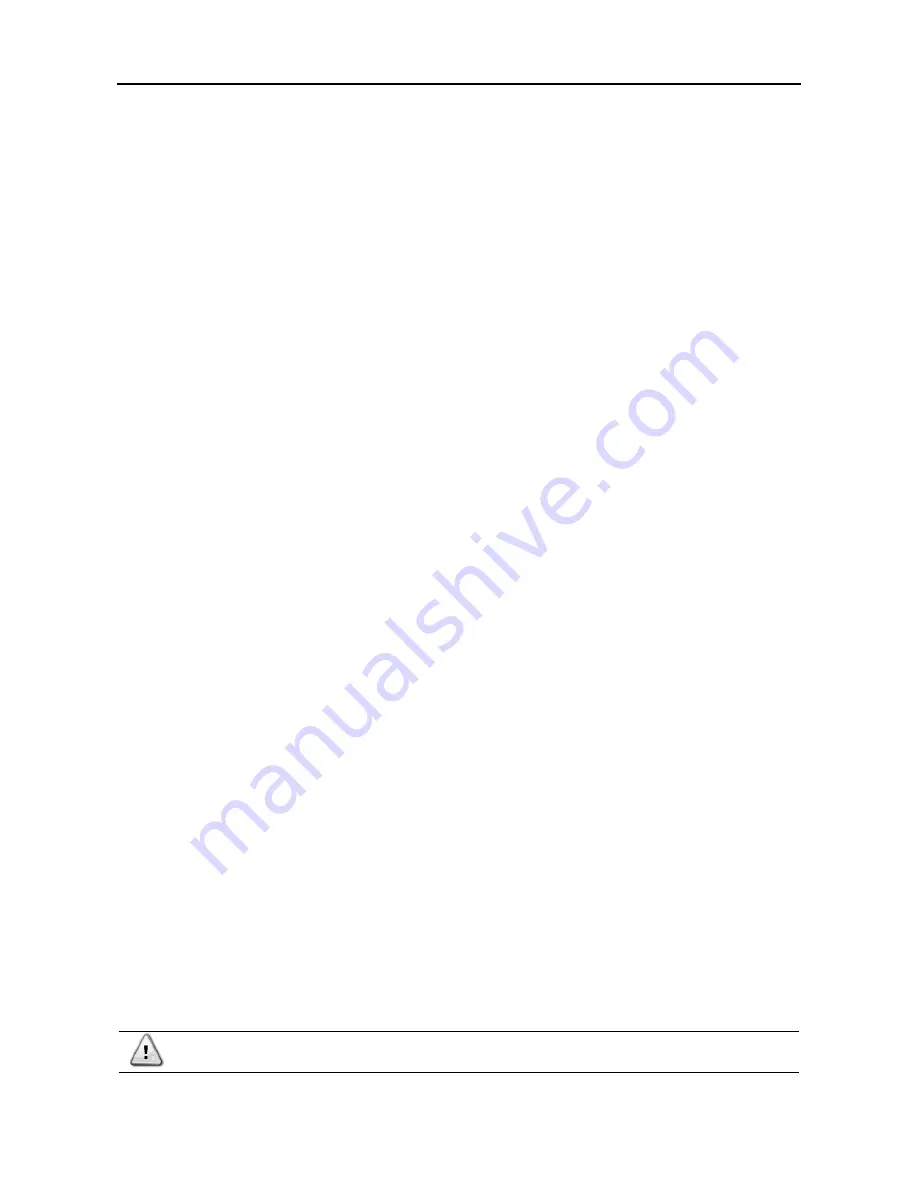
D-EIMWC01405-18EN- 19/32
3
OPERATION
3.1
Operator’s responsibilities
It is important that the operator becomes familiar with the equipment before operating the machine. In addition to reading
this manual, the operator should study the operation manual and the wiring diagram supplied with the unit to understand
commissioning, operation and the shutdown sequence as well as the shutdown mode and safeties.
During initial machine start-up, the Daikin technician is available to answer any questions and instruct on proper operating
procedures.
The operator should keep an operating data log for each specific machine. Furthermore, an additional maintenance log
should be kept for periodic maintenance and service.
This Daikin unit represents a substantial investment and deserves the attention and care to keep this equipment in good
working order. If the operator observes abnormal or unusual operating conditions, calling Daikin technical service is
recommended.
In any case, it is essential to follow the instructions below during operation and maintenance:
Do not allow unauthorized and/or unskilled personnel to access the unit.
It is forbidden to access the electrical components without having opened the unit main switch and switched off
the power supply.
It is forbidden to access the electrical components without using an insulating platform. Do not access electrical
components if water and/or moisture are present.
Ensure that all operations on the refrigerant circuit and on components under pressure are exclusively carried
out by qualified personnel.
Compressors should only be replaced by qualified personnel.
Sharp edges can cause injuries. Avoid direct contact.
Do not introduce solid objects into the water pipes while the unit is connected to the system.
A mechanical filter must be fitted to the water pipe connected to the heat exchanger inlet.
It is absolutely forbidden to remove any protection system covering moving parts.
In case of sudden stop of the unit, follow the instructions on the Control Panel Operating Manual which is part of the on-
board documentation delivered to the end user.
It is strongly recommended to perform installation and maintenance with other people.
In case of accidental injury or unease, it is necessary to:
Keep calm.
Press the alarm button if present in the installation site.
Immediately contact any emergency personnel in the building or the call the Emergency Services.
Wait until emergency personnel arrive and do not leave the injured person alone.
3.2
Unit description
The machine is made up of a latest generation, high efficiency
flooded shell and tube evaporator
, with the refrigerant
outside the tubes and the water to be cooled flowing inside the tube..
A shell and tube condenser where the refrigerant condenses outside the tubes while the cooling water flows inside of the
high-efficiency tubes.
An economizer is included in the DZ series XE version.
The economizer is a plate exchanger
and uses an electronic
expansion valve for each compressor. The algorithm, in the controller, monitors various thermodynamic cycle parameters
to control these valves.
The
compressor is a centrifugal type with magnetic bearings
and thus does not require lubrication oil. A part of the
refrigerant in the liquid line is used to cool the inverter, thus permitting optimal compressor operations in the foreseen
conditions. Refrigerant flow is controlled by the compressor that continuously monitors inverter temperature.
The compressor, controlled by inverters, changes its cooling load according to the rotational speed decided by the
controller. In this way the machine perfectly adapts to system operating conditions to maximize performance.
The cooling circuit also installs an electronic overflow valve that, in addition to managing the level of refrigerant in the heat
exchangers, guarantees the correct operation of the compressor, keeping it within the foreseen limits.
All the described components are managed by an innovative microprocessor control system that, by monitoring all the
machine operating parameters, optimizes operations. A diagnostic system helps the operator in identifying alarm and fault
causes.
Before starting the compressors ensure that all valves are open and the closing caps are repositioned
and tightened.