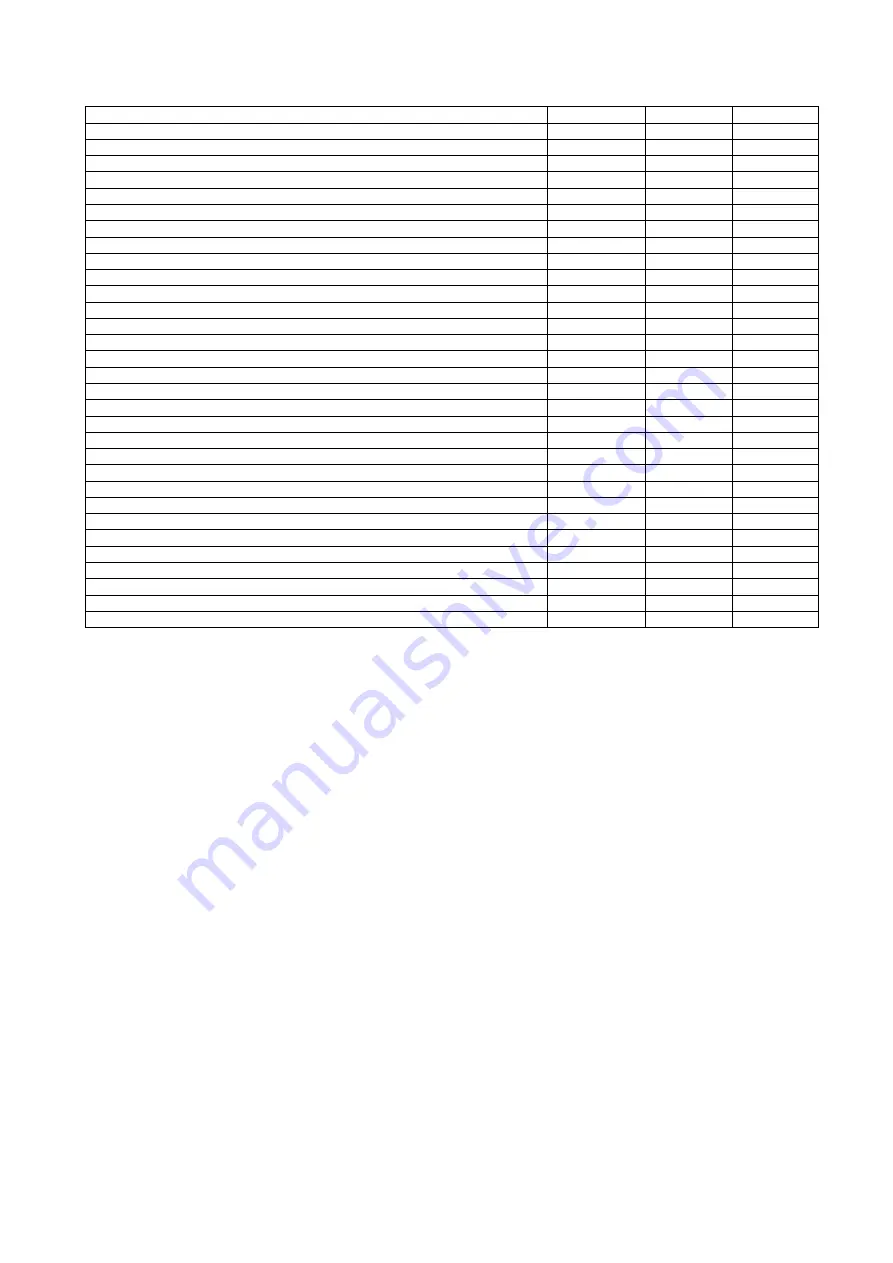
D
–EIMHP01201-18_04EN - 21/24
Paint where necessary
X
Clean and paint where necessary
X
Analysis of water (6)
X
Check of flow switch operation
X
Electrical:
Verification of control sequence
X
Verify contactor wear
– Replace if necessary
X
Verify that all electrical terminals are tight
– Tighten if necessary
X
Clean inside the electrical control board
X
Visual inspection of components for any signs of overheating
X
Verify operation of compressor and oil heater
X
Measure compressor motor insulation using the Megger
X
Clean air intake filters of the electrical panel
X
Verify operation of all ventilation fans in the electrical panel
X
Verify operation of inverter cooling valve and heater
X
Verify status of capacitors in the inverter (signs of damage, leaks, etc)
X
Refrigeration circuit:
Check for any refrigerant leakage
X
Verify refrigerant flow using the liquid sight glass
– Sight glass full
X
Verify filter dryer pressure drop
X
Verify oil filter pressure drop (Note 5)
X
Analyse compressor vibrations
X
Analyse compressor oil acidity (7)
X
Condenser section:
Clean water rinse condenser coils (Note 4)
X
Quarterly clean condenser coils (E-coated only)
X
Verify that fans are well tightened
X
Verify condenser coil fins
– Comb if necessary
X
Check the aspect of the plastic protection of the copper/aluminum connection
X
Notes:
8. Units placed or stored in a Highly Aggressive Environment for long time without operation are still subject to
those routine maintenance steps.
5.2
Unit Maintenance and Cleaning
Unit exposed to a highly aggressive environment can face corrosion in a shorter time than ones installed on a standard
environment. Corrosion causes a rapid rusting of the frame core, consequently decreases unit structure life time. To avoid
that, it is necessary to wash periodically the frame surfaces with water and suitable detergents.
In case of part of unit frame paint came off, it is important to stop its progressive deterioration by repainting the exposed
parts using proper products. Please contact factory to get the required products specifications
.
Note: in case of just salt deposits are present, it is enough to rinse the parts with fresh water.
5.3
Refrigerant charge verification
The multiporpouse units are design to operate in extremely variable conditions and modes (air to water ans water to water).
The refirgerant charge indicated on the name plate has been approved by the manufacturer allowing the unit to operate
within the declared operating envelope. The highgly variable conditions lead to situations where the sight glass on the
liquid line shows flashing of the refrigerant. Generally this phenomenon lead the field operator to charge refrigenat in the
unit. On a mutlipurpose unit doesn
’t add or remove refrigerant based only on the indication of the flashing in sight glass.
The refrigerant charge must be adjusted in water to water operation (Recovery mode) in order to avoid flashing at sight
glass on the liquid line
5.4
Inverter Electrolytic Capacitors
Compressor Inverters include electrolytic capacitors which have been designed to last a minimum of 15 years in normal
use. Heavy duty conditions may reduce the actual life of capacitors.
The unit calculates capacitor residual life based on actual operation. When residual life gets below a give threshold, a
warning is issued by the controller. In this case replacement of capacitors is recommended. This operation must be done
only by qualified technicians. Replacement must be carried out through the following procedure:
•
Power off the unit
•
Wait for 5 minutes before opening the inverter case
•
Check that residual dc voltage in the dc link is zero.
•
Open the inverter case and replace old capacitors with new ones.