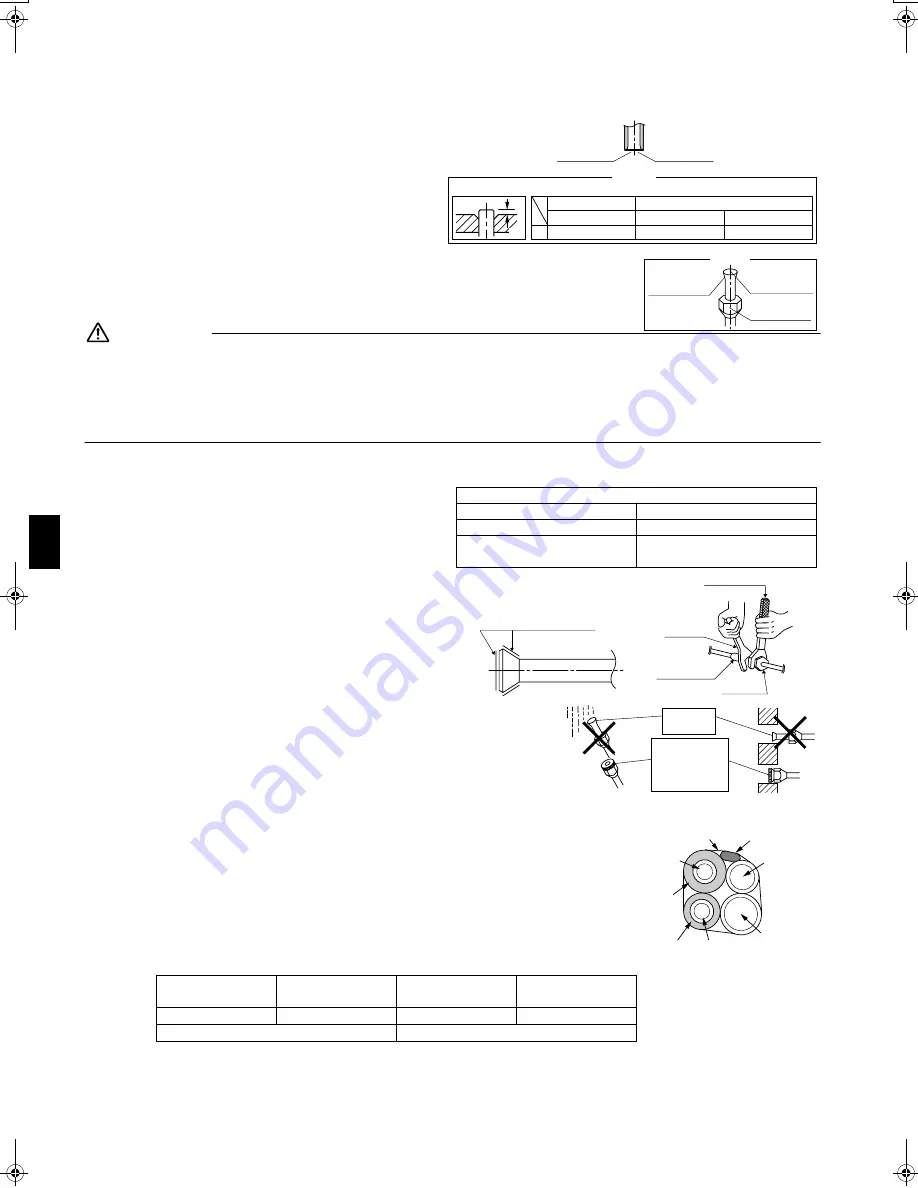
13
■
English
Refrigerant Piping Work
1.
Flaring the pipe end.
1) Cut the pipe end with a pipe cutter.
2) Remove burrs with the cut surface facing downward
so that the chips do not enter the pipe.
3) Put the flare nut on the pipe.
4) Flare the pipe.
5) Check that the flaring is properly made.
WARNING
1) Do not use mineral oil on flared part.
2) Prevent mineral oil from getting into the system as this would reduce the lifetime of the units.
3) Never use piping which has been used for previous installations. Only use parts which are delivered with the unit.
4) Do never install a drier to this R410A unit in order to guarantee its lifetime.
5) The drying material may dissolve and damage the system.
6) Incomplete flaring may cause refrigerant gas leakage.
2.
Refrigerant piping.
1) Align the centres of both flares and tighten the flare
nuts 3 or 4 turns by hand. Then tighten them fully with
the torque wrenches.
• Use torque wrenches when tightening the flare nuts to
prevent damage to the flare nuts and escaping gas.
2) To prevent gas leakage, apply refrigeration oil on both
inner and outer surfaces of the flare. (Use refrigeration
oil for R410A.)
2-1. Caution on piping handling.
1) Protect the open end of the pipe against dust and moisture.
2) All pipe bends should be as gentle as possible. Use a pipe bender
for bending.
(Bending radius should be 30 to 40mm or larger.)
2-2. Selection of copper and heat insulation materials.
• When using commercial copper pipes and fittings, observe the following:
1) Insulation material: Polyethylene foam
Heat transfer rate: 0.041 to 0.052W/mK (0.035 to 0.045 kcal/(mh•°C))
Refrigerant gas pipe’s surface temperature reaches 110°C max.
Choose heat insulation materials that will withstand this temperature.
2) Be sure to insulate both the gas and liquid piping and to provide insulation
dimensions as below.
3) Use separate thermal insulation pipes for gas and liquid refrigerant pipes.
Gas side
Liquid side
Gas pipe thermal
insulation
Liquid pipe thermal
insulation
O.D. 9.5mm
O.D. 6.4mm
I.D. 12-15mm
I.D. 8-10mm
Thickness 0.8mm
Thickness 10mm Min.
Set exactly at the position shown below.
A
Flaring
Die
A
0-0.5mm
Clutch-type
Flare tool for R410A
1.0-1.5mm
Clutch-type (Rigid-type)
1.5-2.0mm
Wing-nut type (Imperial-type)
Conventional flare tool
(Cut exactly at
right angles.)
Remove burrs
Check
Flare’s inner
surface must
be flaw-free.
The pipe end must
be evenly flared in
a perfect circle.
Make sure that the
flare nut is fitted.
32.7-39.9N
l
m
(330-407kgf
l
cm)
14.2-17.2N
l
m
(144-175kgf
l
cm)
Flare nut tightening torque
Gas side
Liquid side
3/8 inch
1/4 inch
Coat here with refrigeration oil
Torque wrench
Piping union
Flare nut
Spanner
Wall
If no flare cap is
available, cover
the flare mouth
with tape to keep
dirt or water out.
Be sure to
place a cap.
Rain
Finishing tape
Liquid pipe insulation
Inter-unit wiring
Gas pipe
insulation
Gas pipe
Humidifying
hose
Drain hose
Liquid pipe
01_EN_3P177302-1.fm Page 13 Tuesday, May 30, 2006 9:36 AM
Summary of Contents for FTXR28EV1B
Page 17: ... 0605 HT 3P177302 1 M05B200 ...