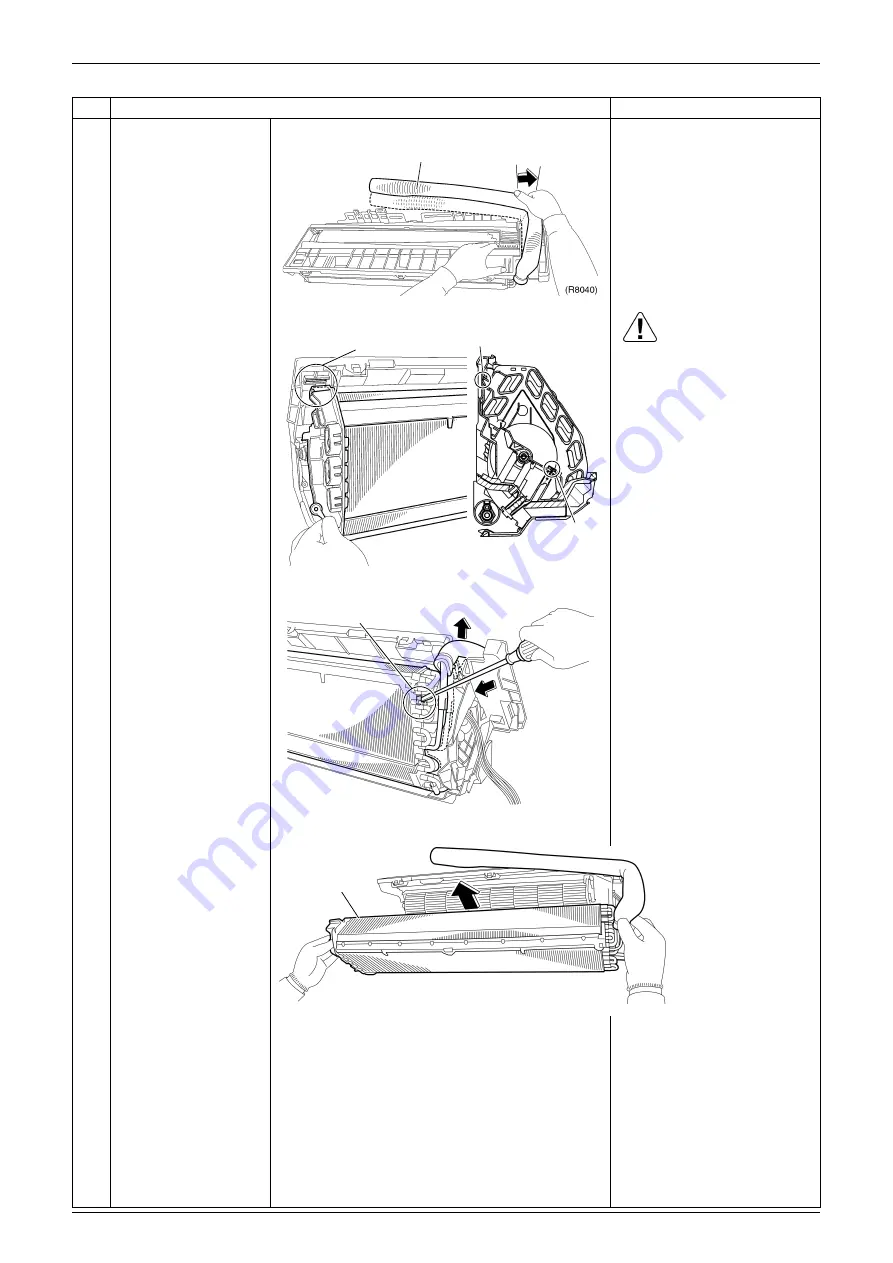
SiBE041025
Indoor Unit
Removal Procedure
113
3
Widen the auxiliary
piping to the extent of
10° ~ 20°.
4
Remove the screw on
the left side and
unfasten the hook on
the rear side.
Caution
When removing or
reassembling the indoor heat
exchanger, be sure to wear
gloves or wrap it with cloth
before proceeding to the
work. (You may be injured by
the fins.)
5
Push and unfasten the
hook on the right side
and lift up the indoor
heat exchanger.
6
Pull the indoor heat
exchanger to the front
side to unfasten the
hooks completely, and
then lift it.
Step
Procedure
Points
Auxiliary piping
(R8041)
(R11269)
Hook
Hook
Screw
Hook
(R8042)
(R8043)
Indoor heat
exchanger