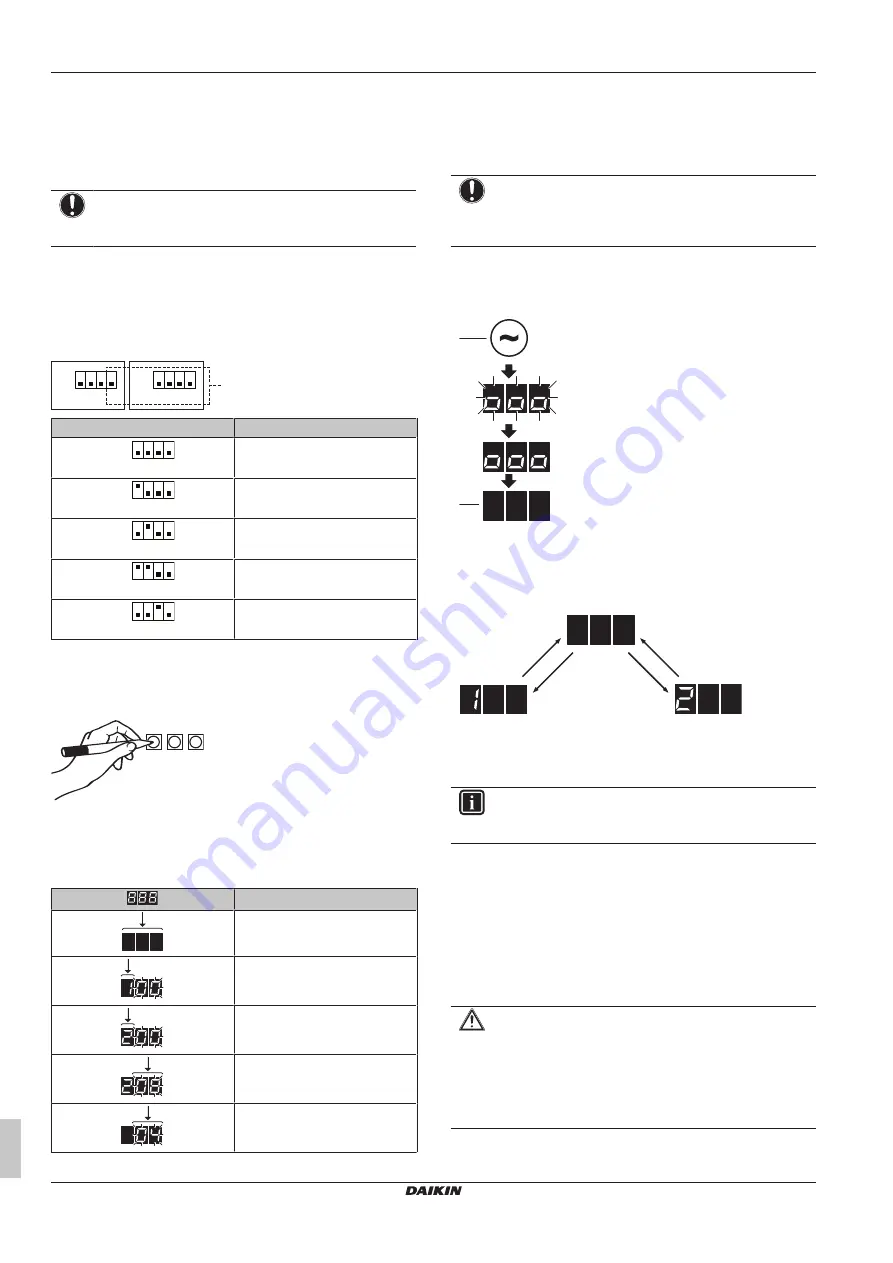
17 Commissioning
Installation and operation manual
34
LRYELRNUN5A7Y1
CO
₂
Conveni-Pack outdoor unit and capacity up unit
4P605461-1 – 2020.04
e2
Push buttons:
BS1: MODE: For changing the set mode
BS2: SET: For field setting
BS3: RETURN: For field setting
e3
DIP switches
4
After making the field settings, reattach the inspection hole
covers and the front plate.
NOTICE
Close the cover of the electrical component box before
turning ON the power.
16.1.3
Field setting components
DIP switches
Use DS1 to set the target evaporating temperature for the
refrigeration side. Do NOT change (a).
1 2 3 4
OFF
ON
DS1
1 2 3 4
OFF
ON
DS2
a
DS1
Evaporating temperature
1 2 3 4
OFF
ON
–10°C (factory setting)
1 2 3 4
OFF
ON
–20°C
1 2 3 4
OFF
ON
–15°C
1 2 3 4
OFF
ON
–5°C
1 2 3 4
OFF
ON
0°C
Push buttons
Use the push buttons to make the field settings. Operate the push
buttons with an insulated stick (such as a closed ball-point pen) to
avoid touching of live parts.
7-segment display
The display gives feedback about the field settings, which are
defined as [Mode-Setting]=Value.
Example:
Description
Default situation
Mode 1
Mode 2
Setting 8
(in mode 2)
Value 4
(in mode 2)
16.1.4
To access mode 1 or 2
After the units are turned ON, the display goes to its default
situation. From there, you can access mode 1 and mode 2.
Initialisation: default situation
NOTICE
Be sure to turn on the power 6 hours before operation in
order to have power running to the crankcase heater and
to protect the compressor.
Turn on the power supply of the outdoor unit, capacity up unit, and
all indoor units. When the communication between the units is
established and normal, the display indication state will be as below
(default situation when shipped from factory).
1~2 min
8~10 min
b
a
a
Power ON
b
Default situation
Switching between modes
Use BS1 to switch between the default situation, mode 1 and
mode 2.
BS1 [5 s]
BS1
BS1
BS1
a
b
c
a
Default situation (H1P OFF)
b
Mode 1 (H1P flashing)
c
Mode 2 (H1P ON)
BS1
Press BS1.
BS1 [5 s]
Press BS1 for at least 5 s.
INFORMATION
If you get confused in the middle of the process, press BS1
to return to the default situation.
17
Commissioning
After installation and once the field settings are defined, the installer
is obliged to verify correct operation. Therefore a test run MUST be
performed according to the procedures described below.
17.1
Precautions when commissioning
CAUTION
Do NOT perform the test operation while working on
the indoor units.
When performing the test operation, NOT only the outdoor
unit, but the connected indoor unit will operate as well.
Working on an indoor unit while performing a test operation
is dangerous.
Summary of Contents for LRYEN10A7Y1
Page 43: ......