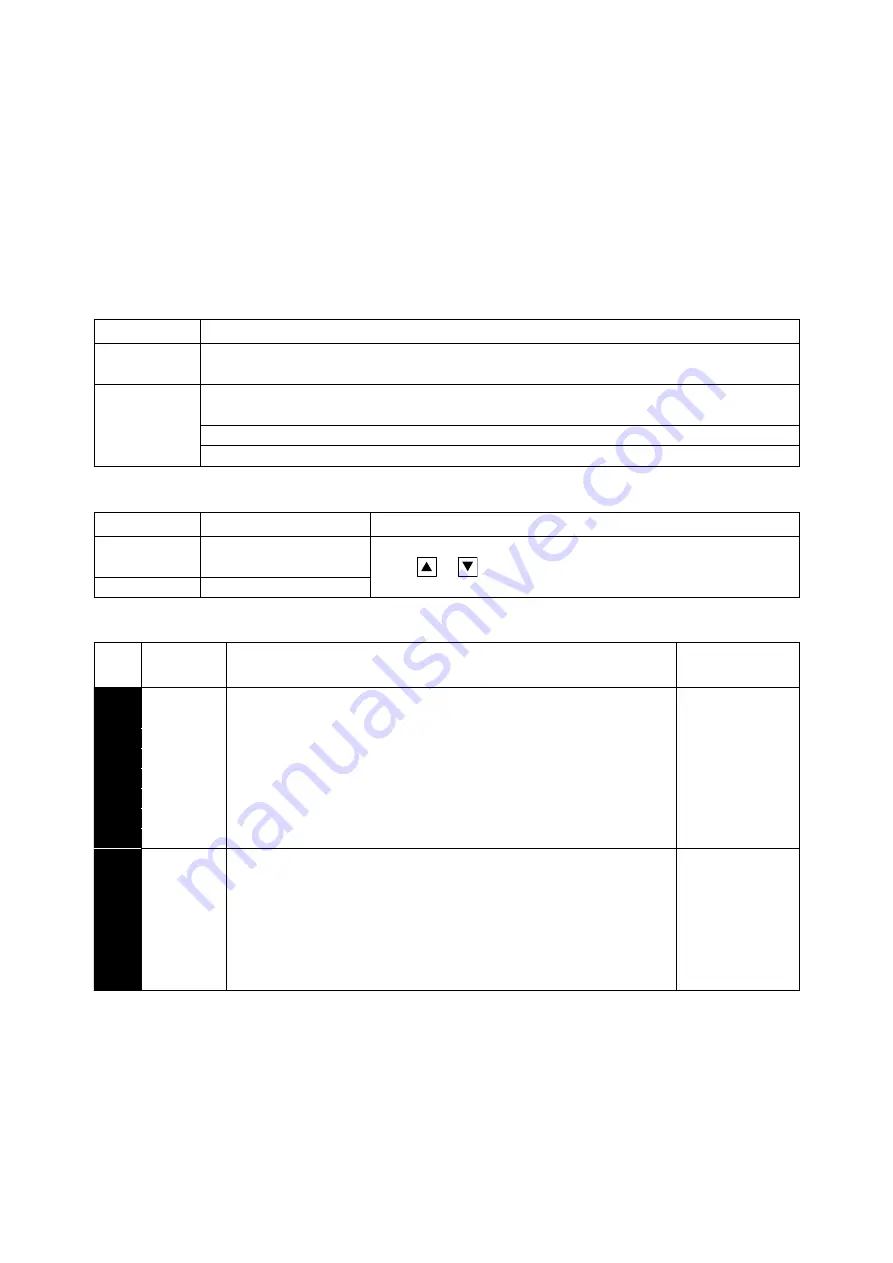
2-19
2.5 Alarm Code
●
Alarm grouping
F---
:
Alarm that unit stop
E---
:
Alarm that unit restart or backup operation
T---
:
Alarm during PTI (Refer to paragraph 3.3.2.)
F5---
:
Alarm that unit stop related to inverter
E5---
:
Alarm that unit restart related to inverter
Communication Interrupted: Communication error between CPU board (EC1) and
operation board (EC3)
Alarm
Controller action at the generating of alarm
F ---
Critical shut down.
(Requires inspection/repair)
E ---
The unit stops, but restarts 3 minutes after the condition returns to normal.
If the same error occurs multiple times, the unit will switch to standby for 4 hours or stop.
Unit continues operation by back-up operation.
Alarm display only. Unit continues operation.
Alarm LED and Alarm Code Display
Alarm
Alarm LED (Red)
Alarm code display
F Alarm,
E807, E304
Blinking
Press
or
key to display alarm code.
E Alarm
OFF
●
F Alarm
Diagnosis
Alarm
code
Alarm content
Controller action
001
F101
HPS activates within 30 seconds after compressor starts.
(2400 kPa or more)
UNIT stops
002
F109
LPT drops below -72kPa within 2 seconds after compressor starts
UNIT stops
003
F301
Temperature setting request
UNIT stops
004
F401
SS, DSS, RS and DRS all failed in chilled mode
UNIT stops
004
F405
HPT, DCHS1 and DCHS2 all failed
UNIT stops
004
F407
HPT and LPT both failed
UNIT stops
004
F409
LPT, DCHS1 and DCHS2 all failed
UNIT stops
005
F701
Abnormal power supply voltage detected within 2 seconds after
unit turns on
One of R, S or T phase is open after unit turns on
UNIT stops
006
F703
Unbalance power supply
UNIT stops
007
F705
Open power phase during operation
UNIT stops
008
F707
Fuse F2U is open (I/O board)
UNIT stops
009
F809
E809 (shortage of refrigerant) is generated twice
UNIT stops
02̲19-44̲LX10F11B̲En.indd 2-19
02̲19-44̲LX10F11B̲En.indd 2-19
2014/11/19 16:37:52
2014/11/19 16:37:52
https://daikin-p.ru
Summary of Contents for LX10F11B
Page 2: ...Revision A Correction of spelling 2012 9 28 https daikin p ru...
Page 6: ...https daikin p ru...
Page 82: ...https daikin p ru...
Page 92: ...https daikin p ru...
Page 127: ...5 9 5 6 Sequence https daikin p ru...
Page 128: ...5 10 Stereoscopic wiring diagram https daikin p ru...
Page 129: ...Revision A Correction of spelling 2012 9 28 https daikin p ru...