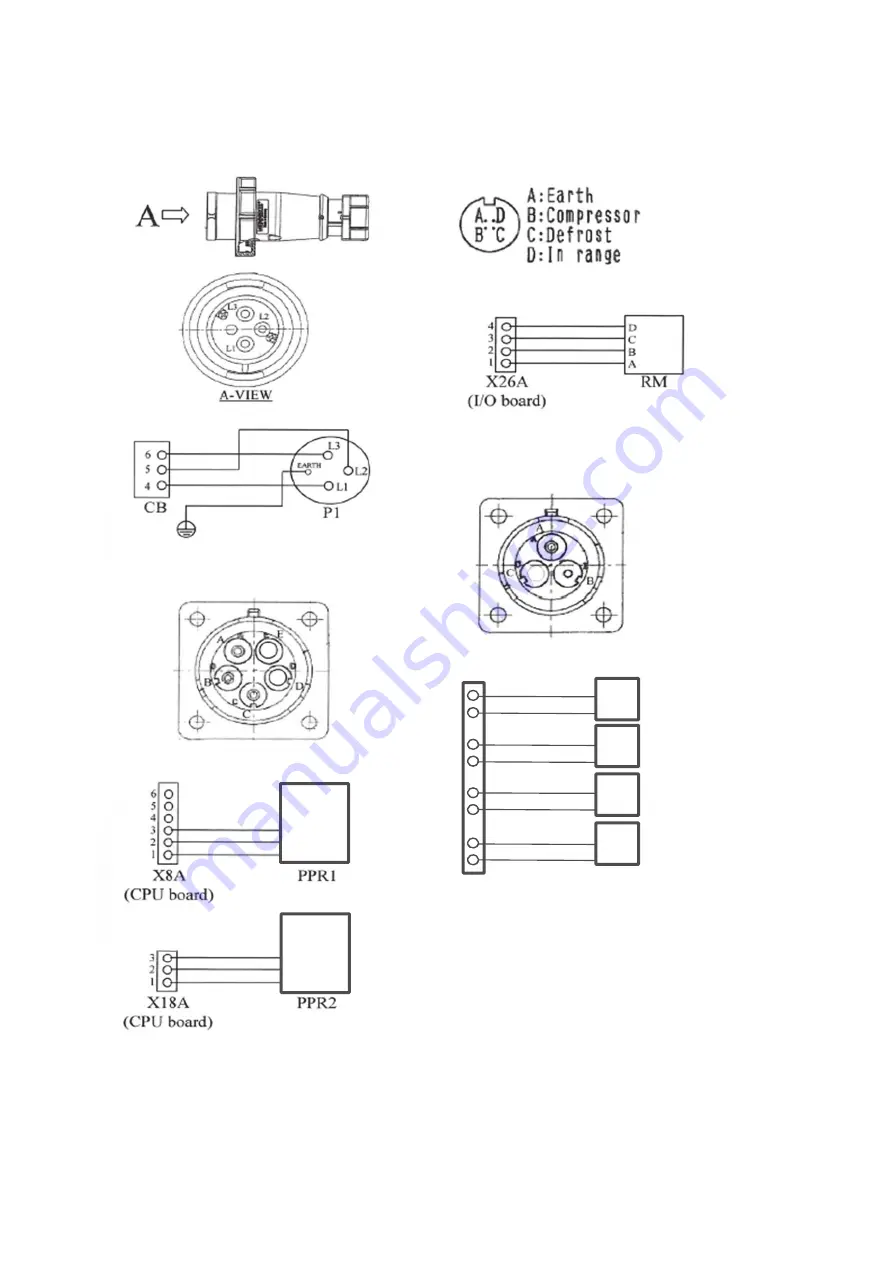
4-27
A
B
C
D
E
B
A
C
D
E
X6A
(CPU board)
1
2
3
4
5
6
7
8
A
B
C
A
B
C
A
B
C
A
B
C
CTR
(
CTS
)
UR3
(
USDA3
)
UR2
(
USDA2
)
UR1
(
USDA1
)
4.10 External Receptacle Wiring Diagrams
4.10.1 Power Plug (P1)
●
Layout
4.10.3 Remote Monitoring Receptacle (RM; option)
●
Layout (as seen from the front)
4.10.4 USDA Sensor 1 to 3 Receptacles (USDA 1 to 3; options)
Cargo Temperature Sensor Receptacle (CTR; option)
●
Layout (as seen from the front)
●
Wiring diagram
●
Wiring diagram
4.10.2 PC Port Receptacle (PPR1, 2)
●
Layout (as seen from the front)
●
Wiring diagram
●
Wiring diagram
04章̲LX10F11B3̲TR16-02̲En.indd 4-27
04章̲LX10F11B3̲TR16-02̲En.indd 4-27
2016/02/03 16:22:16
2016/02/03 16:22:16
https://daikin-p.ru
Summary of Contents for LX10F11B3
Page 7: ...https daikin p ru ...
Page 83: ...https daikin p ru ...
Page 93: ...https daikin p ru ...
Page 121: ...https daikin p ru ...
Page 129: ...https daikin p ru ...
Page 138: ...6 9 6 6 Sequence AIR WATER COOLED AIR WATER COOLED https daikin p ru ...
Page 139: ...6 10 Stereoscopic wiring diagram AIR WATER COOLED https daikin p ru ...