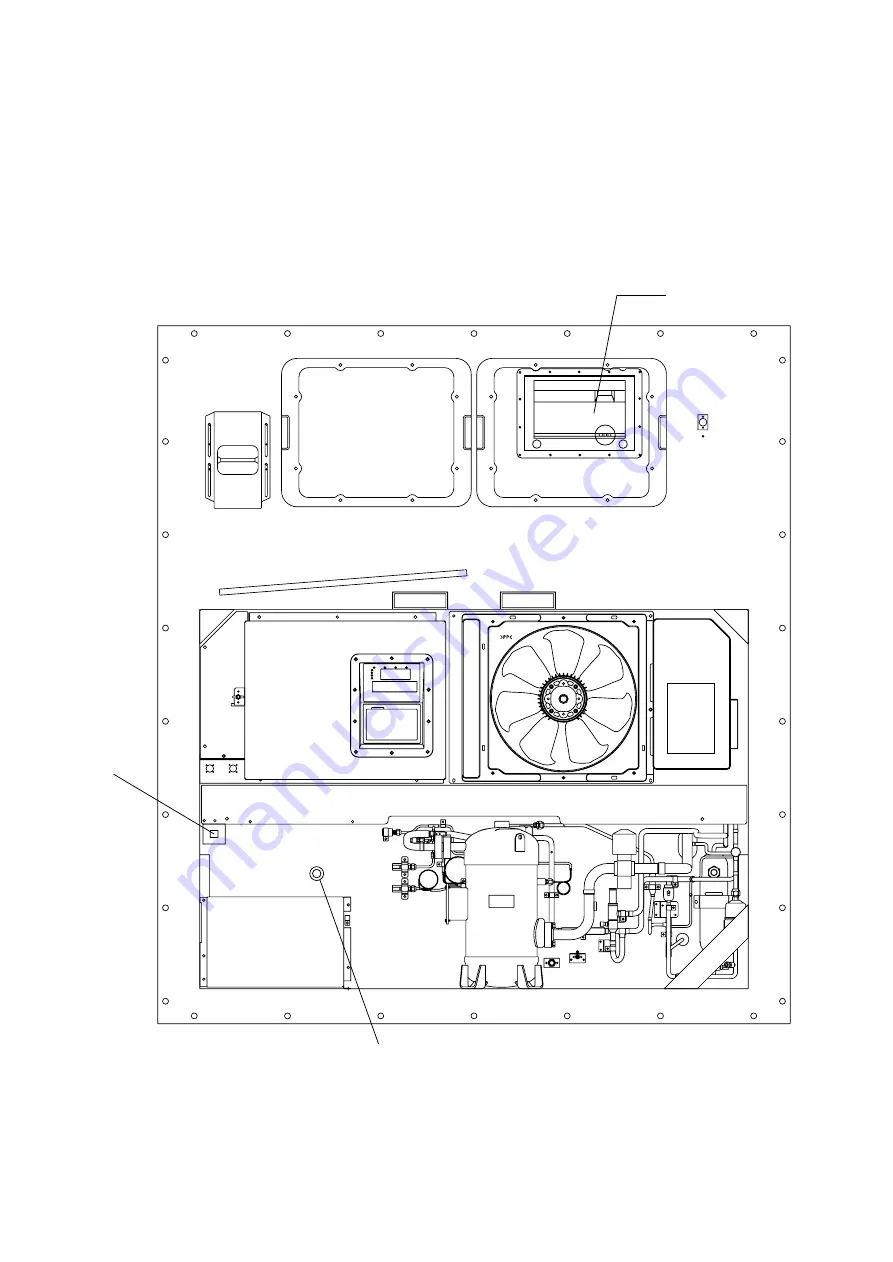
5-6
5.3 TransFRESH
Attachment for the TransFRESH CA devices are provided to control the internal atmosphere (quantity of O
2
and CO
2
).
Use the CA devices according to the Operation Manual supplied by TransFRESH. The controller and
sensor included in the CA devices are installed by the TransFRESH's agents before each transportation.
●
An example of installation of CA devices, outside.
q
TransFRESH SECURITY ENCLOSURE
w
TransFRESH COMMUNICATION BRACKET
e
TransFRESH Single purge port
q
w
e
TransFRESH
https://daikin-p.ru