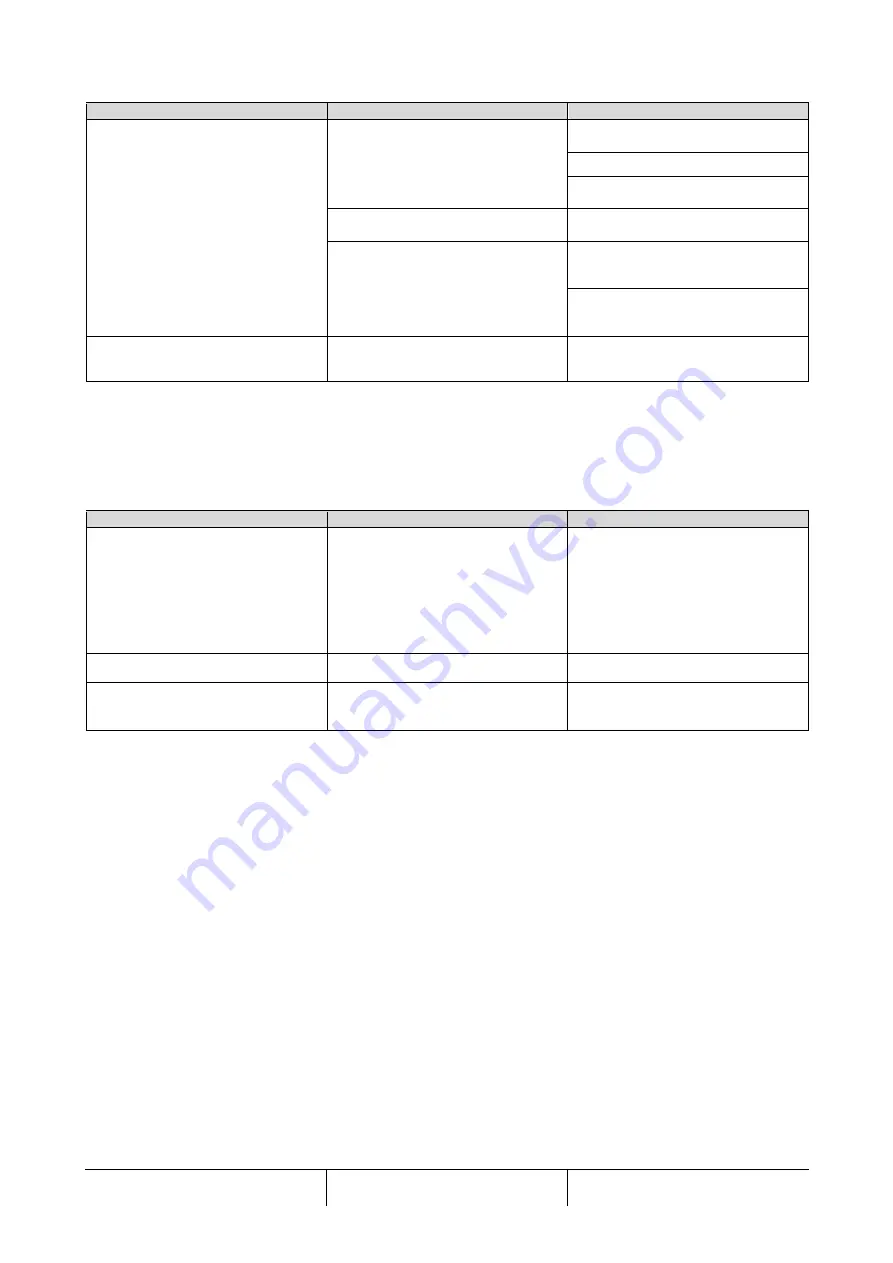
43/77
Operation Manual
D
–EOMWC00A07-16_02EN
Symptom
Cause
Solution
Unit status is Off.
All circuits are stopped immediately.
Bell icon is moving on controller’s
display. String in the alarm list:
HeatPCtrlrCommFail
String in the alarm log:
HeatPCtrlrCommFail
String in the alarm snapshot
HeatPCtrlrCommFail
Module has no power supply
Check the power supply from the
connector on the side of the module.
Check if LEDs are both green.
Check if the connector on the side is
tightly inserted in the module.
Module address is not properly set
Check if module’s address is correct
referring to the wiring diagram.
Module is broken
Check if LED are on and both green.
If BSP LED is solid red replace the
module.
Check if power supply is ok but LEDs
are both off. In this case replace the
module.
Reset
Notes
10.6 Unit Events
10.6.1
Password Over Time
This event indicates that one of the temporary passwords is going to expire in one day. To solve this it is possible to
activate another temporary password
Symptom
Cause
Solution
Unit status is Run.
Bell icon is moving on controller’s
display.
String in the alarm list, log and
snapshot:
Pass1TimeOver 1dayleft
Pass2TimeOver 1dayleft
PassTimeOver 1dayleft
Temporary Password Inserted is
going to expire. One day is left before
Option set is deactivated.
Activate another temporary password
or purchase a permanent license.
Reset
Notes
Local HMI
Network
Auto