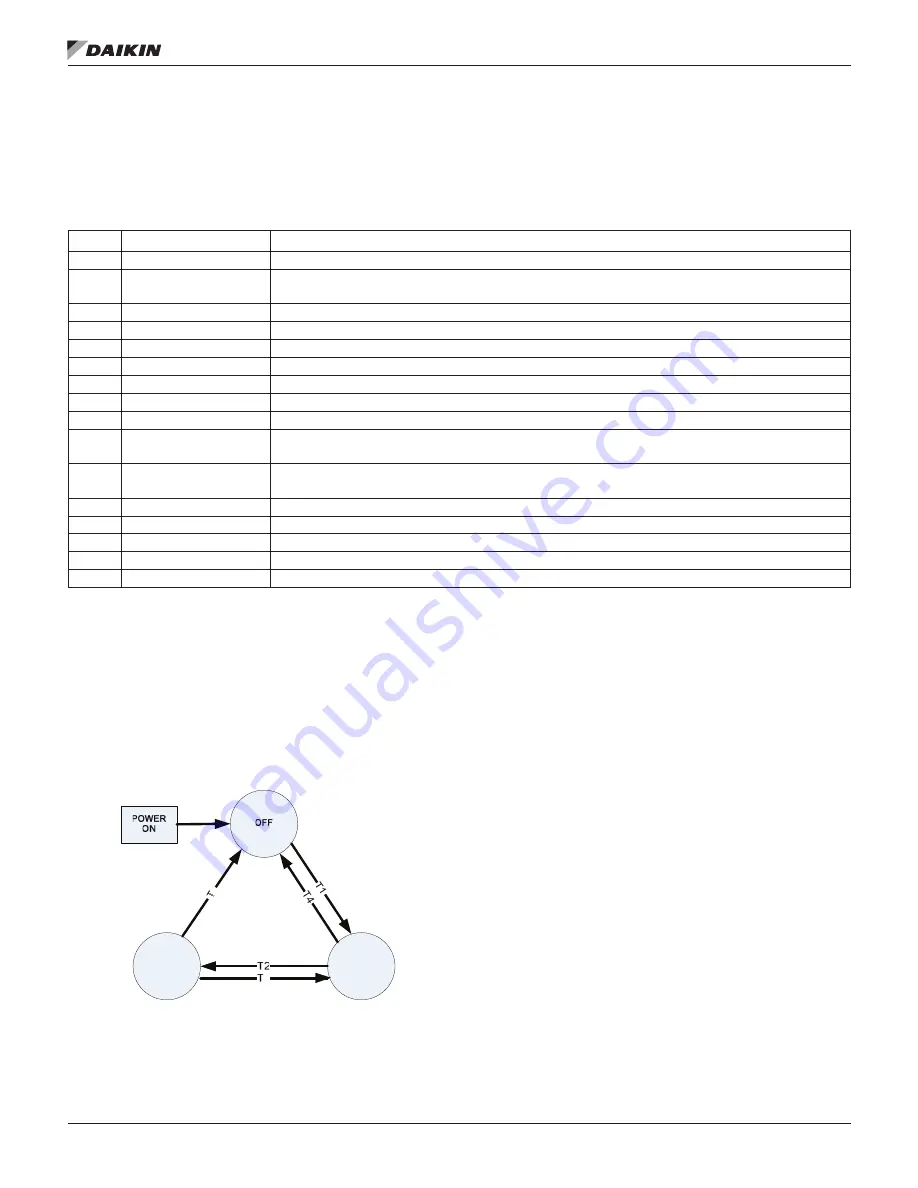
IOM 1264-1 • NAVIGATOR
®
MODEL WWV CHILLERS
26 www.DaikinApplied.com
u
nIT
f
unCTIons
Unit Status
Unit Status is displayed to indicate the general condition of the unit. The following table lists the text displayed for each unit status
and the conditions that enable each status. If more than one status is enabled at the same time, the highest numbered status
overrides the others and is displayed.
Table 27: Unit Status Conditions
#
Status
Conditions
0
AUTO
Unit State = Auto
1
OFF:All Cir Disabled
Unit State = Off and all circuits unavailable to start (temporary conditions are not considered to be a cause
of a circuit being unavailable)
2
OFF: Unit Alarm
Unit State = Off and manual reset Unit Alarm active
3
OFF: Keypad Disable
Unit State = Off and Unit Enable Set Point = Disable
4
Off: Remote Switch
Unit State = Off and Remote Switch input is Off
5
OFF: BAS Disable
Unit State = Off, Control Source = Network, and BAS Enable = false
6
OFF: Unit Switch
Unit State = Off and Unit Switch input is Off
7
OFF: Test Mode
Unit State = Off and Unit Mode = Test
8
AUTO: Wait For Load
Unit State = Auto, no circuits running, and LWT is less than the active set point + startup delta
9
AUTO: Evap Recirc or
Cond Recirc
Unit State = Auto and Evaporator State = Start or Condenser State = Start
10/11
AUTO: Wait Cond Flow or
Wait Evap Flow
Unit State = Auto, Evaporator State = Start and Flow Switch input is off, or Condenser State = Start and
Flow Switch input is off
12
AUTO: Pumpdown
Unit State = Pumpdown
13
AUTO: Max Pulldn Rate
Unit State = Auto, unit capacity limited by the evap EWT pulldown rate
14
AUTO: Unit Cap Limit
Unit State = Auto, unit capacity limit has been met or exceeded
15
OFF: Cfg Chg Rst Ctrl
A configuration change requiring a reboot has occurred but controller has not been rebooted yet.
16
OFF: Invalid Config
The unit configuration is not complete.
Evaporator Pump Control
Three evaporator pump control states for control of the
evaporator pumps.
1. Off - No pump on.
2. Start – Pump is on, water loop is being recirculated.
3. Run – Pump is on, water loop has been recirculated, and
circuits can start if needed.
T1 - Off to Start
- Requires either of the following to be true:
• Unit state = Auto
• Freeze protection started
T2 - Start to Run
- Requires the following to be true for time
longer than evaporator recurculate time set point:
• Evap state = Start
•
Evaporator flow switch input is on
T3 - Run to Off
- Requires all of the following to be true:
• Unit state = Off
• Freeze protection is not active
T4 - Start to Off
. - Requires all of the following to be true:
• Unit state = Off
• Freeze protection is not active
T5 - Run to Start
. - Requires the following to be true for longer
than the Evaporator Flow Loss Delay set point:
• Evap State = Run
•
Evaporator flow switch input is off.
START
RUN
3
5
Summary of Contents for Navigator WWV
Page 4: ......