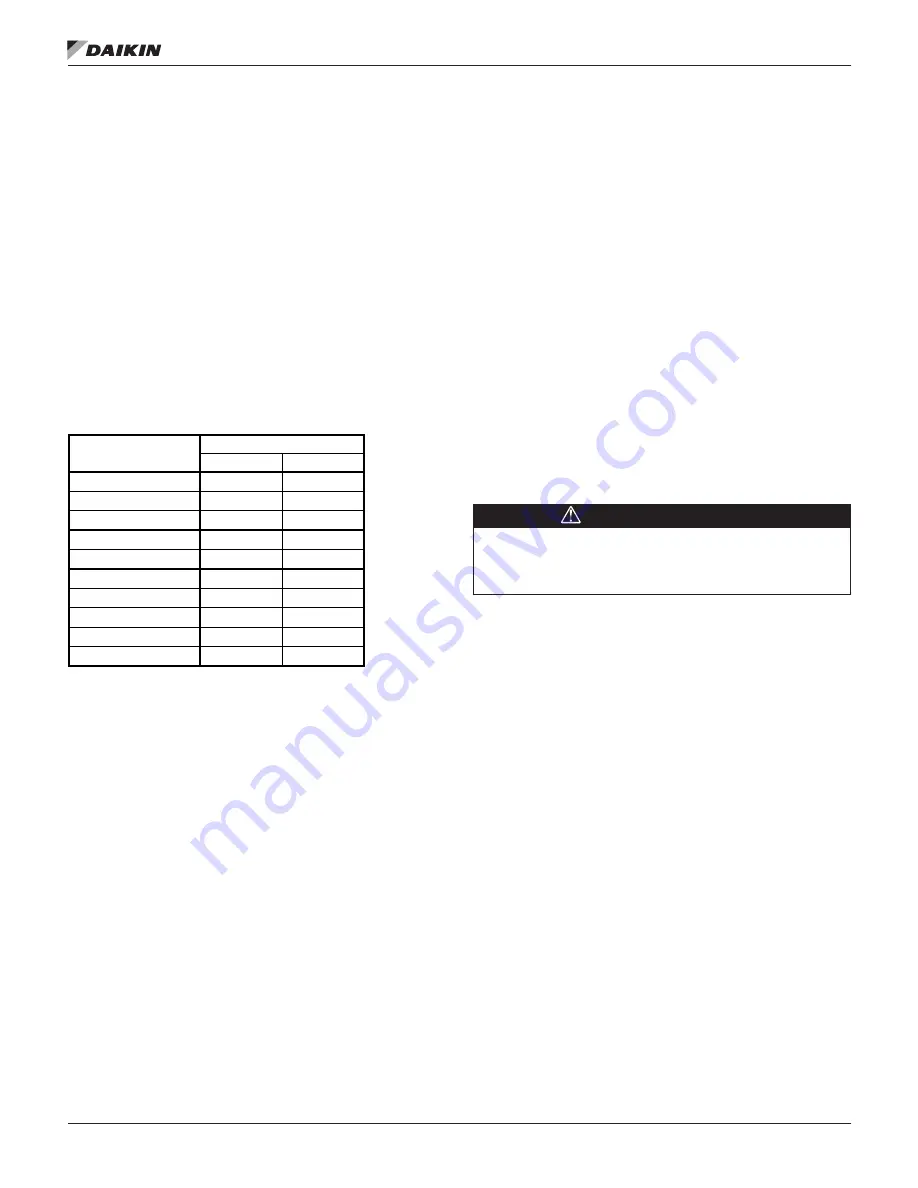
Installation and Application Considerations - Remote Evaporators
www.DaikinApplied.com 31
IOM 1242-8 • PATHFINDER
®
MODEL AWV CHILLERS
Installation and Application Considerations - Remote Evaporators
Shipment Method
AWV chillers with remote evaporators ship in three pieces.
• Outdoor condensing unit
• Remote evaporator
• Refrigerant specialties kit with the unit has the following
components for field installation:
—
Filter-drier housing and cores for field piping
—
Sight glass
—
Electronic expansion valve
—
Solenoid valve
—
Evaporator vent and drain shutoff valves - waterside
—
Charging valve (on non-economizer models)
—
Suction coupling and flange to attachment evaporator
—
Schrader valve
—
Liquid/saturated coupling and flange to evaporator
Table 4: Data for AWV Remote Evaporator Models
Performance Data
AWV performance data is available from the current version of
Daikin Sales Tools or the local sales office. There is a derate to
the performance of an AWV with remote evaporator due to field
installed refrigerant line losses, exceeding those found on the
packaged arrangement. Use the recommended pipe sizes from
Table 6 through Table 10 for design purposes.
Derate Procedure
1. Sketch the liquid and suction piping, including the actual
pipe lengths and all fittings.
2. From Table 5, add up the equivalent pressure drop for
the fittings in the suction line. Add this value to the actual
linear feet of tubing to determine the total equivalent
length (TEL) for the piping run.
3. Using Daikin Sales Tools, enter TEL values to determine
adjusted unit performance. Consult the Daikin Technical
Response Center for all remote evaporator piping
installations for review and approval.
Remote Evaporator Refrigerant Piping
Careful design of refrigerant piping is necessary for proper
system operation. Refer to the latest version of the ASHRAE
Handbook and the Daikin Applied Refrigerant Piping Design
Guide, AG31-011, for recommended refrigerant piping
. Design the
refrigerant piping to accomplish the following:
1. Assure proper refrigerant feed to the evaporator.
2. Provide practical and economical refrigerant line sizes
without excess pressure drop.
3. Maintain uniform oil return to the compressor under all
load conditions.
4. Keep the refrigerant suction line pressure drop to a
maximum of 2°F in saturated temperature equivalent.
5.
The velocity of each suction line must be sufficient to
return oil at 25% of the circuit rating for the application.
6. When facing the unit control box, the left-hand
compressor is circuit #1, and the right-hand is circuit #2.
7. The condenser cannot be used for refrigerant charge
isolation for service. The circuit charge will need to be
recovered for major service events.
IMPORTANT NOTE
Service Form SF99006 (current version available from the
local sales office) must be submitted to Daikin Technical
Response Center and reviewed at least two weeks prior to
beginning piping installation.
The following applies to all size units:
• New refrigerant piping must be used for all equipment
installations. Refrigerant piping must be properly sized for
the circuit capacity and unit refrigerant.
• Piping system must be brazed if copper or welded if steel
and have the proper lay out with all required components.
• Copper (Type L) piping is recommended; carbon steel
. Piping must be installed
per industry standards and local codes. Any welded pipe
requires a replaceable suction line filter at chiller connect
point.
• Measured actual pipe length cannot exceed 200 feet.
• Maximum total equivalent length (TEL) cannot exceed
300 feet (75 feet for vertical suction lines). The evaporator
cannot be located more than 20 feet above or 30 feet
below the outdoor unit.
• Suction line connection at unit = 4 1/8-inch OD each.
• Underground refrigerant piping is not permitted.
• Field piping must include adequate service taps for
checking filter-drier, subcooling, and superheat.
• Insulate complete suction lines. Liquid lines may be
insulated to prevent collection of condensation or loss of
subcooling if required.
• Ensure the braze rod used is appropriate for the
materials being joined.
Evaporator Model
Water Volume
(gal)
(L)
EV40271010/9
67
255
EV40271111/7
66
250
EV40271212/7
63
240
EV50271414/7
106
403
EV50271717/5
99
374
EV50391212/11
154
582
EV66331515/7
225
851
EV66391414/11
271
1027
EV66391616/9
263
995
EV66391717/7
259
979