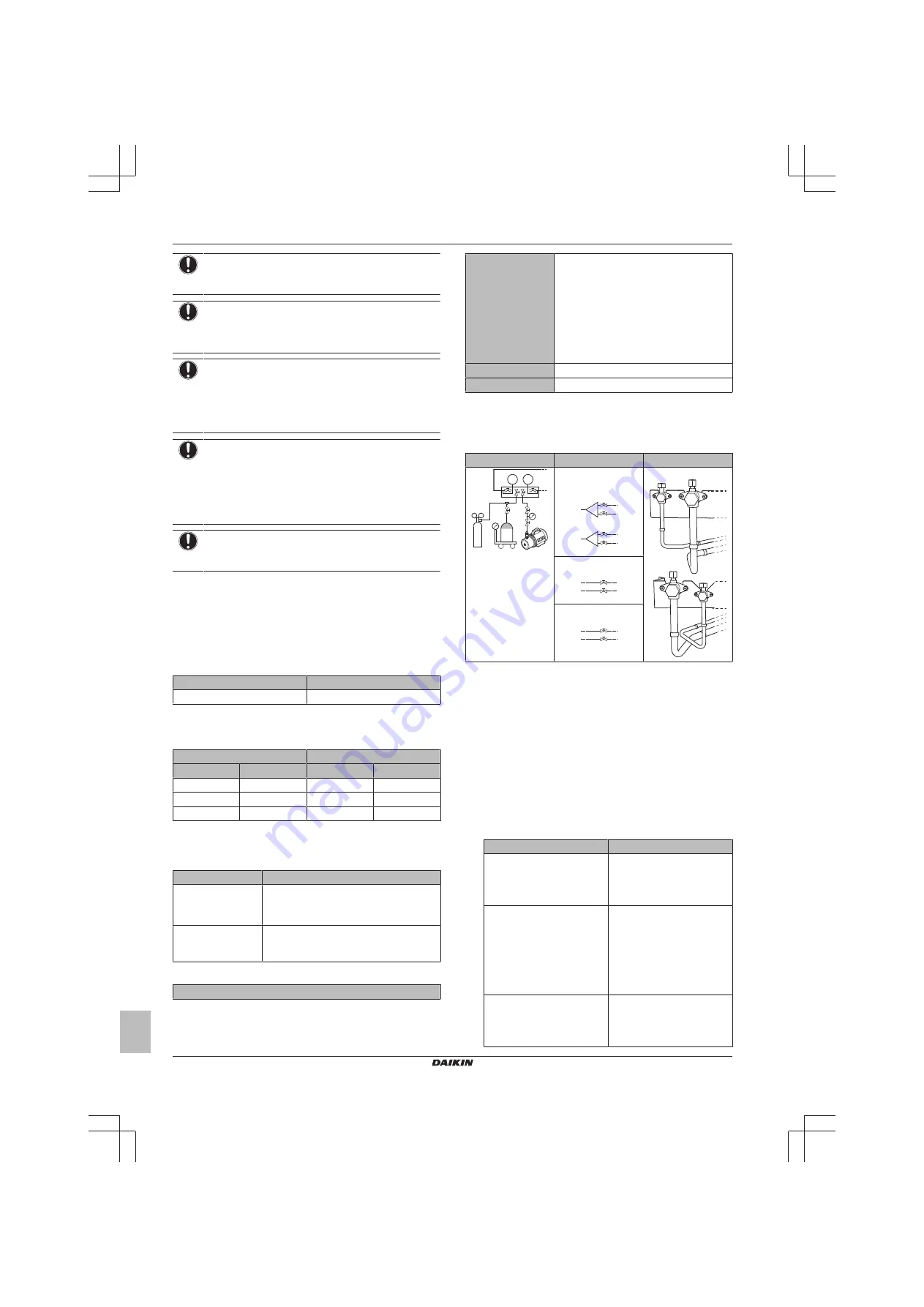
5 Installation
Installation and operation manual
12
RKXYQ5T7Y1B
VRV IV compressor unit for indoor installation
4P408443-1 – 2015.07
NOTICE
If the power of some units is turned off, the charging
procedure cannot be finished properly.
NOTICE
Be sure to turn on the power 6 hours before operation in
order to have power running to the crankcase heater and
to protect the compressor.
NOTICE
If operation is performed within 12 minutes after the
compressor unit, heat exchanger unit and indoor units are
turned on, the compressor will not operate before the
communication is established in a correct way between the
compressor unit, heat exchanger unit and indoor units.
NOTICE
Before starting charging procedures, check if the 7‑LEDs
display is as normal (see
"6.1.4 To access mode 1 or 2" on
), and there is no malfunction code on the user
interface of the indoor unit. If a malfunction code is
present, see
"8.1 Solving problems based on error
.
NOTICE
Make sure all connected units (heat exchanger unit +
indoor units) are recognised (setting [1‑5]).
5.6.2
To determine the additional refrigerant
amount
Additional refrigerant to be charged=R (kg). R should be rounded off
in units of 0.1 kg.
R=[(X
1
×
Ø12.7
)×0.12+(X
2
×
Ø9.5
)×0.059+(X
3
×
Ø6.4
)×0.022]×0.8+B
X
1...3
=Total length (m) of liquid piping size at
Øa
Model
B parameter (kg)
RKXYQ5
3.1
When using metric piping, please take into account following table
concerning the weight factor to be allocated. It should be substituted
in the formula for R.
Inch piping
Metric piping
Size (Ø) (mm)
Weight factor
Size (Ø) (mm)
Weight factor
6.4
0.022
6
0.018
9.5
0.059
10
0.065
12.7
0.12
12
0.097
5.6.3
To charge refrigerant
Charging refrigerant consists of 2 stages:
Stage
Description
Stage 1: Pre-charging Recommended in case of larger systems.
Can be skipped, but charging will take longer
then.
Stage 2: Manual
charging
Only necessary if the determined additional
refrigerant amount is
not reached
yet by
pre-charging.
Stage 1: Pre-charging
Summary – Pre-charging
:
Refrigerant bottle
Connected to the service ports of the stop
valves. Which stop valves to use depends
on the circuits you choose to pre-charge to:
▪ Circuits 1 and 2 together (manifold with
refrigerant line splitters required).
▪ First circuit 1, then circuit 2 (or vice versa).
▪ Only circuit 1
▪ Only circuit 2
Stop valves
Closed
Compressor
Does NOT operate
1
Connect as shown (choose one of the possible connections).
Make sure that all compressor unit stop valves, as well as valve
A are closed.
Possible connections:
Manifold
Connections
Compressor unit
p< p>
R410A
N2
b
c
e
a
d
B
A
Circuit 1 and 2
together
C
g
h
A
f
i
B
C
C
C
D
D
h
i
g
f
Only circuit 1
i
B
h
A
C
C
Only circuit 2
C
C
f
B
g
A
a
Pressure reducing valve
b
Nitrogen
c
Weighing scales
d
Refrigerant R410A tank (siphon system)
e
Vacuum pump
f
Liquid line stop valve (circuit 2: to indoor units)
g
Gas line stop valve (circuit 2: to indoor units)
h
Gas line stop valve (circuit 1: to heat exchanger unit)
i
Liquid line stop valve (circuit 1: to heat exchanger unit)
A, B, C
Valves A, B and C
D
Refrigerant line splitter
2
Open valves C (on line of B) and B.
3
Pre‑charge refrigerant until the determined additional refrigerant
amount is reached or pre‑charging is not possible anymore, and
then close valves C and B.
4
Do one of the following:
If
Then
The determined additional
refrigerant amount is
reached
Disconnect the manifold from
the liquid line(s).
You do not have to perform the
"Stage 2" instructions.
Too much
refrigerant is
charged
Recover refrigerant until the
determined additional
refrigerant is reached.
Disconnect the manifold from
the liquid line(s).
You do not have to perform the
"Stage 2" instructions.
The determined additional
refrigerant amount is
not
reached
yet
Disconnect the manifold from
the liquid line(s).
Continue with the "Stage 2"
instructions.