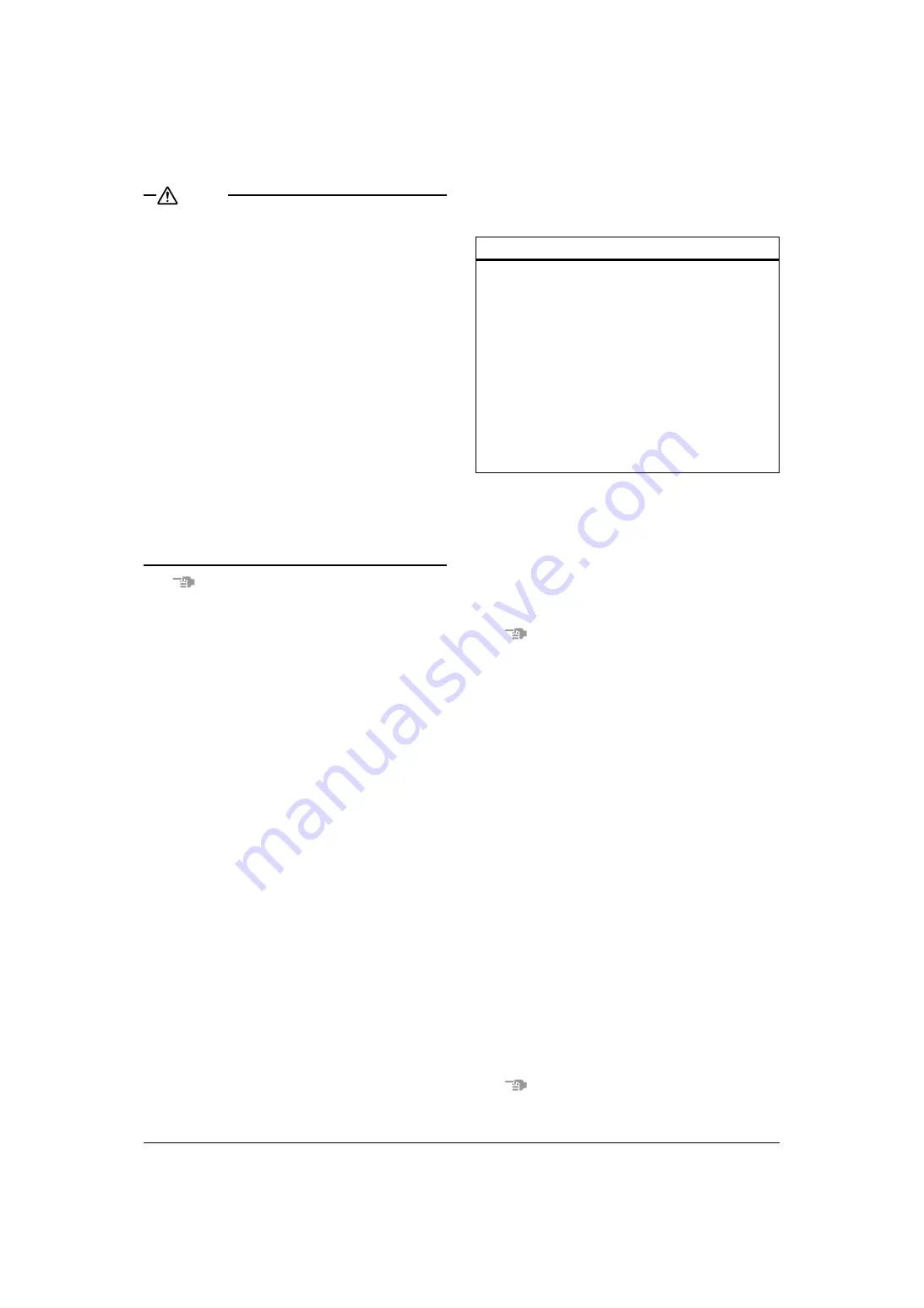
English
10
7.
FIELD WIRING
Caution
•
All field wiring and components must be installed by a licensed
electrician and must comply with relevant local and national
regulations.
•
Be sure to use a dedicated power circuit. Never use a power sup-
ply shared by another appliance.
•
Never install a phase advancing capacitor. As this unit is equipped
with an inverter, installing a phase advancing capacitor will not only
deteriorate power factor improvement effect, but also may cause
capacitor abnormal heating accident due to high-frequency waves.
•
Only proceed with wiring work after blocking off all power.
•
Always ground wires in accordance with relevant local and
national regulations.
•
This machine includes an inverter device. Connect earth and
leave charge to eliminate the impact on other devices by reducing
noise generated from the inverter device and to prevent leaked
current from being charged in the outer hull of the product.
•
Do not connect the ground wire to gas pipes, sewage pipes, light-
ning rods, or telephone ground wires.
Gas pipes :
can explode or catch fire if there is a gas leak.
Sewage pipes :
no grounding effect is possible if hard plastic pip-
ing is used.
Telephone ground wires and lightning rods :
dangerous when
struck by lightning due to abnormal rise in electrical potential in
the grounding.
•
Be sure to install an earth leakage circuit breaker.
This unit uses an inverter, so install the earth leakage circuit
breaker that be capable of handling high harmonics in order to
prevent malfunctioning of the earth leakage circuit breaker itself.
•
Earth leakage circuit breaker which are especially for protecting
ground-faults should be used in conjunction with main switch or
fuse for use with wiring.
Note
•
Electrical wiring must be done in accordance with the wiring dia-
grams and the description herein.
•
Do not operate until refrigerant piping work is completed.
(If operated before complete the piping work, the compressor may
be broken down.)
•
Never remove thermistor, sensor or etc. when connecting power
wiring and transmission wiring.
(If operated with thermistor, sensor or etc. removed, the compres-
sor may be broken down.)
•
This product have reversed phase protection detector that only
works when the power is turned on. If there exists black out or the
power goes on and off which the product is operating, attach a
reversed phase protection circuit locally. Running the product in
reversed phase may break the compressor and other parts.
•
Attach the power wire securely. Introducing power with a missing
N-phase or with a mistaken N-phase will break the unit.
•
Never connect the power supply in reversed phase.
The unit can not operate normally in reversed phase.
If you connect in reversed phase, replace two of the three phases.
•
Make sure the electrical unbalance ratio is no greater than 2%. If
it is larger than this, the unit’s lifespan will be reduced.
If the ratio exceeds 4%, the unit will shut down and an malfunction
code will be displayed on the indoor remote controller.
•
Connect the wire securely using designated wire and fix it with
attached clamp without applying external pressure on the termi-
nal parts (terminal for power wiring, terminal for transmission wir-
ing and earth terminal).
•
If there exists the possibility of reversed phase, lose phase,
momentary blackout or the power goes on and off while the prod-
uct is operating, attach a reversed phase protection circuit locally.
Running the product in reversed phase may break the compres-
sor and other parts.
7-1 Power circuit, safety device and cable
requirements
•
A power circuit (see the following table) must be provided for con-
nection of the unit. This circuit must be protected with the required
safety devices, i.e. a main switch, a slow blow fuse on each phase
and an earth leakage circuit breaker.
•
When using residual current operated circuit breakers, be sure to
use a high-speed type (0.1 second or less) 200mA rated residual
operating current.
•
Use copper conductors only.
•
Use insulated wire for the power cord.
•
Select the power supply cable type and size in accordance with
relevant local and national regulations.
•
Specifications for local wiring are in compliance with IEC60245.
•
Use wire type H05VV when protected pipes are used.
Use wire type H07RN-F when protected pipes are not used.
7-2 Wiring Connection Example for Whole System
(Refer to figure 17)
1.
Power supply
2.
Main switch
3.
Earth leakage circuit breaker
4.
Fuse
5.
Outdoor unit
6.
COOL/HEAT selector
7.
Remote controller
8.
Indoor unit
9.
BS unit
Note
•
Make sure the weak electric wiring (i.e. for the remote controller,
between units, etc.) and the power wiring do not pass near each
other, keeping them at least 50 mm apart.
Proximity may cause electrical interference, malfunctions, and
breakage.
•
Be sure to connect the power wiring to the power wiring terminal
block and secure it as described in “
7-5 Power Wiring Connec-
tion Procedure
”.
•
Transmission wiring should be secured as described in “
7-4
Transmission Wiring Connection Procedure
”.
•
Secure wiring with clamp such as insulation lock ties to avoid con-
tact with piping.
•
Shape the wires to prevent the structure such as the EL. COMPO.
BOX lid deforming. And close the cover firmly.
•
All field wiring is to be procured on site.
7-3 Leading wire Procedure
•
The power wiring and ground wiring are passed out from the
power wiring hole on the sides, the front (knock hole) or the bot-
tom frame (knock hole) .
•
The transmission wiring is passed out from the wiring hole (knock
hole) on the front of the unit or from a piping hole.
(Refer to figure 18)
1.
Electrical wiring diagram
2.
On the back of the EL .COMPO. BOX lid.
3.
Power wiring, ground wiring (inside conduit)
4.
(When the wiring is routed out through the side panel.)
5.
Transmission wiring
6.
Pipe opening
7.
Conduit
8.
For power wiring and ground wiring
9.
Through cover
10.
Cut off the shaded zones before use.
11.
Burr
12.
Knockout hole
13.
For transmission wiring
Note
•
Open the knock holes with a hammer or the like.
Phase and
frequency
Voltage
Minimum
circuit amp.
Recom-
mended fuses
REYQ18PY1
φ
3, 50Hz
380-415V
40.1A
45A
REYQ20PY1
φ
3, 50Hz
380-415V
41.2A
50A
REYQ22PY1
φ
3, 50Hz
380-415V
44.3A
50A
REYQ24PY1
φ
3, 50Hz
380-415V
45.4A
50A
REYQ26PY1
φ
3, 50Hz
380-415V
53.1A
60A
REYQ28PY1
φ
3, 50Hz
380-415V
54.2A
60A
REYQ30PY1
φ
3, 50Hz
380-415V
63.0A
70A
REYQ32PY1
φ
3, 50Hz
380-415V
63.0A
70A
REYQ34PY1
φ
3, 50Hz
380-415V
71.6A
80A
REYQ36PY1
φ
3, 50Hz
380-415V
72.7A
80A
REYQ38PY1
φ
3, 50Hz
380-415V
75.8A
90A
REYQ40PY1
φ
3, 50Hz
380-415V
76.9A
90A
REYQ42PY1
φ
3, 50Hz
380-415V
84.6A
100A
REYQ44PY1
φ
3, 50Hz
380-415V
85.7A
100A
REYQ46PY1
φ
3, 50Hz
380-415V
94.5A
110A
REYQ48PY1
φ
3, 50Hz
380-415V
94.5A
110A
Summary of Contents for VRV III REYQ18PY1
Page 23: ...3P201178 5 EM06A072 0702 FS ...