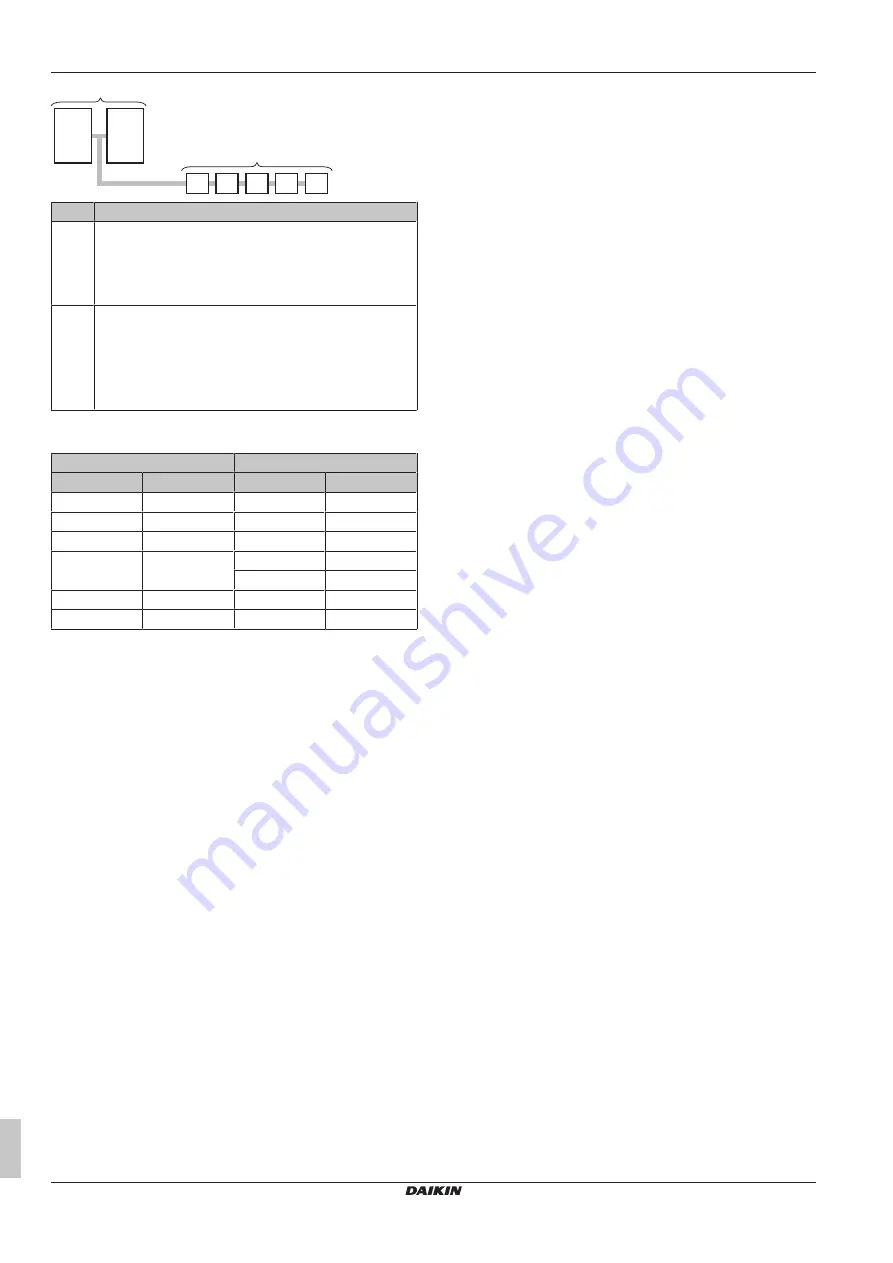
14 Piping installation
Installation and operation manual
26
RYYQ+RYMQ+RXYQ8~20U7Y1B
VRV IV+ heat pump
4P546220-1C – 2020.10
550
200
300
125
125
125 125 50
500
12 HP
8 HP
#
Action
1
Determine the connection ratio:
▪ Total outdoor unit capacity class = 500
▪ Total indoor unit capacity class = 550
=> CR≥100%
2
Determine parameter C:
▪ N=5
▪ 8 HP: N≥4 => C1=N×0.1=5×0.1 kg
▪ 12 HP: N<6 => C2=0 kg
=> C=C1+C2=0.5 kg
Metric piping.
When using metric piping, replace the weight factors
in the formula by the ones from the following table:
Inch piping
Metric piping
Piping
Weight factor
Piping
Weight factor
Ø6.4 mm
0.022
Ø6 mm
0.018
Ø9.5 mm
0.059
Ø10 mm
0.065
Ø12.7 mm
0.12
Ø12 mm
0.097
Ø15.9 mm
0.18
Ø15 mm
0.16
Ø16 mm
0.18
Ø19.1 mm
0.26
Ø18 mm
0.24
Ø22.2 mm
0.37
Ø22 mm
0.35